Automatisierte Lager und automatische Kommissionierung sind für viele Unternehmen zur Realität geworden und für viele andere eine Notwendigkeit. Aber sie sind nicht alle gleich, lassen Sie uns kurz die Vor- und Nachteile der verschiedenen Arten von automatisierten Lagern betrachten:
- Mehrturm-Lager
- Vertikales Karussell
- Horizontales Karussell
- Miniload
- Lager mit Regalbediengerät
- Shuttle
- Vertikaler Puffer oder Microload
1. Mehrturm-Lager
Das Mehrturm-Lager ist ein vertikales Lagersystem mit verschiebbaren Trägern und mehreren Türmen zur hochfrequenten Ein- und Auslagerung von leichten Artikeln. Die Organisation der Produkte in den Trägern ermöglicht die optimale Nutzung des verfügbaren Platzes im Lager.
Die Träger sind im Allgemeinen unterteilt und können an jeden Lager- und Umschlagsbedarf angepasst werden, um den Warenfluss im Lager erleichtern.
Vorteile
- Kurze Zykluszeiten und schneller Zugriff die Materialien
- Optimierung des Materialflusses
- Hohe Produktivität
Nachteile
- Geringere Nutzlast des unteren Trägers im Vergleich zu denen eines VLM (automatisches vertikales Lagersystem mit Träger)
- Die durchschnittliche Zugriffszeit auf den Träger ist länger als beim VLM
2. Vertikales Karussell
Bei dem vertikalen Karussell handelt es sich um ein vertikal entwickeltes automatisches Lager, das auf dem Konzept der „rotierende Regale“ basiert: Das Karussell besteht aus einer Reihe von Regalen, die innerhalb der Maschine in beide Richtungen vertikal rotieren und das Lagergut auf dem schnellsten Wege an den Entnahmeort bringen.
Diese Art von Lager nutzt den vertikalen Raum optimal aus und garantiert einen schnellen Zugriff auf die gelagerten Materialien. Diese Strategie reduziert die Zeit, die normalerweise für traditionelle Regallösungen benötigt wird, erheblich.
Vorteile
- Hohe Anzahl an Picking-Zyklen
- Raumoptimierung und Reduzierung des Platzbedarfs im Lager
- Sehr kompakte Außenabmessungen, insbesondere in der Tiefe, weil, im Vergleich zum VLM, kein zentraler Korridor für
- den Aufzug notwendig ist
- Sehr schnelle Zugriffszeiten und ergonomische Entnahmeposition
- Gut organisierte Lagerung von Kleinteilen
- Hohe Lagerdichte (über dem VLM) bei Maschinen mit reduzierter Höhe
- Ideal für Umgebungen mit begrenztem vertikalem Raum
Nachteile
- Begrenzte Tragfähigkeit sowohl in Bezug auf jedes einzelne Regal als auch auf die gesamte Struktur
- Keine Flexibilität beim Laden. Die Fächer haben eine feste Höhe und es ist nicht einfach, die Höhe der Ladung zu einem
- späteren Zeitpunkt zu ändern
- Nicht für die Lagerung von sperrigen oder besonders schweren Materialien geeignet
- Die Höhe der Maschine kann, wenn sie neu positioniert wird, nicht geändert werden
- Ein einzelner Input-/Output-Punkt
- Die Reparaturarbeiten der Maschine sind im Falle eines schweren Unfalls sehr kompliziert und gefährlich, da die beiden
- Drehachsen möglicherweise verdreht sind
Es stehen verschiedene Modelle zur Verfügung, die je nach Nutzlast auf dem Regal, der maximalen Nutzlast des Systems und den Gesamtabmessungen variieren.
3. Horizontales Karussell
Das horizontale Karussell ist dem vertikalen sehr ähnlich, außer dass es horizontal angeordnet ist, so dass die Rotationsachse nicht vertikal, sondern horizontal ist.
