La simulazione dinamica è una tecnica basata su modelli matematici che cerca di prevedere il comportamento di un sistema o di un edificio se si propongono scenari alternativi.
Nata per minimizzare i rischi, è facile che si appoggi a programmi e sistemi di simulazione 3D, mappando tutti i processi logistici di un’Azienda e confrontando diversi scenari, la simulazione dinamica è in grado di individuare rischi, colli di bottiglia o semplicemente fluttuazioni dei flussi esterni ed interni della filiera logistica e nel contempo di controllare in maniera efficiente le prestazioni del sistema, verificandone costantemente eventuali deviazioni da valori di benchmark operativi fissati in fase progettuale.
Le principali aree di intervento della simulazione dinamica sono:
- Verifica ed ottimizzazione del layout dei sistemi di stoccaggio e di handling (tradizionali e/o automatizzati). Lo scopo è l’individuazione e la rimozione dei colli di bottiglia, nonché l’ottimizzazione degli investimenti (value engineering)
- Verifica ed ottimizzazione delle strategie e delle tattiche per il corretto utilizzo di sistemi di stoccaggio e di handling, da implementare poi sui software di gestione operativa o di controllo dell’automazione, quali: politiche di messa a dimora, ottimizzazione del picking, assegnazione delle missioni ai carrellisti o agli AGV in funzione di vari scenari di utilizzo (giorno medio, di picco, sbilanciamenti nel mix, guasti, ecc.)
- Verifica ed ottimizzazione delle modalità di pianificazione e gestione della produzione, carico macchine, ecc
- Pianificazione dell’attività giornaliera di un Centro di Distribuzione, con la verifica dell’effetto di varie alternative nell’impiego delle risorse disponibili, grazie ad un modello di dettaglio
- Comparazione delle prestazioni teoricamente raggiungibili dal proprio sistema attuale con quelle realmente raggiunte (benchmarking)
- Raffinata presentazione animata 3D dei sistemi oggetto di studio
Il metodo che viene seguito per l’esecuzione di una simulazione dinamica, ad esempio di un magazzino automatico (ma il metodo è sostanzialmente uguale anche per altre categorie di impianti), è riassumibile nei seguenti passi:
- Definizione obiettivi, raccolta dati e validazione del modello concettuale
Ogni sistema può essere variamente modellizzato in funzione degli obiettivi da conseguire. Una simulazione del magazzino richiede input accurati (flussi, prestazioni, regole di gestione etc.), quindi la raccolta dati è una fase molto delicata. Il modello concettuale ha lo scopo di far condividere da tutto il team di progetto gli scenari da verificare, le ipotesi e le assunzioni fatte. - Sviluppo del modello software e progetto della campagna di esperimenti
Una volta “tradotto” nel linguaggio di simulazione dinamica del magazzino il modello concettuale, si definiscono gli scenari da testare e il grado di confidenza atteso per la comparazione dei risultati di output e quindi si stima il numero di run da lanciare. - Elaborazione degli output e loro interpretazione
In questa fase è preziosa la competenza di un simulatore che sia esperto anche di logistica; in questa circostanza il valore aggiunto viene fornito è la capacità di trasformare le indicazioni numeriche in soluzioni di progetto. - Illustrazione dei risultati e formulazione delle raccomandazioni
Anche il migliore studio, se non è capace di “comunicare” i suoi risultati, si rivela inutile. Questa fase è molto importante per aiutare il Cliente a prendere le decisioni. In genere, assieme ad un documento report, si impiega un’animazione 3D, che mostri le situazioni “critiche” ed il mezzo usato per risolverle.
Come ottimizzare le operazioni di picking in magazzino?
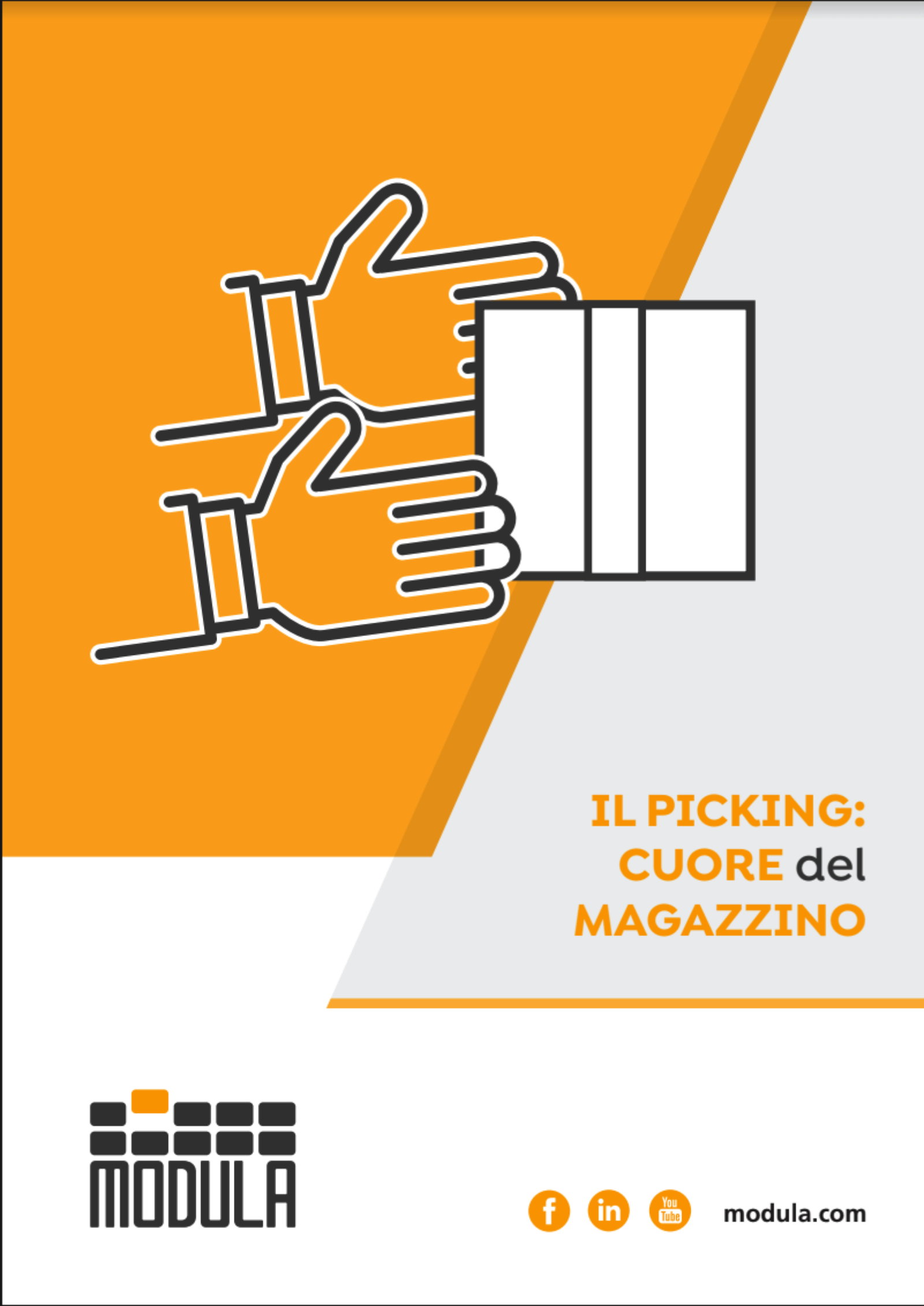