Il Just in Time è una metodologia di gestione della produzione che consiste nel produrre esattamente solo i quantitativi di ogni referenza richiesti nel breve periodo. Se si adotta questo approccio, le scorte non esistono o costituiscono piccole riserve che assicurano il rifornimento tra un centro di lavorazione e il successivo. Il Just in Time è stato giustamente definito una filosofia che coinvolge l’intera organizzazione aziendale e che ha come conseguenza la drastica riduzione delle scorte. Imperativo categorico è dunque rimuovere le scorte “superflue”, evidenziando e eliminando tutte le inefficienze e le disfunzioni organizzative.
Come possiamo passare dalla “filosofia” del Just in Time alla pratica del Just in Time?
Partiamo da un’osservazione che magari potrà sembrare banale ma che costituisce il fondamento di tutta la metodologia: un sistema produttivo senza scorte può fermarsi oppure può adeguarsi.
Ma come si fa a produrre con scorte a zero o molto basse? Le strade sono sostanzialmente queste:
- Produrre solo ciò che è richiesto dal mercato nel brevissimo periodo e quindi produrre a lotti pressoché unitari.
- Bilanciare i ritmi dei vari reparti.
- Implementare un perfetto sistema di trasmissione delle informazioni.
- Disporre di un layout di stabilimento adeguato.
Il Just in Time: un sistema “pull”
Con un “sistema pull”, ovvero con un sistema a trazione, le possibilità di riuscire a produrre solo quello che i clienti domandano e quindi di ottenere un livello di scorte prossimo allo zero, sono senz’altro molto buone.
Producendo sulla base degli ordini ricevuti, l’approvvigionamento dei materiali (materie prime e semilavorati) nel processo produttivo avviene in base ad un programma di produzione predeterminato, con particolare attenzione alle esigenze del reparto che li utilizza. Il ritmo produttivo è determinato sempre dal reparto (centro di lavorazione) più a valle che domanda al reparto più a monte la disponibilità dei materiali necessari.
Ma come si deve procedere in pratica? Si tratta di attuare le seguenti 4 fasi in successione:
- Determinare un programma di montaggio finale;
- Livellare il programma di montaggio finale;
- Sviluppare il programma principale di produzione;
- Fissare i programmi dettagliati di produzione per i vari centri di lavoro.
Il programma di montaggio finale viene elaborato anche con alcuni mesi di anticipo, ma viene via via rettificato all’avvicinarsi delle date effettive di produzione. All’inizio si tratta quindi di un piano basato su previsioni per finire ad essere un piano basato sostanzialmente sugli ordini clienti già acquisiti e tendenzialmente con una temporalità definita non troppo a lungo termine.
Il livellamento del programma di montaggio finale ha l’obiettivo di bilanciare il più possibile il ritmo di produzione e quindi l’impiego di tutte le risorse produttive. Il livellamento è guidato dal mercato e può essere attuato grazie alla possibilità di produrre a lotti molto piccoli.
Il programma principale di produzione non è altro che una sintesi giornaliera dei quantitativi da produrre per ogni articolo. I programmi dettagliati di produzione si ottengono dall’esplosione, mediante distinte base, del programma principale di produzione.
Il punto critico della logica pull è il “livellamento”, cioè deve essere possibile ed economico produrre a lotti unitari perché per avere una produzione equilibrata nel breve e brevissimo termine occorre produrre un po’ di tutto ogni giorno in lotti di montaggio tendenti all’unità.
Come trasmettere le informazioni in maniera rapida ed efficace? Con il sistema Kanban
Perché un sistema Pull possa funzionare correttamente è necessario disporre di una perfetta trasmissione delle informazioni: ogni operazione da effettuarsi all’interno di uno stabilimento deve essere opportunamente documentata affinché sia svolta nei tempi e nei modi corretti.
Un metodo molto semplice e al contempo rapido ed efficace di trasmissione delle informazioni è il cosiddetto sistema Kanban. Tale sistema si basa sulla circolazione di schede tra i vari centri di lavorazione e di stoccaggio all’interno di uno stabilimento. La consegna della scheda autorizza l’effettuazione di una determinata operazione.
Il sistema Kanban viene attivato dalla linea di assemblaggio finale che preleva pezzi dal proprio punto di stoccaggio in entrata e tramite le schede di movimentazione si risale all’area di stoccaggio del centro di lavorazione precedente e così via. In questo modo ogni centro di lavorazione sa esattamente cosa produrre e a quale ritmo produrlo e soprattutto produrrà solo ed esclusivamente ciò che il centro di lavorazione a valle utilizzerà.
Il layout di stabilimento di un sistema Pull
L’implementazione del sistema Just in Time richiede un insieme di interventi su diverse aree volti a migliorare l’efficacia del processo produttivo. Uno di questi riguarda persino il layout ossia la disposizione degli impianti all’interno dello stabilimento.
Per realizzare un layout adeguato per il sistema Pull, è necessario che:
- La produzione sia organizzata per centri di lavorazione: ogni centro di lavorazione deve avere un punto di stoccaggio in entrata e un punto di stoccaggio in uscita. Le scorte di materiali in corso di lavorazione e di parti componenti saranno collocate esclusivamente in queste aree.
- All’interno dello stabilimento ci sia un solo punto di rifornimento per ogni materiale.
- Siano precisati e definiti esattamente i percorsi di ciascun materiale attraverso i centri di lavorazione e le relative aree di stoccaggio.
In un’azienda tradizionale, generalmente, gli impianti di produzione sono completamente separati dai diversi magazzini destinati a conservare materie prime, semilavorati e prodotti finiti.
