Ob es darum geht, Verschwendung durch die Beseitigung schwerfälliger Lagerprozesse zu beseitigen oder die Sicherheit der Lagermitarbeiter/innen zu gewährleisten, Lean Warehousing ist die Lösung für verschiedene Herausforderungen in der Lagerverwaltung.
Wir informieren Sie über alles, was Sie über Lean Warehousing wissen müssen, von den Vorteilen und Leitsätzen bis hin zu Erfolgsmodellen (Best Practice) und viel mehr.
Darüber hinaus stellen wir Ihnen unsere fortschrittlichen automatisierten Lagerlösungen und Bestandsverwaltungssysteme vor, die Sie bei der Umsetzung eines schlanken Konzepts für Ihr Lager unterstützen können.
Schaffen Sie ein Lager mit Lean Management Methoden („Lean Warehouse“) durch Automatisierung.
SCHAUEN SIE SICH DIE LÖSUNGEN VON MODULA AN!
Was ist Lean Warehousing?
Lean Warehousing ist ein Ansatz für die Lagerverwaltung, bei dem Lagerprozesse oder -aktivitäten, die Ressourcen verbrauchen, aber keinen Mehrwert schaffen, eliminiert werden, um Verschwendung zu reduzieren und die Produktivität zu verbessern.
Dieser Ansatz wurde ursprünglich in der verarbeitenden Industrie – im Automobilsektor – von Toyota entwickelt, wobei der Schwerpunkt auf Verschwendungsreduzieung und Effizienzsteigerung lag.
Als Beispiel soll ein manueller Kommissionierprozess betrachtet werden. Bei der manuellen Kommissionierung müssen Lagermitarbeiter/innen Kommissionierlisten verwenden und die Kommissionierplätze manuell bedienen, was als Verschwendung angesehen werden kann, da es Ressourcen wie Zeit und Arbeitskraft verbraucht, aber keinen Mehrwert für die Kundschaft bringt.
Um die durch die manuelle Kommissionierung verschwendeten Ressourcen zu reduzieren, könnte die Umsetzung des Lean-Warehousing-Ansatzes in dieser Situation bedeuten, dass stattdessen automatisierte Kommissionierlösungen genutzt werden.
Vorteile von Lean Warehousing
Lean Warehousing kann Unternehmen helfen, Verschwendung zu reduzieren, unnötige Prozesse zu eliminieren und die Produktivität und Effizienz ihrer Lagermitarbeiter/innen zu steigern.
Schlüsselvorteile von Lean Warehousing
- Produktivitätssteigerung. Lean Warehousing setzt den Schwerpunkt auf die Beseitigung von verschwenderischen Lagerprozessen, wie Überproduktion und übermäßige Lagerhaltung. Durch die Ermittlung und Beseitigung nicht wertschöpfender Tätigkeiten wird die Produktivität verbessert.
- Erhöhung der Arbeitssicherheit. Lean Warehousing stellt die Sicherheit am Arbeitsplatz in den Vordergrund, indem die Lagerautomatisierung genutzt wird, um die Notwendigkeit, an hohe und niedrige Stellen zu gelangen, zu beseitigen, wodurch sowohl Unordnung als auch unsichere Arbeitspraktiken reduziert werden.
- Verbesserung der Arbeitsmoral. Die Lean-Prinzipien fördern die Einbeziehung und Befähigung der Arbeitnehmer/innen. Indem die Mitarbeiter/innen in Initiativen zur kontinuierlichen Verbesserung einbezogen werden, kann man die Mitarbeiterbindung erhöhen und dem Personal das Gefühl geben, geschätzt zu werden und motiviert zu sein sowie zum Erfolg des Lagers beizutragen.
- Reduzierung der Ausfallzeiten. Durch die Verbesserung der Prozesse im Lager können Ausfallzeiten reduziert und ein reibungsloser Lagerbetrieb sichergestellt werden.
- Reduzierung des Bedarfs an mehr Lagerraum. Anstatt in eine größere Anlage umzuziehen, können Sie durch die Umsetzung des Lean-Ansatzes in Ihrem bestehenden Lager die Lagerbestände optimieren und Überbestände abbauen. Dies wiederum ermöglicht es Ihnen, die Kosten zu sparen, die mit einer Lagererweiterung oder der Anmietung zusätzlicher Lagerräume verbunden sind.
