En las empresas manufactureras la gestión de las existencias y la programación de la producción deberían estar estrechamente vinculadas. De hecho, existen empresas en las que el dimensionamiento de las existencias de producto acabado constituye el input para la programación de la producción. En estos casos, las existencias de producto acabado pueden ser gestionadas con sistemas EOQ, tratando de reducir al mínimo los costes de gestión y teniendo en cuenta vínculos financieros, de espacio, etc. En otros casos, los vínculos en producción, sobre todo los lotes mínimos de producción, influyen considerablemente en la gestión de las existencias, es decir que la dimensión de las existencias de producto acabado es consecuencia de la programación de la producción. El ambiente productivo y la tecnología a disposición determinan si esta última actividad predomina sobre la primera o viceversa.
Recapitulemos brevemente de qué se ocupan las distintas áreas de gestión:
- La gestión de las existencias se ocupa del correcto dimensionamiento de las existencias de productos y materiales. Artículo de profundización sobre los modelos de gestión de las existencias: Cómo gestionar las reservas de manera eficiente.
- La gestión de las existencias de productos acabados en una empresa de producción se ocupa de dimensionar las existencias de producto acabado compatiblemente con los principales vínculos productivos.
- La programación de la producción se ocupa de definir los planes o los programas de producción y de establecer qué, cuánto y cuándo producir con diferentes niveles de detalle y diferentes horizontes temporales.
¿Qué significa elaborar planes de producción?
El objetivo fundamental de la programación de la producción es organizar la actividad de producción de manera que ésta resulte coherente con los planes de la empresa que establecen los objetivos económico-financieros de la empresa en su conjunto a mediano plazo (3-5 años).
Más precisamente, se trata de coordinar la actividad de producción con las logísticas de funcionamiento y los objetivos de eficiencia con la actividad de venta, que debe seguir la evolución del mercado y responder a la demanda de los clientes. Si bien por una parte la producción, para operar en régimen de máxima eficiencia (reduciendo al mínimo los costes de producción), requiere programas de producción lo más estables posible a lo largo del tiempo, por otra parte la ausencia de coordinación puede causar consecuencias graves: existencias superiores a las necesarias o existencias de producto insuficientes o baja eficiencia en el uso de los recursos de producción (y en consecuencia, mayores costes y deficiencias de servicio).
Planes de producción
En general, los planes de la empresa establecen los objetivos económico-financieros de la empresa en su conjunto a mediano plazo (3-5 años). Los planes o los programas de producción establecen qué, cuánto y cuándo producir con diferentes niveles de detalle y diferentes horizontes temporales.
Sustancialmente podemos distinguir 3 planes:
- El plan agregado de producción o Production Plan (PP): concierne a un horizonte temporal extendido (1 año) y tiene como objeto de planificación parámetros cuantitativos muy agregados (número de unidades producibles, toneladas de producto acabado, etc., a nivel total o por familias de producto). El objetivo del plan agregado es conciliar la demanda de capacidad productiva (que depende de la demanda de mercado) con la disponibilidad efectiva (expresada en horas-hombre o máquina).
- El plan principal de producción o Master Production Schedule (MPS): concierne a un horizonte temporal limitado (3-4 meses) y tiene como objeto cada uno de los productos acabados. En particular, el MPS tiene el objetivo de dimensionar todos los lotes productivos.
- El plan final de monitorización o Final Assembly Schedule (FAS): concierne a un horizonte temporal muy breve (1 mes) y tiene como objeto el ensamblaje-configuración del producto acabado. La tarea típica del plan final es la selección de los modos de elaboración de los pedidos.
La característica principal del proceso de planificación de la producción es su carácter cíclico, es decir que un mismo período puede ser objeto de varias planificaciones sucesivas con crecientes grados de definición. Podemos hablar de fases de planificación y control de la producción: cada fase se abre con la planificación de un período y se concluye con el control que abre la planificación del período siguiente.
Fase 1: preparación del plan agregado
Hablando del proceso de planificación de la producción hemos subrayado su carácter cíclico: un mismo período puede ser objeto de varias planificaciones sucesivas con crecientes grados de definición. El proceso consiste, pues, en distintas fases: cada fase se abre con la planificación de un período y se concluye con el control que abre la planificación del período siguiente.
Como datos de input podemos distinguir:
- Las previsiones de venta o los pedidos de los clientes.
- Las características del sistema productivo y las condiciones operativas estándar: turnos, horarios, lotes mínimos y múltiples, disponibilidad de mano de obra, restando las ausencias y las ineficiencias, etc.
- La disponibilidad (existencias en mano + productos pedidos – productos comprometidos) actual e ideal de productos acabados, semielaborados y materiales.