Dieses System besteht auch aus rotierenden Regalen, die sich in beide Richtungen drehen und das Material auf kürzestem Weg zum Bediener bringen. Aufgrund der horizontalen Ausrichtung ist die Pickingposition ergonomisch gesehen nicht immer die beste.
Diese Art von System kann eine gute Lösung sein, wenn es Höhenbeschränkungen gibt, wie z. B. bei einem niedrigen Dach.
Vorteile
- Dies ist die beste Lösung, wenn die Höhe begrenzt ist oder der Raum lang und eng ist (z. B. Korridore)
- Hohe Produktivität
- Lager können nebeneinander installiert werden, um den Durchsatz weiter zu erhöhen
- Es gib ein paar Doppelkarussellmodelle
Nachteile
- Effizienz ist auf bestimmte Bedingungen beschränkt
- Der Arbeitsplatz ist nicht sehr ergonomisch
- Ev. Probleme mit Unwuchten
- Nicht für die Lagerung von sperrigen oder besonders schweren Materialien geeignet
4. Miniload
Das Miniload ist ein automatisches Hochleistungslager mit einer ein- oder zweimastigen Struktur für die Handhabung leichter Lasten.
Diese Art von Lager besteht aus einer Reihe von Regalen, die parallel zueinander angeordnet und durch schmale Gänge unterteilt sind, entlang derer sich die Krane des Regalbediengeräts bewegen. Die Ladeeinheiten werden in den Zellen im Regal gelagert. Der Miniload holt die Ladeeinheiten ab und bringt sie in den Picking-, Verpackungs- oder Versandbereich.
Die Systeme sind je nach Auslagerungsanforderung mit einer oder mehreren Entnahmen ausgestattet. Das größte Plus dieser Lösung ist, dass sie ein vollautomatisches Pickingsystem bietet und somit eine hohe Produktivität, Geschwindigkeit und Sicherheit garantiert.
Vorteile
- Es können verschiedene Arten von Ladeeinheiten verwendet und transportiert werden
- Sehr hohe Nutzlast möglich
- Es ist auch möglich, sehr hohe Einheiten auf dem gesamten verfügbaren vertikalen Raum im Lager zu lagern
- Möglichkeit auch Pakete zu verwalten
- Hohe Gesamtleistung
Nachteile
- Begrenzte Laufzeiten wegen nur einer Input-/Output-Position für jeden Kanal
- Hohe Kosten
- Lange und teure Installation
- Die Kapazität der Ladeeinheiten und ihres Innenraums ist aufgrund der Form und Größe der gelagerten Ware nicht immer zu 100 % nutzbar
- Nicht für die Lagerung von sperrigen oder besonders schweren Materialien geeignet
5. Lager mit Regalbediengerät
Das Lager mit Regalbediengerät ist ähnlich wie beim Miniload, aber im Gegensatz zu diesen ist es für den Transport und die Lagerung von Paletten und allgemein schweren Materialien konzipiert.
Das System besteht aus einem mobilen Fahrwerk und einem Masten, entlang dessen ein Hubschlitten geführt wird, das horizontal einen Korridor zwischen zwei Regalen entlang fährt. Diese Art von automatisierter Lösung wird in Lagern mit einer Höhe von mehr als 12 Metern eingesetzt.
Vorteile
- Kann verschiedene Arten von Ladeeinheiten verwalten: Paletten, Container, etc.
- Kann sehr schwere und sperrige Materialien lagern
- Erreicht große Höhen
- Vollautomatisches System
Nachteile
- Im Allgemeinen ziemlich langsam
- Nicht geeignet für die Lagerung von kleinen Gegenständen
- Eher teuer und schwer zu implementieren
6. Shuttle
Ein automatisiertes Lager-Shuttle-System besteht aus einer Reihe paralleler Regale, die durch einen engen Korridor unterteilt sind, in dem sich die Shuttles bewegen, um Material von den Lagerplätzen zu entnehmen und zum Aufzug zu transportieren, der sich an einem Ende des Korridors befindet.