Unorganisiertes Lager vs. Lean-Warehousing-Ansatz, gekennzeichnet durch unübersichtliche Wege, organisierte Lagerbereiche und ein optimiertes Lagerlayout
Die 5S-Methode des Lean Warehousing
Die 5S-Methode ist ein grundlegender Bestandteil aller Lean-Methoden, einschließlich Lean Warehousing.
Die Leitsätze der 5S-Methode können dem Unternehmen helfen, ein effizientes, organisiertes und sicheres Arbeitsumfeld zu schaffen, wenn sie auf jeden Aspekt des Lagerbetriebs angewandt werden – vom Layout des Lagers bis hin zur Art und Weise, wie die Waren kommissioniert und verpackt werden.
Zu den Leitsätzen der 5S-Methode (und ihren japanischen Pendants) gehören:
1. Selektieren (Seiri)
Der Leitsatz „Selektieren“ besagt, dass jeder Artikel im Lager gründlich bewertet werden sollte, um sicherzustellen, dass er wertvoll ist. Veraltete, überflüssige oder selten verwendete Gegenstände sollten entfernt werden.
Um den Leitsatz „Selektieren“ umzusetzen, beseitigen Sie alles, was nicht regelmäßig benutzt wird, und entsorgen Sie unnötige Gegenstände in Ihrem Lager, wie z. B. ungenutzte Werkzeuge und Geräte.
Wenn Sie Waren mit geringer Umschlagshäufigkeit haben, die über einen längeren Zeitraum liegen geblieben sind, sollten Sie diese Artikel in einem separaten Lagerbereich aufbewahren, um Platz in Ihrem Lager zu schaffen. Dies erleichtert dem Lagerpersonal das Auffinden der benötigten Artikel und steigert die Effizienz.
2. Systematisieren (Seiton)
Der Leitsatz „Systematisieren“ besagt, dass Gegenstände je nach Häufigkeit ihrer Verwendung an bestimmten Orten aufbewahrt werden sollten, um sicherzustellen, dass sie bei Bedarf zugänglich sind.
Um den Leitsatz „Systematisieren“ umzusetzen, organisieren Sie Ihren Bestand, um sicherzustellen, dass er leicht zu finden und zugänglich ist.
Sie können zum Beispiel die ABC-Analyse-Methode einsetzen, um die Waren nach ihrem Wert und Umsatz zu kategorisieren.
Lagern Sie Ihre schnell umlaufenden Artikel (Kategorie A) in leicht zugänglichen Bereichen in der Nähe des Versandbereichs und Ihre langsam umlaufenden Artikel (Kategorie C) in weniger häufig zugänglichen Bereichen, z.B. in Zwischengeschossen oder in der hintersten Ecke des Lagers.
3. Säubern (Seiso)
Der Leitsatz „Säubern“ besagt, dass ein sauberes und gut instandgehaltenes Lager äußerst wichtig für die Förderung von Sicherheit und Effizienz ist.
Um den Leitsatz „Säubern“ umzusetzen:
- Schaffen Sie eine Routine für regelmäßige Reinigungs- und Organisationstätigkeiten. Erstellen Sie einen Zeitplan für das Fegen, Abstauben und Wischen von Böden, das Abwischen von Oberflächen und die Beseitigung von Schutt und Müll. Übertragen Sie die Aufgaben an bestimmte Lagermitarbeiter/innen oder beauftragen Sie professionelle Reinigungsdienste.
- Nutzen Sie Regale, Gestelle und Behälter. Achten Sie darauf, dass die Gegenstände geordnet und leicht zugänglich aufbewahrt werden. Implementieren Sie Etikettierungssysteme oder Barcode-Scanner, um die schnelle Identifizierung und Wiederauffindung von Waren zu erleichtern.
- Optimieren Sie Ihr Lagerlayout. Minimieren Sie Staus und ermöglichen Sie einen effizienten Warenverkehr. Stellen Sie sicher, dass die Wege frei von Unordnung sind und dass Geräte wie Gabelstapler oder Hubwagen über festgelegte Wege verfügen, um Unfälle zu vermeiden.
4. Standardisieren (Seiketsu)
Der Leitsatz „Standardisieren“ besagt, dass einheitliche Prozesse, Verfahren und Richtlinien eingeführt und befolgt werden sollten, um die Effizienz zu erhalten.
Um den Leitsatz „Standardisieren“ umzusetzen:
- Dokumentieren Sie die im Lager bestehenden Prozesse und Verfahren. Dazu gehören Arbeitsabläufe, Bestandsverwaltung, Auftragsabwicklung, Wareneingang, Kommissionierung, Verpackung und Versand. Achten Sie auf etwaige Abweichungen oder Ineffizienzen in diesen Prozessen.