- Los estándares de consumo de los materiales (mediante las listas de productos).
- Los estándares de los recursos de producción (mediante los ciclos de elaboración).
Prácticamente el plan agregado de producción sirve para confrontar y conciliar la demanda con la disponibilidad de materiales y demás recursos de producción en un período de tiempo más bien extendido (en general, un año).
El detalle de los valores suele ser mensual y concierne a parámetros agregados (familias). Generalmente se revisa una vez al mes (o con menor frecuencia) mediante la técnica rolling (se cierra un mes y se añade un mes sucesivo).
En cuanto a los recursos productivos propiamente dichos (hombres y máquinas), es importante comprobar que la capacidad y la disponibilidad sean coherentes tanto durante el período evaluado (el año) como en los sub-períodos (meses).
En caso contrario, según el problema será necesario emprender las siguientes acciones:
- Ampliación o reducción permanente de la capacidad productiva interna.
- Recurso a elaboraciones externas.
- Ampliación o reducción de la capacidad productiva en determinados períodos mediante horas extra, horarios flexibles, vacaciones, etc.
- Anticipos de producción de períodos con demanda excesiva a períodos con disponibilidad excedente.
- En cuanto a la gestión de los materiales, es necesario definir acuerdos con los proveedores de larga data, con el propósito de reservar la capacidad productiva de los proveedores y negociar los precios y los modos de suministro.
La primera fase está concluida: el plan agregado está listo.
Fase 2: preparación del plan principal
El plan principal de producción o Master Production Schedule (MPS) concierne a un horizonte temporal limitado (3-4 meses) y tiene como objeto cada uno de los productos acabados y las relativas cantidades. El MPS es un instrumento de programación de la producción que sirve para dimensionar los lotes de producción, teniendo en cuenta los vínculos de capacidad productiva existentes en cada período.
En otras palabras, el MPS responde a las siguientes preguntas: ¿qué producir? ¿Cuándo realizar la producción? ¿Qué cantidad poner en producción?
Tratándose de un plan de producción derivado de la planificación agregada a largo plazo (con mayor nivel de detalle) el MPS debe tener un horizonte temporal más breve o igual que el horizonte temporal del Plan agregado y debe ser mayor o igual que el lead time de producción de los productos planificados. Generalmente la frecuencia de revisión de este plan es semanal o mensual.
Los datos que se ingresan en el MPS son:
- Pedidos y previsiones de venta de los productos.
- Niveles de existencias de productos.
- Existencias de seguridad para los distintos productos.
- Tiempos de producción de los distintos productos.
- Plan de producción agregado con vínculos de capacidad productiva.
Dado que, como hemos dicho, el MPS es un plan derivado del Plan Agregado, deberá respetar los vínculos ya establecidos anteriormente en términos de recursos máximos a disposición (cantidad de componentes o cantidad de horas).
Para su preparación, será necesario evaluar la capacidad productiva necesaria (capacity plan) en relación con las horas de mano de obra a disposición y en relación con la disponibilidad de la maquinaria a emplear. Si la capacidad disponible no satisface la demanda planificada, será necesario encontrar el equilibrio recurriendo, por ejemplo, a un aumento de los recursos (horas extra en lo posible) o anticipando/postergando las producciones.
En síntesis, generalmente un MPS se elabora con el siguiente procedimiento:
- Identificación del horizonte temporal de referencia.
- Elaboración de un borrador de MPS en base a las previsiones y a los pedidos ya recibidos.
- Ejecución de un análisis de capacidad, mediante simulaciones de viabilidad del plan de producción propuesto.
- Revisión del MPS en base al punto anterior o modificación de la capacidad disponible hasta hallar uno realizable.
Fase 3: preparación del plan final de montaje
El plan final de monitorización o Final Assembly Schedule (FAS) concierne a un horizonte temporal muy breve (de 1 a 4 semanas) y tiene como objeto el ensamblaje-configuración del producto acabado. En otras palabras, se trata del plan que define a nivel de turno de trabajo y centro de elaboración qué producir y en qué secuencia (se habla de artículos individuales, variantes de producto, paquetes, etc.) teniendo en cuenta la disponibilidad efectiva de materiales y horas-hombre o máquina.
La definición del FAS de un determinado período debe ser conforme a lo establecido por el MPS. De hecho, la cantidad global obtenible para un determinado conjunto (artículo) no deberá superar aquella prevista para los componentes comunes a nivel de MPS. En cambio, a nivel de variantes de producto, las combinaciones podrán variar si se han previsto existencias de seguridad para los componentes específicos de cada artículo.
El FAS es el instrumento de programación de la producción que tiene la función de:
- Controlar la disponibilidad de los materiales y componentes respetando lo programado.
