Dans les entreprises manufacturières, la gestion des stocks et la planification de la production doivent être étroitement liées. En fait, il existe des réalités commerciales dans lesquelles le dimensionnement des stocks de produits finis est un élément de la planification de la production. Dans ces cas, les stocks de produits finis peuvent être gérés avec des systèmes EOQ en essayant de minimiser les coûts de gestion et en tenant compte des contraintes financières, de l’espace, etc. Dans d’autres cas, les contraintes de production, en particulier les lots de production minimum, influencent fortement la gestion des stocks et, par conséquent, la taille des stocks de produits finis est une conséquence de la planification de la production. Ce sont l’environnement de production et la technologie disponible qui déterminent la prédominance de cette dernière activité sur la première et non l’inverse.
Résumons brièvement ce que les différentes zones de gestion occupent:
- La gestion des stocks s’occupe du dimensionnement correct des stocks de produits et de matériel. Article de fond sur les modèles de gestion des stocks: Comment gérer efficacement les stocks.
- La gestion des approvisionnements des produits finis dans une entreprise de production traite du dimensionnement, compatible avec les principales contraintes productives, des approvisionnements de produits finis.
- La planification de la production consiste à définir les plans ou les programmes de production et donc à établir quoi, combien et quand produire avec différents niveaux de détail et différents horizons temporels.
Qu’est-ce que cela signifie d’élaborer des plans de production ?
L’objectif fondamental de la planification de la production est d’organiser l’activité de production de manière à ce qu’elle soit cohérente avec les plans d’affaires qui définissent les objectifs économiques et financiers de l’entreprise entière à moyen terme (3-5 ans).
Plus précisément, il s’agit de coordonner les activités de production, avec leur propre logique de fonctionnement et leurs propres objectifs d’efficacité, avec les activités commerciales visant à suivre les tendances du marché et à satisfaire les exigences des clients. Si, d’une part, la production pour fonctionner au maximum de son efficacité (minimiser les coûts de production) nécessite des programmes de production aussi stables que possible dans le temps, d’autre part, le manque de coordination peut avoir de graves conséquences : stocks supérieurs à ceux requis et/ou manque de produit à stocker lorsque requis ou faible efficacité dans l’utilisation des moyens de production (donc coûts et inefficiences).
Plans de production
En général, les plans d’affaires définissent les objectifs économiques et financiers de l’ensemble de l’entreprise à moyen terme (3-5 ans). Les plans ou programmes de production définissent quoi, combien, quand et quand produire avec différents niveaux de détail et différents horizons temporels.
Fondamentalement, on peut distinguer 3 plans :
- Le Plan de Production Globale (PP) : concerne un horizon temporel assez long (1 an) et a pour objet la planification de paramètres quantitatifs très agrégés (nombre de pièces pouvant être produites, tonnes de produit fini, etc., au niveau global ou par famille de produits). L’objectif du plan global est de concilier les besoins en capacité de production (qui peuvent être attribués à la demande du marché) et la disponibilité réelle (exprimée en heures-homme ou en heures-machine).
- Le Plan de Production Principal ou Plan Directeur de Production (PDP) : concerne un horizon temporel limité (3-4 mois) et concerne les produits finis individuels. En particulier, le MPS vise à dimensionner les lots de production.
- Le Calendrier d’Assemblage Final (CAF) : concerne un horizon temporel très court (1 mois) et a pour objet l’assemblage-configuration du produit fini. La tâche typique du Plan final est le choix des modalités d’exécution des ordres.
La caractéristique principale de l’ensemble du processus de planification de la production est son caractère cyclique, de sorte que la même période fait l’objet de plusieurs plans successifs avec des degrés de définition croissants. On peut donc parler de phases de planification et de contrôle de la production: chaque phase s’ouvre avec la planification d’une période et se termine avec le contrôle qui ouvre la planification de la période suivante.
Phase 1: la préparation du plan d’ensemble
Parlant du processus de planification de la production, nous avons souligné son caractère cyclique : la même période fait l’objet de plusieurs plans successifs avec des degrés de définition croissants. Le processus se déroule ensuite en phases : chaque phase commence par la planification d’une période et se termine par le contrôle qui ouvre la planification de la période suivante.
En tant que données d’entrée, nous pouvons distinguer :
- Prévisions de ventes et/ou commandes clients.
- Les caractéristiques du système de production et les conditions normales d’exploitation : quarts de travail, heures, lots minimaux et multiples, disponibilité nette de main-d’œuvre des absences et des inefficacités, etc.
- La disponibilité actuelle et optimale (stocks en main + commandes – engagés) des produits finis, semi-finis et matériaux.
- Les normes de consommation des matériaux (à travers la nomenclature des matériaux des produits).
