El sector del comercio electrónico, a pesar de un momento económico inestable, no deja de crecer en Italia, Europa y al otro lado del océano; las estimaciones suponen que este mercado, solo en Estados Unidos, rozará cifras cercanas a los 11 billones de dólares para el año 2025.
Sin embargo, pocos conocen las dinámicas que tienen lugar entre bastidores de este enorme flujo: la mayoría de los usuarios de servicios de comercio electrónico ni siquiera se preguntan cómo es posible sostener la logística de un almacén, manteniéndola siempre eficiente y de altas prestaciones.
Detrás de cada entrega, de cada paquete, de cada pedido, hay operadores y empresas que deben gestionar una cantidad cada vez mayor de existencias, realizar entregas rápidas y sin errores, todo ello sin aumentar la mano de obra ni el espacio ocupado por el almacén.
¿Existe un procedimiento ideal para optimizar estas operaciones? Por desgracia, no existe una solución que, con un chasquido de dedos, lo resuelva todo. De hecho, el almacén vive de procesos interrelacionados entre sí; para mejorar la gestión y aumentar así el número de envíos, o hacerlos más rápidos, es necesario que la empresa concentre su atención en los procesos de mayor impacto, los estratégicos.
Uno de ellos es el slotting del almacén: un método de organización del espacio de almacenamiento que puede contribuir a mejorar la eficiencia y la productividad en todos los sectores y en todas las empresas, especialmente en aquellas equipadas con sistemas de automatización, como los almacenes automáticos verticales.
¿Qué es el slotting de almacén y por qué introducirlo?
Uno de los procesos que más repercuten en la gestión operativa del almacenamiento es precisamente el slotting del almacén. Se trata de una secuencia logística que permite optimizar el espacio, ubicar los artículos y elegir materiales y accesorios para mejorar las prestaciones de picking.
Una gestión eficiente del espacio es fundamental en un almacén y, por regla general, se basa en la correcta colocación de las unidades de almacenamiento (SKU): cada una de ellas debe ocupar un slot óptimo para facilitar la operatividad de los encargados del almacén.
A su vez, cada slot se diferencia, según parámetros de la empresa, en slot fijo o aleatorio.
El slot fijo es un método de subdivisión del inventario que se utiliza para los productos que tienen una colocación permanente. El slot aleatorio suele utilizarse para los productos que se asignan a la primera zona de picking disponible.
Normalmente, el slot fijo se reserva a los artículos en rápido movimiento o de alta rotación, mientras que el slot aleatorio se utiliza para los artículos de baja rotación.
Slotting de almacén: ¿por qué implementarlo?
La elección de cómo organizar el almacén tiene siempre por objeto lograr el menor coste de gestión optimizando las ubicaciones de picking. Esto significa productos mejor colocados en el área de picking, menos desplazamientos y menos tiempo perdido. Significa mapear y analizar el historial y las actividades del almacén para saber qué productos hay que mantener cerca entre sí y en qué parte del almacén.
En todo almacén existe una «golden zone» con áreas o ubicaciones donde se conservan los artículos más demandados, es decir, con mayor rotación. Si la golden zone se compacta, las operaciones se optimizan inmediatamente.
La optimización de Slotting normalmente afecta el análisis de posicionamiento de acuerdo con la clasificación ABC de las unidades logísticas. Un buen análisis del slotting permite un gran ahorro en términos de gestión de almacén: si el tiempo de viaje y el tiempo de picking pueden modificarse a favor del tiempo de picking, la eficiencia será indudablemente mayor. Es crucial reducir en la mayor medida posible los costes de picking y de reposición.
3 buenas prácticas fundamentales para el slotting
Una vez conocidas estas dinámicas, veamos cómo se puede establecer un proceso de slotting eficiente.
1. Organizar el inventario en función de la velocidad de las SKU
Desde la repentina demanda de balones de playa y adornos festivos en verano, hasta las rebajas y los descuentos imperdibles del Black Friday, la estacionalidad puede tener un gran impacto en la velocidad de las SKU (la frecuencia de picking de cada artículo en un período determinado).
Para responder a los picos de demanda, es necesario idear y crear una estrategia de distribución de las existencias para mejorar la disposición de las mismas y mantener una buena eficiencia del almacén durante todo el año.