- Analysieren Sie die dokumentierten Prozesse und ermitteln Sie Bereiche, in denen Erfolgsmodelle (Best Practices) eingeführt werden können. Dabei geht es darum, die effizientesten und effektivsten Methoden zur Ausführung von Aufgaben zu ermitteln, Verschwendung zu reduzieren und die Gesamtproduktivität zu verbessern. Führen Sie ein Benchmarking mit Industriestandards durch und holen Sie die Meinung der Mitarbeiter/innen ein, die direkt an diesen Prozessen beteiligt sind.
- Erstellen Sie klare und präzise Arbeitsanweisungen für jede Aufgabe oder jeden Prozess. Diese Anweisungen sollten die schrittweisen Verfahren, die erwarteten Ergebnisse, die Qualitätsstandards und die Sicherheitsvorkehrungen umreißen. Standardisierte Arbeitsanweisungen dienen als Bezugspunkt für die Mitarbeiter/innen, um ihre Aufgaben konsistent auszuführen.
- Bieten Sie Ihrem Lagerpersonal Schulungen an. Schulen Sie Ihre Mitarbeiter/innen an den neu erstellten standardisierten Arbeitsanweisungen. Stellen Sie sicher, dass die Mitarbeiter/innen die Verfahren verstehen, die Richtlinien befolgen und ihre Aufgaben gemäß der Norm ausführen.
- Nutzen Sie visuelle Anhaltspunkte. Verwenden Sie Schilder, Etiketten, Anzeigen mit Farbcodes oder Bodenmarkierungen, um die standardisierten Prozesse und Richtlinien visuell darzustellen. Diese visuellen Management-Tools helfen dem Personal, die richtigen Verfahren, Orte oder Materialien zu identifizieren, wodurch Fehler reduziert und die Einhaltung der Norm gefördert werden.
5. Selbstdisziplin üben (Shitsuke)
Der Leitsatz „Selbstdisziplin üben“ besagt, dass die ersten vier S (Sort, Set in Order, Shine und Standardize) konsequent eingehalten werden sollten, um eine Kultur der kontinuierlichen Verbesserung zu schaffen.
Um den Leitsatz „Selbstdisziplin üben“ umzusetzen:
- Durchführen Sie regelmäßige Audits. Ermitteln Sie verbesserungsbedürftige Bereiche und gewährleisten Sie die Einhaltung von Standards.
- Anbieten Sie fortlaufende Schulungen. Die Bedeutung der 5S-Praktiken immer wieder betonen und sicherstellen, dass Ihre Lagerarbeiter/innen wissen, wie man sie anwendet.
Verhalten sie sich anerkennend den Mitarbeiter/innen des Lagers gegenüber. Belohnen Sie Ihre Mitarbeiter/innen, die hohe Standards einhalten, um ihre Moral und Arbeitszufriedenheit zu steigern und andere Mitarbeiter/innen zu ermutigen, ihrem Beispiel zu folgen.
Die 5S-Methode des Lean Warehousing
Implementierung des Lean-Warehouse-Managements
Sobald Sie die Schritte zum Erreichen des Lean-Ansatzes festgelegt haben, besteht der nächste Schritt darin, die Erfolgsmethode (Best Practices) in Ihre täglichen Lagerabläufe zu implementieren.
Vollständige Integration des Lean-Warehousing-Ansatzes
1.Audit der Lagerprozesse
Die Überprüfung der Lagerprozesse ist der Schlüssel zur Ermittlung von Ineffizienzen und verbesserungswürdigen Bereichen im Lager.
- Definition der Ziele. Dazu können die Verbesserung der Effizienz, die Senkung der Kosten, die Einhaltung von Sicherheitsvorschriften, die Verbesserung des Kundendienstes oder die Ermittlung des Schulungsbedarfs gehören. Klare Ziele helfen Ihnen, sich auf die Prüfung zu konzentrieren.
- Erstellung einer Audit-Checkliste. Erstellen Sie eine Liste der zu untersuchenden Bereiche auf der Grundlage Ihrer Ziele. Dazu können Bestandsverwaltung, Kommissionierung, Verpackung und Versand, Wartung der Ausrüstung, Raumnutzung und Mitarbeiterschulung gehören.