- Les normes des ressources productives (à travers les cycles de travail).
Dans la pratique, le plan de production global vise à comparer et à concilier les besoins et la disponibilité des matériaux et autres ressources productives sur une période assez longue (généralement un an).
Le détail des valeurs est généralement mensuel et concerne des paramètres plutôt agrégés (familles). Il est habituellement révisé une fois par mois (mais aussi moins fréquemment) avec la technique du roulement (il ferme un mois et ajoute un mois suivant).
En particulier, en ce qui concerne les moyens de production réels (personnes et machines), il est important de vérifier que la capacité et la disponibilité sont cohérentes tant pendant toute la période examinée (l’année) que pendant les différentes sous-périodes (mois).
Si ce n’est pas le cas, les mesures suivantes doivent être prises, selon le problème :
- Utilisation de la sous-traitance.
- Augmentation ou réduction de la capacité de production à certaines périodes par le biais d’heures supplémentaires, d’horaires de travail flexibles, de congés, etc.
- La production passe des périodes avec besoins excédentaires aux périodes avec disponibilité excédentaire.
En ce qui concerne la gestion des matières, il est nécessaire d’établir des accords avec les fournisseurs à long terme, dans le but de réserver la capacité de production des fournisseurs, de négocier les prix et les méthodes d’approvisionnement.
A ce stade, la première phase est terminée : le plan global est prêt.
Phase 2 : la préparation du plan principal
Le plan de production principal ou plan directeur de production (PDP) concerne un horizon temporel limité (3-4 mois) et concerne les produits finis individuels et leurs quantités relatives. Le PDP est en fait l’outil de planification de la production qui a pour tâche de dimensionner les lots de production, en tenant compte des contraintes de capacité de production présentes dans chaque période.
En d’autres termes, le MPS répond aux questions suivantes : que produire ? Quand la production doit-elle avoir lieu ? Quelle quantité mettre en production ?
Puisqu’il s’agit d’un plan de production dérivé de la planification à long terme agrégée (avec un niveau de détail plus élevé), le PDP doit avoir un horizon temporel inférieur ou égal à l’horizon temporel du plan global et doit être supérieur ou égal au délai de fabrication des produits planifiés. En général, la fréquence de révision de ce plan est hebdomadaire ou mensuelle.
Les données d’entrée dans le PDP sont :
- Prévisions de commandes et de ventes pour les produits.
- Niveau des stocks de produits.
- Stocks de sécurité pour les différents produits.
- Temps de production des différents produits.
Plan de production global avec contraintes de capacité de production.
Comme déjà mentionné, le SPM est un plan dérivé du plan global, il devra respecter les contraintes déjà établies précédemment en termes de ressources maximales disponibles (quantités de composants ou heures).
Lors de sa préparation, il sera donc nécessaire d’évaluer la capacité de production nécessaire (plan de capacité) à la fois par rapport à la main-d’œuvre disponible et par rapport à la disponibilité des machines à utiliser. Si la capacité disponible n’est pas suffisante pour répondre aux besoins planifiés, un équilibre sera nécessaire, par exemple en augmentant les ressources (heures supplémentaires si possible) ou en anticipant ou planifiant la production.
En résumé, la rédaction d’un PDP se fait généralement selon la procédure suivante :
- Identification de l’horizon temporel de référence.
- Formulation d’un premier projet de MPS à partir des prévisions et des commandes déjà reçues.
- Réalisation d’une analyse de capacité, au moyen de simulations de faisabilité du plan de production proposé.
- Révision du MPS ou modification de la capacité disponible, si nécessaire selon le point précédent, jusqu’à ce qu’une solution réalisable soit trouvée.
Phase 3 : préparation du plan de l’Assemblée finale
Le calendrier de montage final (FAS) concerne un horizon très court (de 1 à 4 semaines) et a pour objet le montage/configuration des produits finis. En d’autres termes, c’est le Plan qui définit ce qu’il faut produire et dans quel ordre au niveau du poste de travail et du centre d’usinage unique (on parle donc d’articles individuels, de variantes de produits, d’emballages, etc.) en tenant compte de la disponibilité réelle des matériaux et des heures-homme ou des machines.
La définition du SAF pour une période donnée doit être effectuée conformément à ce qui a été précédemment établi dans le SPM. En effet, la quantité totale pouvant être obtenue pour un ensemble donné (article) ne doit pas dépasser celle prévue pour les composants communs au niveau du SPM. Au lieu de cela, au niveau des variantes de produits, l’assortiment peut également varier si des stocks de sécurité sont prévus pour les composants spécifiques de chaque article individuel.
Le FAS est l’outil de planification de la production qui a pour tâche de :
- Vérifier la disponibilité des matériaux et des composants comme programmé.
