El sistema MRP (Material Requirement Planning) es un sistema de planificación de la demanda de materiales adecuado para la gestión de los componentes necesarios para la elaboración de productos acabados.
Es una técnica ya conocida, utilizada para planificar los pedidos de producción y de compra, teniendo en cuenta la demanda del mercado, las especificaciones y los lead times de producción.
Si pensamos en un gestor de stock que gestiona sus materiales utilizando los modelos tradicionales (Wilson y sus variantes), podemos imaginar que uno de los problemas principales será calcular la demanda correcta de estos materiales. De hecho, los modelos tradicionales generalmente suponen que la demanda futura será análoga a la pasada (demanda histórica media).
Esto es correcto mientras la demanda sea regular, pero ¿qué ocurre en caso contrario?
¿Y si la demanda se concentra en algunos períodos (cuando se pone en producción el producto acabado de referencia) y después se reduce a cero? El error está en la base: la demandade estos materialesno se debe prever sinocalcular sobre la base de la demanda del producto acabado. La programación de la producción debe establecer la cantidad de productos acabados que será necesario producir, y de estas cantidades se puede deducir la demanda real de materiales que los componen.
Los inputs del sistema MRP son 3:
El programa de producción (MPS)
El programa de producción (MPS) indica las cantidades a producir de cada referencia en un determinado intervalo de tiempo. Generalmente el horizonte temporal al que se refiere el programa de producción es a corto plazo. Para definir las cantidades a producir se deben tener en cuenta las previsiones de la demanda de un producto dado, los pedidos en mano ya recibidos y todos los vínculos derivados del sistema productivo. Además, se debe intentar definir cantidades a producir bastante regulares.
Las especificaciones
Las especificaciones constituyen el documento que define la estructura de un producto, que detalla los elementos (materias primas, componentes, productos intermedios, subensamblados, material auxiliar) que componen un determinado producto acabado. Las especificaciones de un producto constan de varios niveles (generalmente el producto acabado constituye el «nivel cero», sus componentes el «nivel 1», los componentes de los componentes el «nivel 2», etc). Mediante las especificaciones se pasa de los programas de producción de los productos acabados a los de sus componentes. La operación mediante la cual un ensamblado se transforma en la lista de sus componentes se denomina «despiece».
El estado del stock
El estado del stock es el archivo constantemente actualizado de los materiales y componentes de reserva en almacén.
Pero ¿cómo funciona el sistema MRP? Cálculos, muchos cálculos…
Podemos sintetizar el funcionamiento del sistema MRP definiendo los cálculos a realizar. Se trata de 5 fases:
Cálculo de las demandas brutas
Las demandas brutas de componentes de primer nivel se deducen de los pedidos a emitir (o lanzar) de productos acabados. Este cálculo se repite «en cascada» hasta agotar las especificaciones. De los pedidos a emitir de componentes de primer nivel se deduce la demanda bruta de componentes de segundo nivel, y así sucesivamente.
Cálculo de las demandas netas
Las demandas netas de cada producto acabado, componente, ensamblado, subensamblado se deben calcular teniendo en cuenta las existencias de cada uno. La demanda neta se obtiene restando de la demanda bruta las existencias en mano al final del período anterior. Las demandas brutas y netas se deben calcular con exactitud: la fecha en la que deben estar disponibles los productos acabados figura en el plan de producción, mientras que las fechas de los componentes se calculan hacia atrás, teniendo en cuenta los respectivos lead times de producción o de compra.
Cálculo de los pedidos a recibir
Conociendo las demandas netas de cada producto acabado, componente, ensamblado, subensamblado, es posible determinar los pedidos a recibir, o sea, calcular las cantidades que efectivamente por cada uno se recibirán, teniendo en cuenta los lotes mínimos prefijados (de producción o de compra). Si no hay vínculos sobre la cantidad a pedir o a producir, los pedidos a recibir coinciden con las demandas netas.
Cálculo de los pedidos a emitir
Los pedidos a emitir son las cantidades a pedir (o a producir) por cada producto acabado, componente, ensamblado, subensamblado. Las cantidades coinciden con los pedidos a recibir pero son anteriores en el tiempo del lead time.
Cálculo del stock en mano al final del período
La última fase consiste en determinar el stock al final del período. A las existencias disponibles al principio del período hay que añadir los pedidos a recibir y restar las demandas netas relativas al período. Naturalmente, el cálculo se debe repetir con cada producto.
Ventajas y limitaciones del sistema MRP
El sistema MRP es preferible a los sistemas por punto de pedido o intervalo fijo si la gestión concierne a materiales destinados a la producción, sobre todo si el producto final es complejo (con especificaciones en varios niveles).
En estos productos es posible evidenciar las siguientes ventajas respecto de los sistemas tradicionales:
- Comporta niveles de stock más bajos.
- No necesita previsiones precisas (necesariamente basadas en datos del pasado) ya que mira al futuro y gestiona mejor los artículos con demanda altamente variable.
- Es una herramienta de programación válida que pone en evidencia los pedidos con retraso e indica si estos retrasarán o no el plan de producción.
En cuanto a los límites, el objetivo principal de un sistema MRP de reducir al mínimo los costes de existencias de materiales se consigue solamente si no existen impedimentos particulares. Los problemas del sistema MRP se vinculan sustancialmente a dificultades de recopilación y actualización continua de la información necesaria.
Podría pensarse que sería preferible gestionar con métodos tradicionales los stocks de componentes de bajo valor y amplio consumo (por ejemplo, no vale la pena calcular con precisión y actualizar continuamente la demanda de tornillos) o de componentes que presentan lead times de compra particularmente largos y probablemente variables.