- Datensammlung. Nutzen Sie verschiedene Methoden zur Sammlung von Informationen, z. B. physische Inspektionen, Mitarbeiterbefragungen, Überprüfung der Dokumentation (z. B. Versand- oder Sicherheitsprotokolle) und Datenanalyse (z. B. Auftragsabwicklungszeiten oder Fehlerquoten).
- Datenanalyse. Achten Sie auf Anzeichen, die auf ein Problem hinweisen. Wenn beispielsweise in einem bestimmten Zeitraum häufig bestimmte Artikel ausfallen, könnte dies ein Hinweis auf einen unzureichenden Bestand an schnell umlaufenden Artikeln sein.
- Messung der Leistung (Benchmark). Vergleichen Sie Ihre Leistung mit Branchenstandards und/oder mit Ihrer bisherigen Leistung, um Bereiche zu finden, die verbessert werden müssen.
- Empfehlungen. Empfehlen Sie Verbesserungen auf der Grundlage Ihrer Erkenntnisse. Dies kann Änderungen der Verfahren, der Ausrüstung, des Lagerlayouts oder der Mitarbeiterschulung umfassen.
- Präsentation der Ergebnisse. Bereiten Sie einen Bericht vor, in dem Sie Ihre Ergebnisse und Empfehlungen darlegen, und stellen Sie diesen den relevanten Interessengruppen vor.
2.Einführung des Just-in-Time (JIT)-Bestandsmanagements
Just-in-Time (JIT) ist eine Art der Bestandsverwaltung, bei der Sie eng mit den Lieferanten zusammenarbeiten müssen, um sicherzustellen, dass die Rohwaren zu dem Zeitpunkt eintreffen, zu dem die Produktion beginnen soll.
Durch die Einführung einer JIT-Bestandsverwaltung können Sie die Effizienz steigern, überschüssige Bestände beseitigen und die Lagerkosten senken – Ziele, die im Einklang mit der schlanken Produktion stehen.
Implementierung der JIT-Bestandsverwaltung im Lager
- Sammeln Sie historische Verkaufsdaten auf granularer Ebene (z. B. nach Verbraucherverhalten oder SKU), um einen detaillierten Überblick über die Nachfrage zu erhalten.
- Bauen Sie enge Beziehungen zu Ihren Lieferanten auf und beziehen Sie sie in Ihren Planungsprozess ein. Teilen Sie Ihre Bedarfsprognosen Ihren Lieferanten mit und stellen Sie sicher, dass diese Ihre Anforderungen in Bezug auf Menge, Qualität und Zeitplan erfüllen können.
- Implementieren Sie eine Bestandsverwaltungssoftware, die automatisch Bestellungen auslöst, wenn Ihre Waren einen niedrigen Lagerbestand erreichen, damit Sie keine Fehlbestände riskieren.
- Führen Sie in Ihrem Betrieb und bei Ihren Lieferanten strenge Qualitätskontrollmaßnahmen ein, um fehlerhafte Produkte zu vermeiden.
3.Schulung des Lagerpersonals
Die Implementierung von Lean Warehousing erfordert eine Änderung der Prozesse und eine Umstellung der Denkweise der Mitarbeiter/innen.
Die Schulung des Lagerpersonals ist der Schlüssel, um sicherzustellen, dass jeder die Leitsätze der schlanken Produktion versteht und weiß, wie sie in die Praxis umgesetzt werden können.
Schulung des Personals in Lean-Warehousing-Praktiken
- Bieten Sie Ihren neuen Mitarbeitern/innen ein fundiertes Orientierungsprogramm an. Das Programm könnte z. B. eine Einführung in die Leitsätze der schlanken Lagerhaltung sowie einen Überblick über die spezifischen Prozesse und Verfahren Ihres Unternehmens und eine klare Erläuterung der Aufgaben und Zuständigkeiten des Lagerpersonals umfassen.
- Bieten Sie spezielle Schulungen an, die sich mit den Leitsätzen und Praktiken des Lean Warehousing befassen, z.B. mit der 5S-Methode, der Wertstromanalyse, Techniken zur Reduzierung der Verschwendung, visuellem Management und Problemlösungsinstrumenten zur kontinuierlichen Verbesserung.
- Bieten Sie dem Personal praktische Schulungsmöglichkeiten zur Anwendung von Lean-Konzepten, z. B. Simulationen, Rollenspiele oder tatsächliche Arbeitsaufgaben.
4.Einsatz der Lagerautomatisierung
Die Automatisierung kann die Effizienz und Genauigkeit im Lager erheblich verbessern – Eigenschaften, die dem Lean-Ansatz entsprechen.