- Garantir le respect des délais de livraison des produits finis tels qu’établis.
- Gérez les niveaux de stock des articles dans les magasins aux niveaux les plus bas possibles.
- Réglementer les activités de production, d’achat et d’émission d’ordres.
Les activités précédemment prévues au niveau du PDP (achat de matières premières et de composants, réalisation de travaux internes donnant lieu à des produits semi-finis, etc.) Dans les cas où le processus d’achat et/ou la conception des produits ont lieu sur commande, en l’absence de prévisions, toutes les activités sont planifiées directement au niveau du FAS. Dans ce cas, le SAF pourra donc s’étendre sur des horizons plus longs et être révisé moins fréquemment (de la même manière que le SPM).
40 KPI de magasin pour contrôler et mesurer les performances
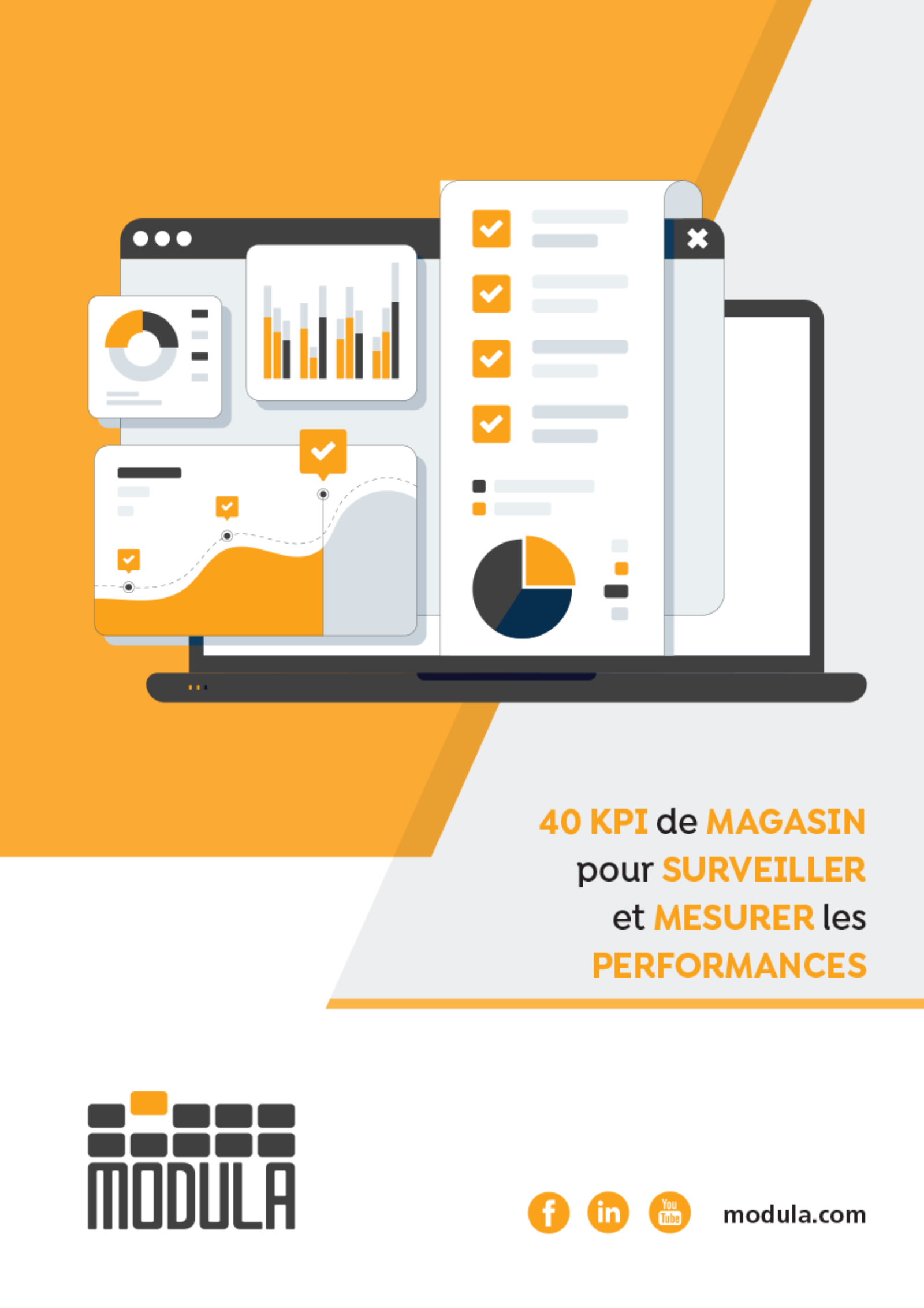