Il magazzino ricopre un ruolo fondamentale all’interno delle aziende. Non può solamente essere interpretato come un’entità fisica, ma come una parte importante della catena produttiva e come tale deve essere gestito tramite operazioni strategiche aziendali.
I magazzini, negli anni, sono cambiati. Ora possono espandersi anche all’esterno per svariate ragioni che vanno dall’outsourcing ma anche a seguito di politiche di approvvigionamento e di produzione.
Capita quindi di dover riprogettare interamente un magazzino per massimizzare le prestazioni e per eliminare problematiche dispendiose in termini di denaro quali la mancanza di spazio e il tempo perso a ricercare gli articoli all’interno di un ambiente estremamente ampio e poco organizzato quale è il magazzino.
Ma come si può riprogettare un magazzino, massimizzando le prestazioni ed evitando di stravolgere il budget? Quali sono gli step da seguire?
Inizialmente si possono attivare delle azioni di miglioramento continuo volte ad eliminare i piccoli problemi quotidiani (consegne dirette da parte dei fornitori, riprogettare gli imballaggi in modo da occupare meno spazio, migliorando le modalità di previsione). Successivamente la direzione dovrà attivarsi per effettuare interventi più sostanziosi, investendo in modo concreto nella riprogettazione del magazzino, affidandosi a consulenze di esperti del settore logistico.
In dettaglio, qui di seguito, vengono proposte le diverse fasi per progettare un magazzino automatico:
1. Diagramma di Gantt e stima dell’investimento per un magazzino automatico
Stimare l’investimento significa fare doverose analisi che dimostrino l’adeguatezza dell’intervento rispetto agli obiettivi posti. È molto importante effettuare delle stime sulle durate dell’intervento, schedulando degli obiettivi operativi, considerando anche che l’attività potrà non rispettare i tempi di esecuzione stabiliti.
Il consiglio è quello di farsi aiutare da esperti con esperienze maturate nel campo. In questo modo sarà più semplice effettuare stime analogiche, ovvero quelle basate su attività passate, oppure stime parametriche sul campione di lavoro già eseguito.
Ma riprogettare l’intero magazzino risulterà redditizio? Entro quanto tempo?
Costruire un nuovo magazzino o affidarsi a nuove tecnologie ha un costo che va quantificato e splittato nel tempo spesso aiutandosi con un’analisi Gantt.
Questo diagramma cartesiano rappresenta le attività e indica quando un’attività deve iniziare e finire. Nelle ascisse si dispone la scala temporale dall’inizio alla fine del progetto, e nelle ordinate le cose da fare per portare a termine il progetto. Inserite tutte le attività stimate si avrà una visione completa del progetto. A colpo d’occhio si vedrà a cosa dare la priorità, quanto manca alla scadenza, quali attività svolgere contemporaneamente per risparmiare tempo o quali attività dipendono da altre.
Il diagramma di Gantt serve a tenere sotto controllo lo svolgersi tempestivo di un insieme di attività. Può essere corredato da un insieme di informazioni: chi deve svolgere il compito, se ci lavora a tempo pieno o part time, quanta parte del lavoro è stata fatta e quanta resta da fare.
2. Audit e studio di fattibilità
Bisogna partire analizzando i punti di forza e debolezza, e definire gli interventi in funzione dello scopo che si vuole ottenere e dell’obiettivo che si vuole raggiungere. Si parte con una verifica delle prestazioni del magazzino per individuare ed eliminare le criticità: in questo modo si va a costruire l’audit.
Ci si deve concentrare sugli indicatori di prestazione, sui processi, strumenti, tecnologie e costi impiegati e non ultimo sulle risorse umane coinvolte.
Affidandosi allo studio di fattibilità si possono risolvere i problemi e migliorare i risultati operativi. Analizzando i dati, si vanno ad individuare le alternative in termini di organizzazione, stoccaggio e logistica, si confrontano e si sceglie quella con il miglior rapporto costi e benefici.
Le soluzioni alternative andranno a considerare vari aspetti quali il master plan del sito, il layout del magazzino, i criteri operativi e logistici, le risorse umane e i costi da impiegare e le tempistiche. Sulla base di tutte le informazioni emerse la direzione aziendale potrà scegliere la migliore alternativa possibile con la quale proseguire.