Sobald die Ware den Aufzug erreicht, wir sie abgesenkt, bis sie den Entnahmepunkt erreicht. Während der Beladephase wird der Vorgang umgekehrt.
Diese Art von System ist äußerst effizient und bietet eine sehr hohe Produktivität. Dieses System lässt sich einfach installieren und leicht skalieren, da es je nach Bedarf mit weiteren Regalen, Shuttles und Aufzügen nachgerüstet werden kann.
Es wird im Allgemeinen zusammen mit anderen Systemen, wie z. B. Miniloads eingesetzt, um die Produktivität des gesamten Lagers effizienter zu gestalten.
Vorteile
- Pickinggeschwindigkeit, sehr hohe Effizienz
- Einfach zu installieren, einfach zu skalieren
- Vielseitig, in der Lage, verschiedene Arten von Materialien zu verwalten
- Das Shuttle entlastet das Regalbediengerät in seinem Kanal, das daher unterschiedlich groß sein kann
Nachteile
- Begrenzte Betriebshöhe
- Nicht für die Handhabung von sperrigen oder schweren Produkten geeignet
7. Vertikaler Puffer oder Microload
Dies ist ein neuartiges automatisches Lager für die Ein- und Auslagerung von kleinen, leichten Komponenten.
Diese Art von Lager besteht aus einem Regalsystem, das die Träger im Innern automatisch bewegt. Die echte Neuheit im Vergleich zum Vertical Lift Module (VLM) ist die Pickingstation: Die Materialien werden dem Bediener in einer um 20 °C geneigten Ebene präsentiert, die ihm somit maximale Ergonomie garantiert.
Der vertikale Puffer eignet sich besonders für die Lagerung von Materialien mit geringer Bewegungsfrequenz und damit für die Entnahme kleiner Mengen unterschiedlicher Materialien durch die Möglichkeit, bis zu 4 verschiedene Artikel in einem Arbeitsgang aufzunehmen. Das Verfahren ist denkbar einfach: Während der Bediener einen Artikel aufnimmt, bereitet die Maschine den zweiten Auftrag vor, nachdem die erste Entnahme erfolgt ist, dreht das Modul die Schublade um 180°, um die zweite Schublade für die Entnahme bereitzustellen.
Der Microload kann daher als VLM der neuesten Generation definiert werden, mit der Besonderheit, dass es einen internen Aufzug gibt, der anstelle von einem einzelnen Träger hier 4 oder 5 kleine Träger verwaltet.
Wenn der Bediener einen Auftrag mit 4 verschiedenen Artikeln vorbereiten muss, die in 4 verschiedenen Trägern im Lager untergebracht sind, muss das traditionell VLM 4 verschiedene Pickingvorgänge ausführen, während der Vertikale Puffer über einen internen Aufzug verfügt, der in einem einzigen Vorgang die 4 Schubladen nimmt und sie zur Pickingstation bringt. Dies garantiert zwangsläufig eine höhere Anlageneffizienz.