Consejos para organizar el inventario con el fin de satisfacer la demanda estacional:
- Determinar qué productos se ven o se verán afectados por la demanda estacional
- Identificar cuándo se producirán los picos
- Identificar los artículos que se mueven con rapidez y colocarlos cerca de la zona de envío para facilitar el picking
- Agregar las SKU que se retiran con frecuencia en la misma área de almacenamiento
2. Organizar el inventario de los slot en función de la zona o del equipamiento
Tanto si se trata de almacenar productos perecederos en zonas refrigeradas (en cuyo caso será necesario adoptar soluciones como el Modula Climate Control) como si se almacenan artículos de gran valor en compartimentos de alta seguridad, identificar la zona correcta para cada artículo es crucial para garantizar una gestión eficiente del inventario y la seguridad en el puesto de trabajo.
Cómo dividir el slotting del inventario en función de las zonas:
- Delinear las zonas de picking del almacén
- Identificar el área de almacenamiento adecuada para cada SKU: por ejemplo, colocar los artículos perecederos en áreas de ambiente controlado y guardar los líquidos inflamables en la zona dedicada a los inflamables.
Además de dividir el almacenamiento de los artículos/SKU por zonas, es posible optimizar el slotting del inventario agrupando los productos en función de los equipos de picking utilizados.
Cómo optimizar la distribución de las existencias en función de las herramientas y equipos de picking utilizados en el almacén:
- Almacenar los artículos pesados en carriles próximos entre sí
- Almacenar las piezas pequeñas en otra zona de picking, lejos del material pesado
- Si se utilizan carretillas elevadoras o plataformas de tijera para retirar las existencias, asegurarse de que los pasillos sean lo suficientemente anchos para el paso de estos equipos
3. Organizar las existencias en función del análisis de afinidad de los productos
El análisis de afinidad de los productos es el proceso de analizar el comportamiento de los consumidores para evaluar e identificar qué productos suelen comprarse juntos.
Ejemplos de kits o paquetes de artículos que pueden venderse juntos son los cartuchos de tinta y las impresoras, el papel de regalo y los adornos navideños, la pasta seca y los tomates en conserva, los teléfonos móviles y las carcasas.
Saber qué productos suelen comprarse juntos ayuda a optimizar la subdivisión de las existencias en el almacén, a estimular las promociones y a involucrar a los clientes en las actividades de cross-selling o up-selling de productos relevantes.
Para la subdivisión del inventario mediante el análisis de la afinidad de los productos:
- Estudiar el comportamiento de los consumidores y sus pautas de compra
- Almacenar los artículos de un paquete, o que potencialmente pueden venderse juntos, uno al lado del otro.
En estos casos, el operador tiene que realizar actividades multipedido y, en consecuencia, batch picking. El hecho de tener ya ordenado todo el almacén en función de los posibles multipedidos reduce enormemente los tiempos de picking porque no obliga al operador a recorrer el almacén a lo largo y a lo ancho.
Los almacenes verticales Modula son la mejor solución en estos casos, ya que el operador puede permanecer en su mismo puesto para realizar el batch picking, es decir, la retirada de los artículos del mismo tipo al mismo tiempo y clasificarlos después en los distintos pedidos.
¿Cómo puede ayudar la automatización a optimizar la organización del almacén?
Desde la reducción de los tiempos de viaje hasta el aumento de la seguridad en el puesto de trabajo, he aquí cuatro motivos por los que la subdivisión del almacén, combinada con la introducción de soportes automatizados, es clave para optimizar la gestión del inventario.
1- Reducción de los tiempos de desplazamiento
La rutina de un operador de almacén incluye la búsqueda de productos dentro del almacén mismo para su retirada, por lo que la posición de las existencias es crucial a fin de reducir el tiempo necesario para retirar los productos listos para su envío.
Es en casos como éste en los que el slotting de almacén resulta útil: la mercancía que se vende con rapidez puede almacenarse cerca del área de envío, lo que agiliza la retirada y el reabastecimiento.
Incorporar un almacén automático Modula es un claro ejemplo de aumento de la eficiencia: los tiempos de desplazamiento prácticamente se anulan, a favor de una «golden zone» concentrada en el almacén. Además, los costes de reabastecimiento resultan fácilmente previsibles, manteniendo bajo control todos los pickings, depósitos y empleo de material.