Cuando se invierte en un almacén automático vertical dotado de WMS, se erradica por completo este problema.
Con un sistema de WMS conectado a un almacén automático vertical, todos los componentes codificados depositados en el almacén son rastreados y siempre es posible mantener bajo control el stock de los códigos y hacer pedidos de reabastecimiento sobre esta base de.
En la programación de la producción, que puede ser semanal, mensual, anual o de una periodicidad definida, se suele programar el sistema de gestión de la empresa (ERP) para lanzar las salidas. Del programa de gestión es posible deducir el estado exacto de las existencias solo si cada operación de extracción, depósito y uso ha sido correctamente mapeada y rastreada.
Si el material se deposita en un almacén automático, dotado de Warehouse Management System, es fácil comprender que cada movimiento de recogida, ya sea de extracción o depósito, se registra y codifica y automáticamente se envía al programa de gestión mediante protocolos de intercambio de datos.
Para quienes se ocupan de programar la producción será casi imposible confundir los pedidos de reabastecimiento o mandar a producción artículos con componentes faltantes, precisamente porque las existencias se actualizan en tiempo real.
Una vez programado el sistema de gestión, este lanza las extracciones únicamente en las cantidades necesarias y estas acciones se transforman en salidas para el almacén. Una vez efectuada la salida, el WMS comunica automáticamente al programa de gestión la cantidad actualizada, poniendo a disposición un inventario just in time.
El riesgo de error prácticamente desaparece y ya no hace falta un inventario físico o manual; la gestión en almacén de la técnica MRP es la práctica ideal para un proceso productivo en línea con los principios más modernos de la lean production.
40 KPI de almacén para monitorizar y medir las prestaciones
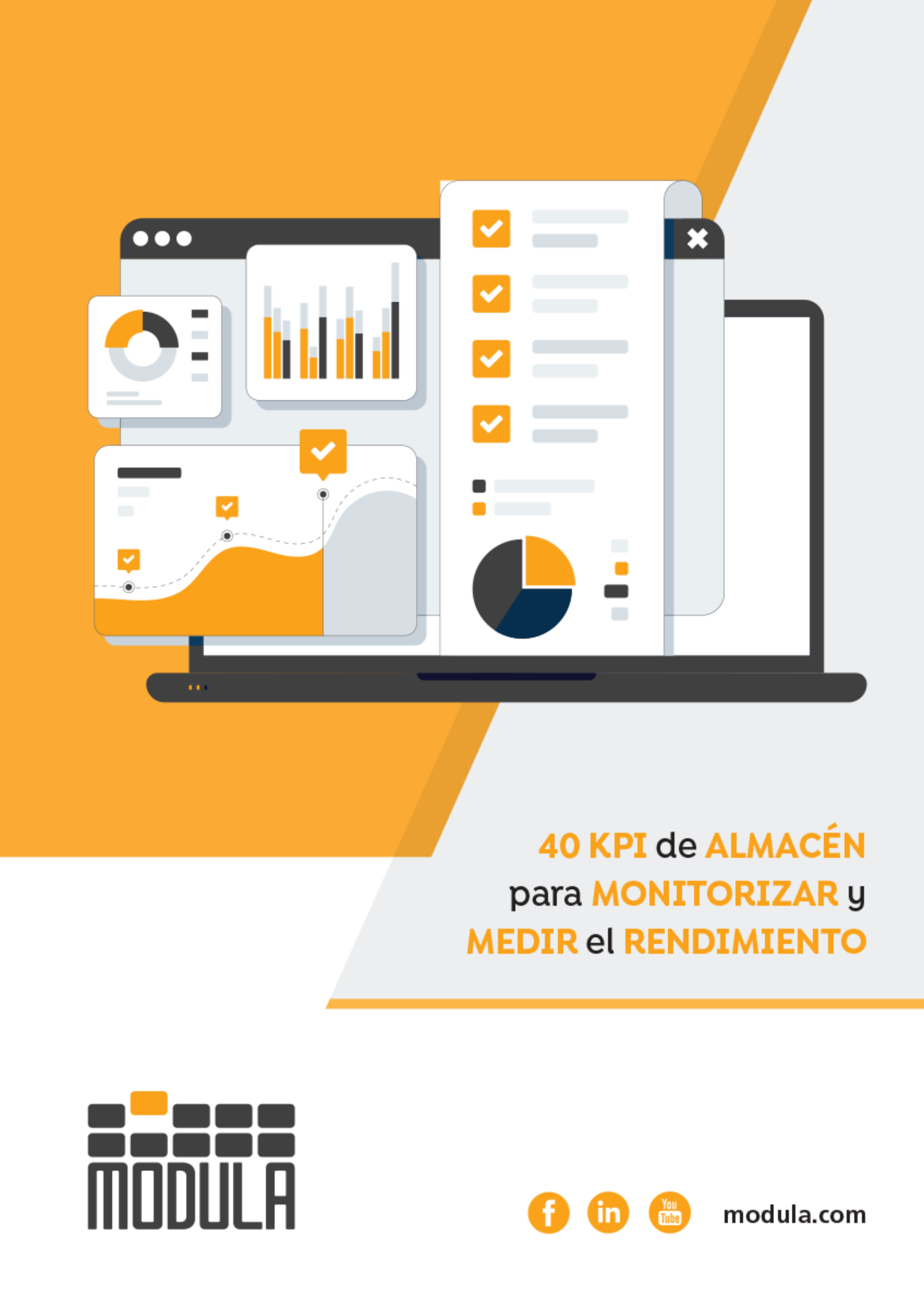