Per tutti i dettagli leggi l’articolo su come si redige un audit e sullo studio di fattibilità.
3. Slotting: la predisposizione dei prodotti
Per ottenere il minor costo di gestione del magazzino e minori spostamenti, i prodotti vanno collocati in modo migliore nell’area di picking. Mappando e analizzando lo storico delle attività del magazzino si può capire dove mettere i prodotti all’interno del magazzino automatico e quali articoli posizionare vicini.
L’analisi di Slotting permette di capire dove posizionare e come classificare i prodotti all’interno del magazzino per risparmiare tempo e ottimizzare le risorse.
Per tutti i dettagli leggi l’articolo sull’ottimizzazione di Slotting.
4. Progetto di dettaglio
Nel momento in cui si è valutato che ha senso fare l’investimento e si vuole procedere, occorre fare un’analisi del progetto di dettaglio. Questo significa entrare nel merito di aspetti funzionali, tecnici, gestionali, sistemistici che si erano accennati nello studio di fattibilità.
Approfondendo e analizzando i dati di progetto si determina un layout definitivo con disegni, piante, sezioni e particolari.
Il progetto logistico si deve integrare con gli aspetti edili (ad esempio nei magazzini automatici è possibile considerare un’implementazione in esterno detta coibentazione, talvolta valutando anche soluzioni antisismiche) e impiantistici (ad esempio impianti di sprinkler, riscaldamento, raffrescamento, illuminazione e aria compressa).
Si definiscono poi le procedure operative e si stila un Gantt di dettaglio.
5. Simulazione dinamica
La simulazione dinamica cerca di prevedere il comportamento di un sistema o di un edificio se si propongono scenari alternativi. Partendo da una mappatura dei processi logistici dell’azienda e confrontando diversi scenari, individua rischi e colli di bottiglia e controlla le prestazioni del sistema.
Si parte dalla raccolta dei dati e dalla validazione del modello concettuale per condividere con tutto il team di progetto gli scenari da verificare, le ipotesi e le assunzioni fatte. Si procede con la definizione degli scenari da testare e il grado di confidenza atteso per la comparazione dei risultati di output. Si trasformano le indicazioni numeriche in soluzioni di progetto e si illustrano i risultati per aiutare il cliente nel prendere le decisioni.
Per tutti i dettagli leggi l’articolo sulla simulazione dinamica per minimizzare i rischi nella logistica.
6. Progetto costruttivo
L’analisi dinamica si rivela preziosa quando si deve poi procedere al progetto costruttivo. Una volta definito il progetto e stabiliti i fornitori, si procede a un esame critico dei disegni costruttivi e si revisionano i vari documenti relativi all’automazione.
Partendo dal Gantt di progetto che l’azienda ha redatto, si procede con l’aggiornamento dello stesso sulla base delle decisioni prese e del progetto costruttivo che sicuramente inficerà il flusso e le date.
Si passa poi all’accettazione dei FAT (Factory Acceptance Test) con documentazione preparata da tutti i fornitori. Si tratta dell’ispezione delle apparecchiature e dei componenti prima della consegna o dell’ispezione finale.
Garantendo l’alto livello qualitativo dei componenti si assicura anche l’integrità all’interno della fabbrica. Tramite una prova di funzionalità convenzionale o una simulazione, si attesta che l’impianto o le apparecchiature rispettano le specifiche e gli obblighi contrattuali. Ciò comporta la verifica di documenti quali manuali e ogni sorta di istruzioni, progetti, disegni, diagrammi delle condutture e delle strumentazioni.
Questo avviene anche per i magazzini automatici verticali che ad esempio possiedono un libretto di istruzioni, un libretto di manutenzione, una dichiarazione di conformità e altri documenti ad esempio in caso di garanzie o certificazioni TÜV.
Questi documenti sono fondamentali in caso di ispezioni periodiche ad esempio sia in cantiere che dopo.
È molto importante dotarsi di un Project Leader che segua tutte le fasi di implementazione del progetto, poiché il monitoraggio del lavoro dei fornitori e la supervisione del Commissioning è fondamentale fino alla fase del Site Acceptance Test, dove il sistema viene testato in conformità ai piani di test e alle specifiche tecniche, per mostrare che il sistema è installato correttamente e si interfaccia con altri sistemi e periferiche all’interno del suo ambiente di lavoro.