Zu den automatisierten Lagerlösungen gehören Regalbediengeräte (RBG), Kommissionierroboter und Lagerverwaltungssysteme (LVS), die die Genauigkeit und Geschwindigkeit der Kommissionierung erhöhen.
5.Kontinuierlicher Verbesserungsprozess (Kaizen)
Die Lean-Reise endet nicht, wenn die ersten Verbesserungen umgesetzt sind – es handelt sich um einen kontinuierlichen Prozess.
Sie können für kontinuierliche Verbesserungen sorgen, indem Sie regelmäßige Teamsitzungen abhalten, um Ideen zu diskutieren, oder formelle Kaizen-Veranstaltungen durchführen, bei denen Ihr Team gemeinsam an der Lösung eines bestimmten Problems arbeitet.
Implementierung des Lean-Warehouse-Managements
Schaffen Sie Lean Warehousing mit den automatisierten Lagerlösungen von Modula
Als führender Hersteller von automatischen Lager- und Lagerverwaltungssystemen bietet Modula fortschrittliche Lösungen, die die Produktivität, Effizienz und Kommissioniergenauigkeit steigern – primäre Ziele, die mit dem Lean-Warehousing-Ansatz übereinstimmen.
Die automatisierten Lösungen von Modula umfassen:
Automatische Vertikale Lager
Modula Automatische Vertikale Lager maximieren den vorhandenen Lagerraum durch Nutzung der verfügbaren Deckenhöhe und steigern so die Effizienz und Kapazität.
Zu den automatischen vertikalen Lagerlösungen von Modula gehören die folgenden Modelle:
- Modula Lift:. Perfekt für die Lagerung von Industrie- und Ersatzteilen; erhältlich in einer Vielzahl von Kapazitäten und Größen.
- Modula Slim: Dank seiner kompakten Bauweise ideal für Lager mit begrenztem Platzangebot.
- Modula OnePick: Hervorragend geeignet für Lager, die kein menschliches Eingreifen erfordern, da es vollautomatisch arbeitet.
Vorteile der automatischen vertikalen Lager von Modula
- Einsparung von bis zu 90 % der Bodenfläche, indem die verfügbare Deckenhöhe ausgenutzt wird.
- Beschleunigung der Auftragsabwicklung mit einem Durchsatz von 140 Träger pro Stunde
- Erhöhung der Kommissioniergeschwindigkeit auf über 300 Zeilen pro Stunde
- Erhöhte Sicherheit für die Mitarbeiter/innen, da sie nicht mehr in hohe und niedrige Bereiche gelangen müssen
- Sicherung des Bestands dank eines sicheren, geschlossenen Systems.
Horizontal-Karussell Modula HC
Das Horizontal-Karussell Modula HC ist die ideale automatische Lagerlösung für Einrichtungen mit begrenzter Deckenhöhe.
Vorteile des Horizontal-Karussels Modula HC
- Modifizierung der Regalabstände, um verschiedene Waren zu lagern
- Steigerung der Kommissionierleistung auf 550 Zeilen pro Stunde und Bediener
- Vollständige Transparenz von Lagerbeständen und Bestellungen
- Überwachung von Kommissioniervorgängen in Echtzeit
- Nahezu perfekte Kommissioniergenauigkeit, die mit unseren Put-to-Light-Systemen und Barcode-Lesegeräten bei 99 % liegt.
Kommissionierlösungen
Die Kommissionierlösungen von Modula reduzieren die erforderliche Suchzeit und erhöhen die Kommissioniergenauigkeit bei der Bearbeitung großer oder einzelner Aufträge.
Vorteile der Kommissionierlösungen von Modula
- Verbesserung der Kommissioniergenauigkeit und -geschwindigkeit mit Hilfe von Lichtgeräten, die das Lagerpersonal zum richtigen Ort führen
- Verbesserung der Bestandsverwaltung mit einem umfassenden Überblick über den aktuellen und prognostizierten Bestand
- Weitere Steigerung der Genauigkeit und Effizienz, wenn sie in Verbindung mit unseren fortschrittlichen automatisierten Lagerlösungen verwendet werden.
Warehouse Management System
Das Lagerverwaltungssystem (LVS) von Modula ermöglicht die Überwachung der Position und der Bewegungen der Waren und bietet Ihnen einen umfassenden Einblick in Ihre Lagerbestände.