2- Aumento de la seguridad
Como en cualquier otro lugar de trabajo, por desgracia también en el almacén pueden producirse accidentes. Ya sea tropezar por descuido con un producto dejado en el suelo o ser golpeado por un artículo que cae de un estante, un almacén puede ser un fértil caldo de cultivo de accidentes si la mercancía no está almacenada correctamente.
Los almacenes automáticos Modula permiten, en primer lugar, guardar todos los productos en el interior de bandejas, evitando así el riesgo de caídas repentinas de los estantes, pero sobre todo permiten almacenar las mercancías más ligeras en la parte superior y los artículos más pesados en la parte inferior, garantizando así un área de almacenamiento equilibrada y más segura.
3- Mejorar la movimentación de los materiales
El valor estimado de todas las devoluciones globales en Europa en 2020 fue de 490.000 millones de euros. Este es el resultado de un estudio reciente, realizado por Twenga, en el que se compararon los porcentajes de pedidos y devoluciones de los países europeos, poniendo de relieve los diferentes enfoques de los compradores digitales con respecto a la devolución de mercancía.
Las cifras más altas en cuanto a devoluciones se registran en Alemania (53 %), seguida de Holanda (52 %), Francia (45 %), Italia (43 %), España (43 %), Gran Bretaña (40 %), Bélgica (38 %) y Polonia (32 %).
Con los almacenes verticales, las devoluciones debidas a los errores de picking se reducen exponencialmente; en efecto, el simple hecho de almacenar los artículos en su posición correcta (por ejemplo, contenedores refrigerados para los alimentos perecederos) reduce las tasas de restitución y, por tanto, mejora la satisfacción del cliente.
Una correcta división del espacio puede mejorar el proceso de movimentación de los materiales. En un almacén organizado, los empleados se dedican principalmente a las operaciones de picking, que son operaciones de valor añadido, y no se ven obligados a recorrer los pasillos en busca de productos, ya que gracias a los almacenes automáticos verticales conocen la posición exacta de los artículos. Como resultado, están más concentrados y cometen menos errores de picking, y los procesos de gestión de las existencias son más rápidos, sencillos y eficientes.
4- Maximizar el almacenamiento
El espacio para un almacén en Italia puede costar entre 50 y 60 euros por metro cuadrado (en Milán son 55 euros por m2/año, en Roma 56 euros por m2/año y en Florencia una media de 50 euros por m2/año).
Mucho más caras son las ciudades de Londres, París y las del norte de Europa, mientras que los costes más bajos se observan en Polonia, Europa del Este y España.
Al planificar y realizar una subdivisión eficiente del almacén, las empresas pueden ahorrar espacio muy valioso y concentrar las operaciones en un área más pequeña y más cercana al lugar donde se necesitan. Obviamente, esto contribuye a reducir los costes globales de gestión o a eliminar la necesidad de trasladarse a un almacén más grande.
La capacidad neta del almacén automático vertical en caso de volúmenes de slot crecientes es muy alta Además, el mapeado detallado de las bandejas y la subdivisión en compartimentos mediante divisores y separadores, permite una optimización del espacio que es imposible lograr con el uso de estantes, repisas, entrepisos y almacenes tradicionales.
Es posible pensar en términos de golden zone y slotting incluso en el detalle del almacén: imaginemos que en la parte central de una bandeja en un almacén automático (llamado también armario vertical) están los productos más pedidos y con mayor rotación, siempre al alcance del operador. La amplitud del arco del brazo y la profundidad de la bandeja pasan a ser variables de cálculo para la colocación de los productos.
El uso de cubetas, recipientes y divisores de metal para la creación de compartimentos múltiples detallados puede aumentar aún más la eficiencia del picking. Normalmente estos sistemas forman parte del SGA o pueden ser módulos adicionales al SGA en contextos de mecanización o en la preparación manual.
Automatización y estrategia de slot optimization
La organización del almacén requiere un proceso continuo de recogida de información sobre el comportamiento de los consumidores, de análisis de los datos y de modificaciones a la disposición del inventario cuando es necesario.
Utilizar una solución Modula, junto con una razonada slot optimization, constituye una excelente elección para garantizar que las dinámicas de almacén se desarrollen correctamente, aportando beneficios desde el punto de vista de la productividad y de la seguridad.