In un’azienda che utilizza un sistema Pull invece i magazzini per le materie prime e i prodotti finiti praticamente spariscono, mentre quelli per i semilavorati vengono sostituiti da piccole aree polmone che contengono scorte che coprono il consumo di ore, o al massimo di qualche giorno, e che sono tutte collocate necessariamente nell’area di produzione vicino ai centri di lavorazione. In questo modo i materiali prodotti, o in attesa di lavorazione, sono visibili da parte degli addetti che possono quindi accorgersi immediatamente di accumuli eccessivi, o viceversa di carenze di componenti, e prendere tempestivamente gli opportuni provvedimenti.
In queste aree polmone il magazzino automatico verticale rappresenta la migliore soluzione per lo stoccaggio misto di materie prime, semilavorati o prodotti finiti.
In primis consente di ridurre del 90% lo spazio a terra occupato dallo stock dei materiali e riduce ulteriormente l’area polmone concentrando in una piccola area tutte le operazioni di picking, velocizzando e semplificando l’attività degli operatori.
In secondo luogo, rende praticamente impossibile l’errore nell’operazione di picking. In un sistema Pull l’errore rappresenta un rischio notevole, perché se si opera secondo questo modello, tutto deve funzionare in modo lineare e perfetto, per non creare ritardi o fermi nella fase successiva della produzione.
Avere il pezzo giusto o il materiale necessario al posto giusto e al momento giusto diventa fondamentale, per l’efficienza di tutta la linea produttiva che si snoda intorno alla funzione cruciale del magazzino.
Un esempio di come il magazzino automatico verticale possa addirittura diventare il propulsore del passaggio alla filosofia just in time è raccontato qui: MT Marchetti e Modula: come stoccare 1.750 mq di materiale in 100 mq.
7+1 Peccati Mortali del Magazzino
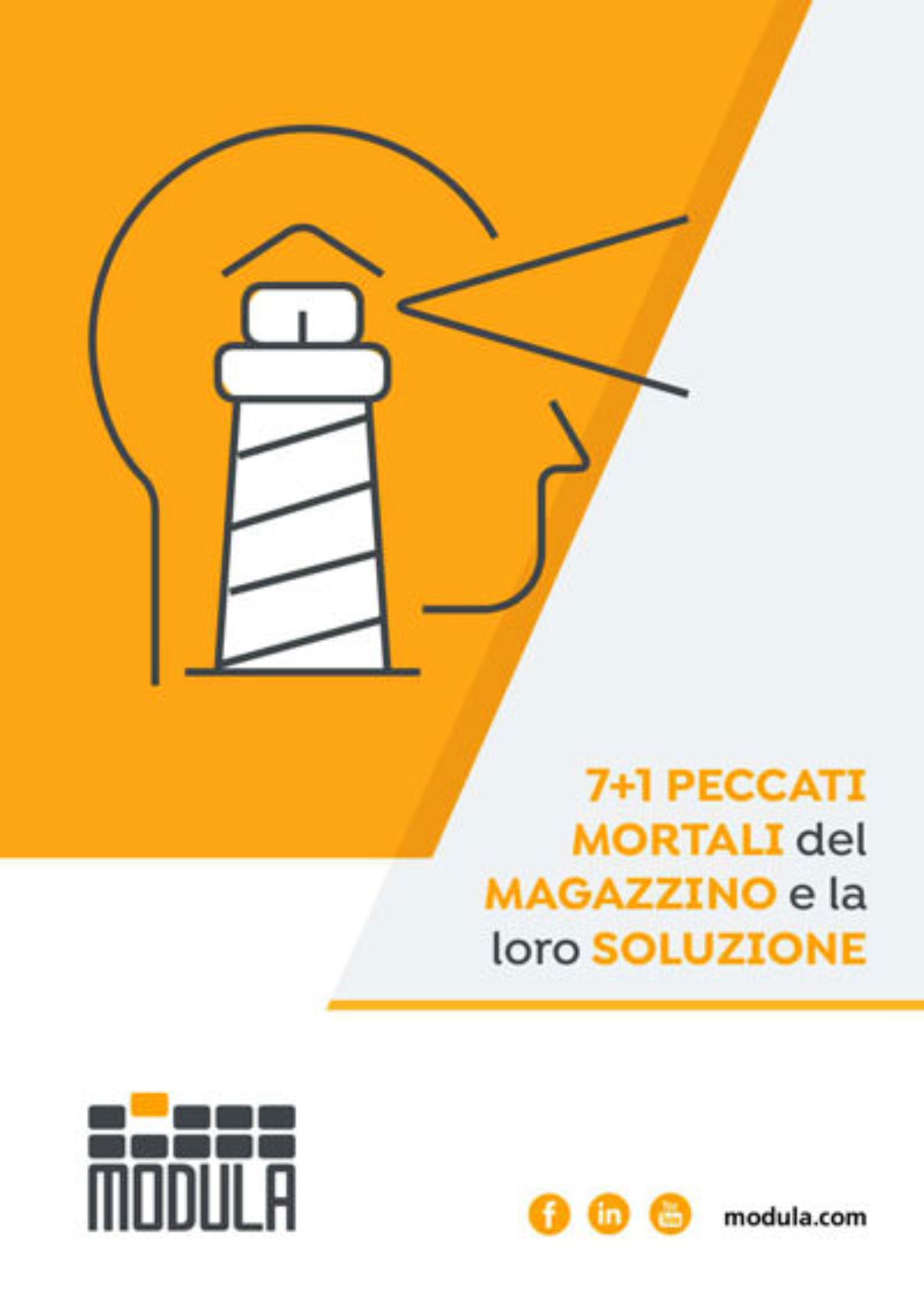