Vorteile des Lagerverwaltungssystems
- Volle Bestandstransparenz
- Überwachung und Verfolgung von Lagerbeständen und Lagerbewegungen
- Erhöhte Genauigkeit, wenn es in Verbindung mit den automatischen vertikalen Lagern von Modula verwendet wird.
Die fortschrittlichen Lagerlösungen und das Lagerverwaltungssystem von Modula ermöglichen es Ihnen, einen schlanken Ansatz für Ihre Lagerabläufe zu implementieren, um den Lagerplatz zu optimieren, die Kommissioniergenauigkeit zu verbessern und die Produktivität und Effizienz des Personals zu steigern.
Optimierung der Logistik dank innovativer technologischer Lösungen
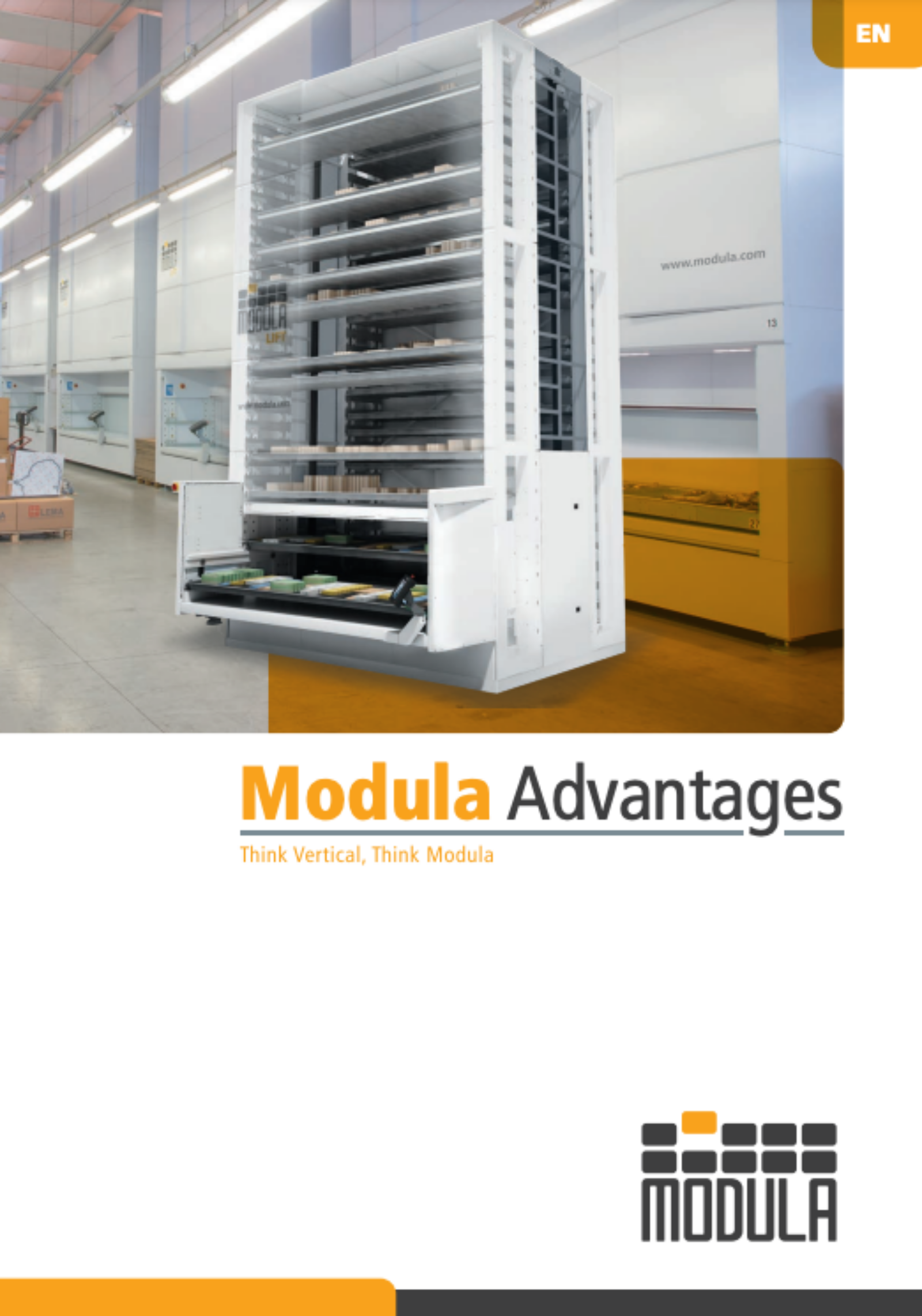