Nel caso del Magazzino automatico questa fase si conclude con la fase di installazione e collaudo del software WMS e il suo eventuale interfacciamento con ERP aziendale.
Questa fase si conclude con il documento di hand-over.
Idee per la riorganizzazione del magazzino
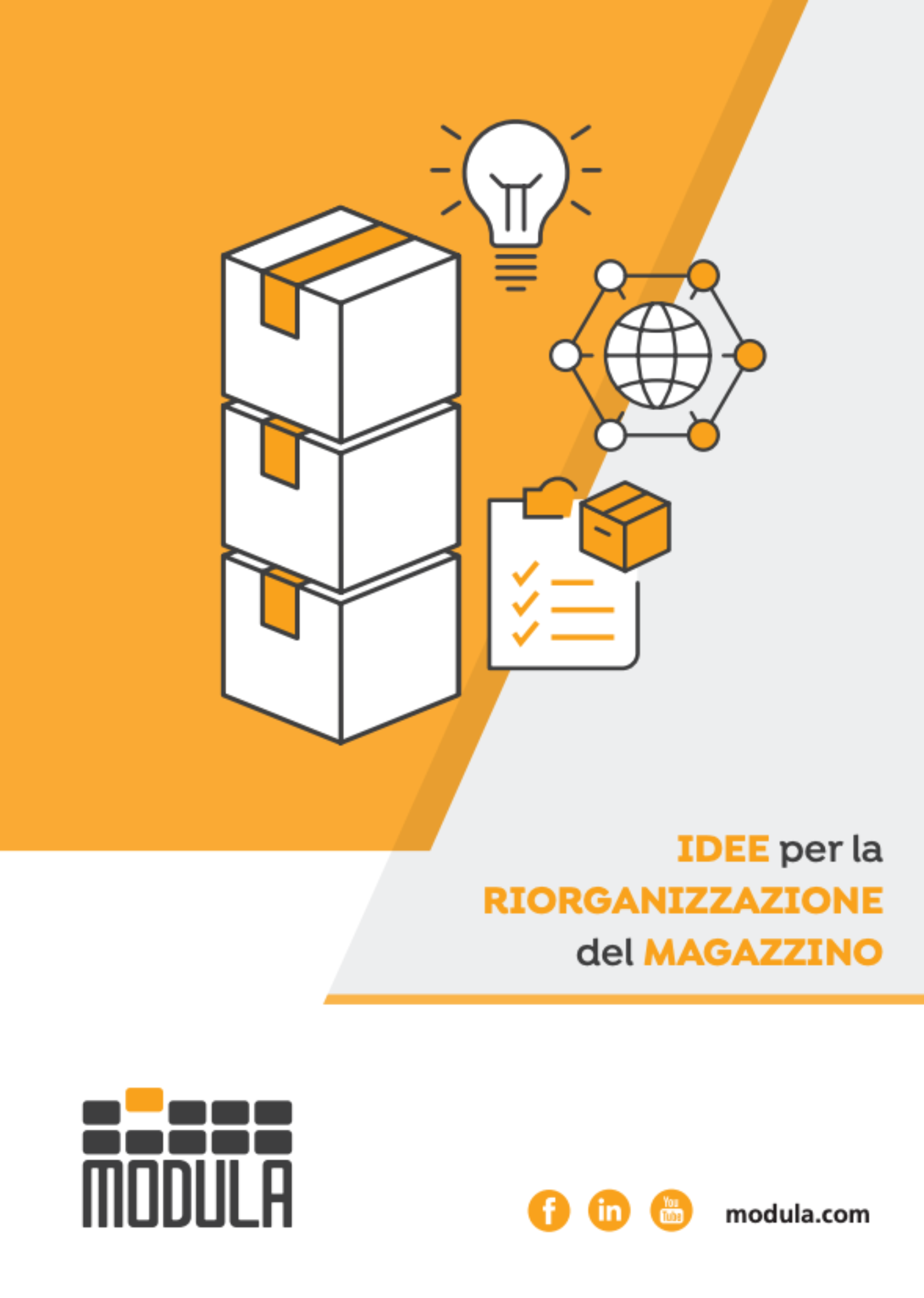