- Garantizar el respeto de las fechas de entrega de los productos acabados según lo establecido.
- Mantener los niveles de existencias de materiales en almacén dentro de los mínimos niveles posibles.
- Regular las actividades de producción, compra y emisión de pedidos.
Las actividades planificadas anteriormente a nivel de MPS (compra de materias primas y componentes, elaboraciones internas de semielaborados, etc.) se predisponen siempre de acuerdo con las previsiones. Si el proceso de compra y el diseño de los productos se realizan bajo pedido, en ausencia de previsiones, todas las actividades se planifican directamente a nivel de FAS. En este caso, el FAS podrá abarcar horizontes temporales mayores y ser revisado con menor frecuencia (de manera análoga al MPS).
40 KPI de almacén para monitorizar y medir las prestaciones
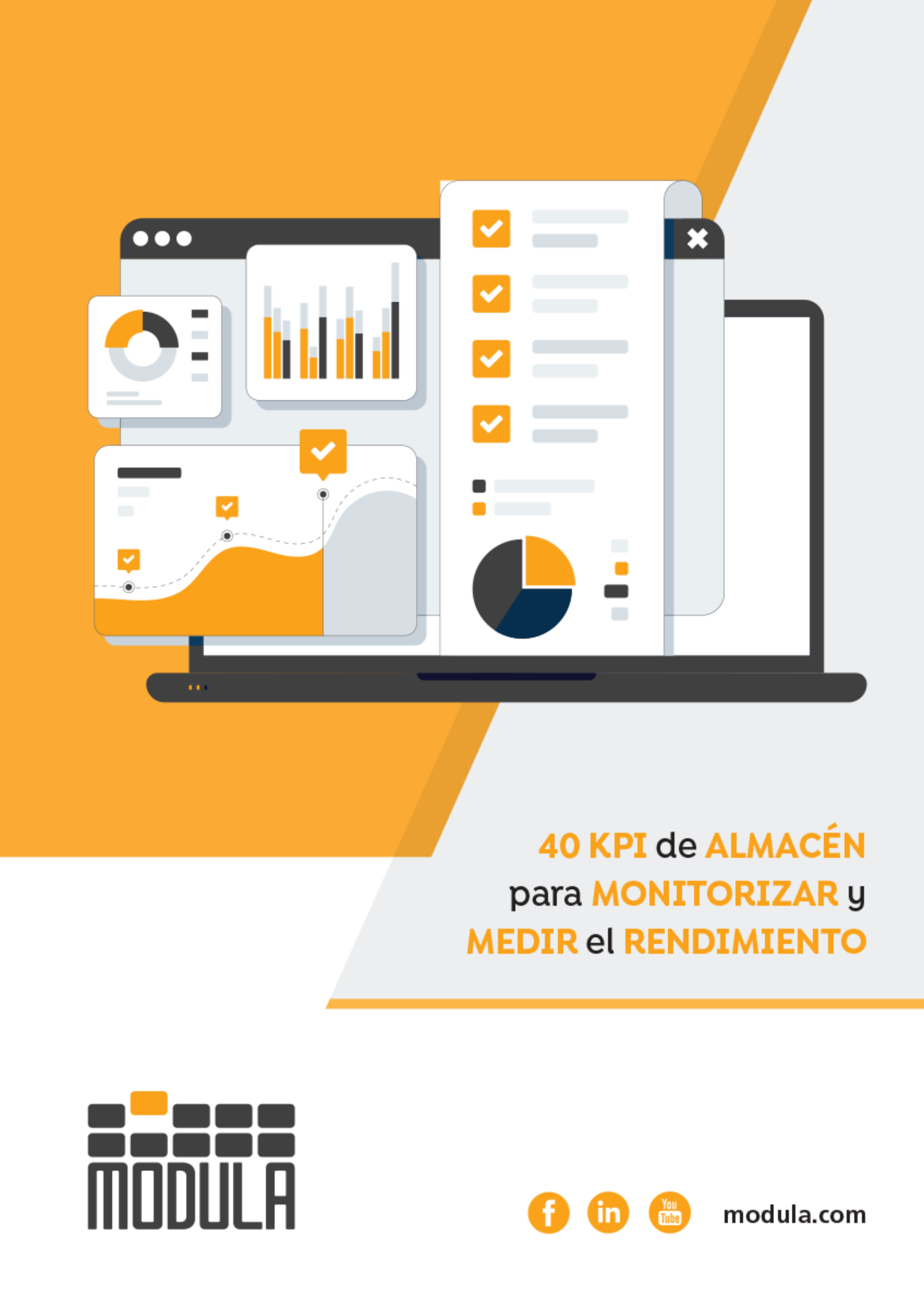