Vorteile
- Hohe Pickinggeschwindigkeit, bis zu 4-mal höher als ein VLM
- Lagerung von Komponenten in Kartons mit Standardabmessungen und fehlender Identifizierung
- Die Träger werden schräg und damit ergonomischer in den Pickingbereich gebracht
- Möglichkeit der Installation des Vertikalpuffers in gekühlten Bereichen bis zu -20 °C
- Geringeres Bodengewicht als der VLM oder das Karussell
Nachteile
- Nicht für die Lagerung von sperrigen oder besonders schweren Materialien geeignet
- Maximale Belastung pro kleiner Träger 25 kg
- Maximales Gewicht pro Aufzug 125 kg
- Maximale Nutzlast der Maschine 40.000 kg – die Konstruktion ist sehr leicht
Optimierung der Logistik dank innovativer technologischer Lösungen
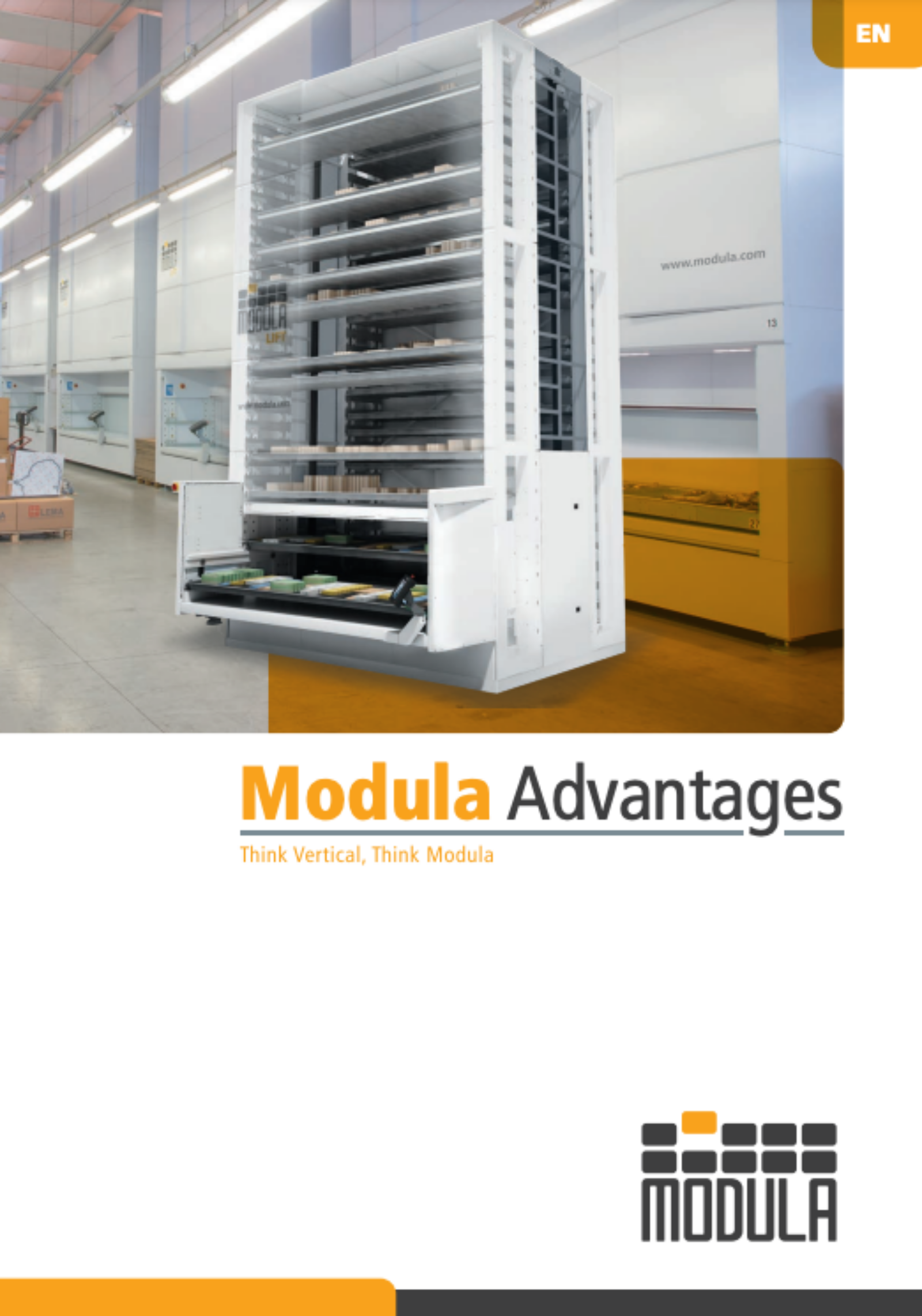