El usuario puede monitorizar los niveles de stock en tiempo real, acelerar los tiempos de ejecución de los pedidos tanto para las operaciones de picking como de abastecimiento y evitar el despacho accidental de productos equivocados, obsoletos, caducados o en espera.
Las ventajas de un sistema de almacenamiento vertical automático Modula
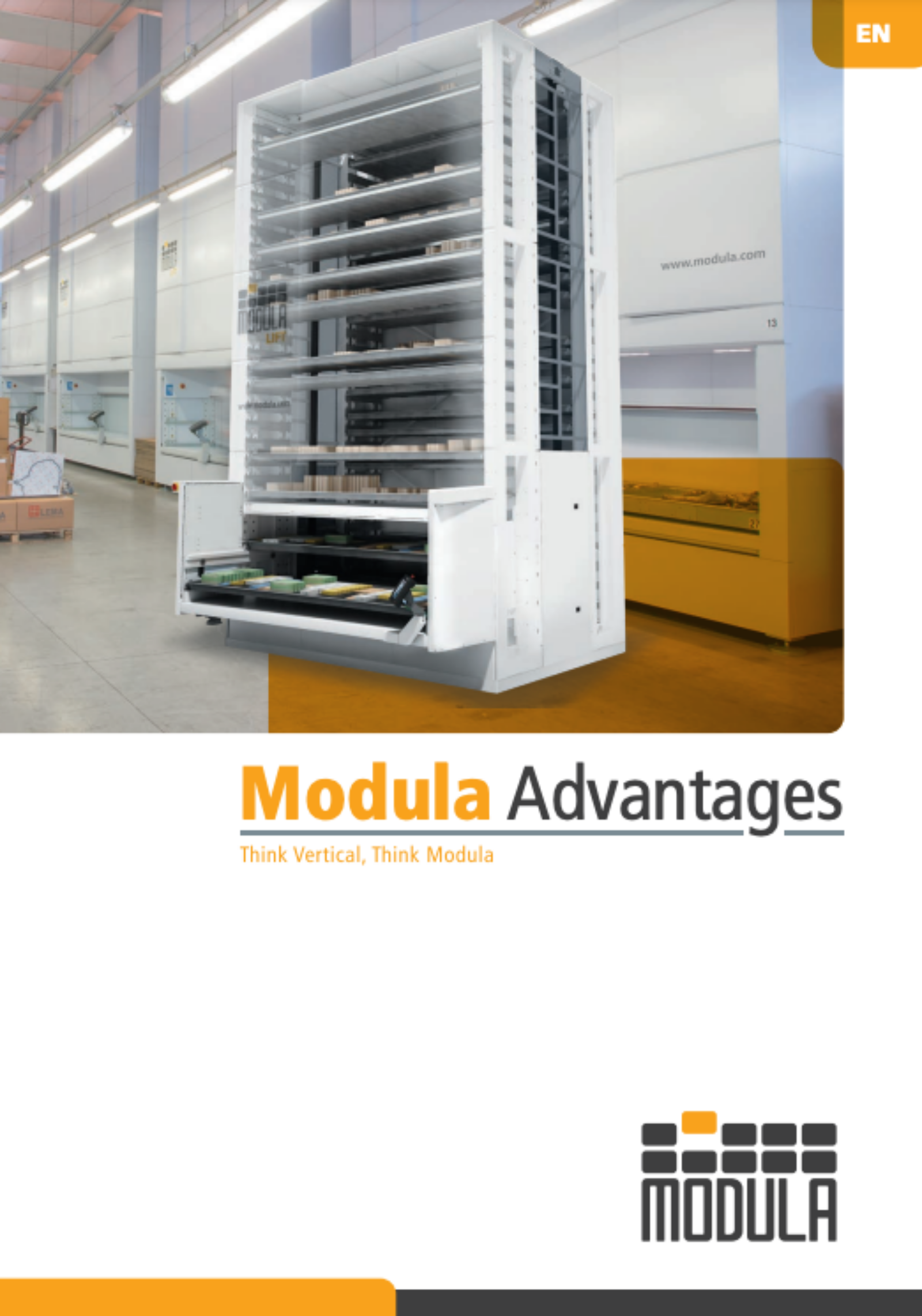