Bin storage is one of the most effective solutions for managing warehouse logistics, especially in industries where efficiency, speed, and precision are paramount. In the pharmaceutical sector, this method allows for the safe storage of sensitive products, while ensuring excellent traceability and expiry date control. In retail and e-commerce, it accelerates picking and order fulfilment, supporting increasingly dynamic omnichannel logistics. In the electronics industry, where the handling of delicate components requires protection and tidiness, bin storage provides optimal organisation and rapid access to stock.
Industries like the automotive, agriculture, manufacturing, and aerospace sectors, where kitting is essential for production, benefit from bins that facilitate the picking of individual components, ensuring both speed and efficiency. This approach allows products to be stored, organised, and retrieved intuitively, minimising waste and optimising operational flow, even in emergency situations.
Across all these sectors, the Modula Flexibox represents a highly innovative technology, combining all the advantages of vertical storage with high-speed picking. This system enhances overall warehouse operations without requiring changes to existing infrastructure or business processes, integrating seamlessly with numerous other technologies.
The Modula Flexibox: technical features and advantages
The Modula Flexibox is an automatic bin storage solution specifically designed to meet the needs of even the most dynamic industries, where high turnover requires rapid handling. Capable of managing up to 180 bins per hour, it significantly reduces the number of movements needed for each picking cycle.
The Modula Flexibox vertical bin storage system ensures exceptionally fast access times and high picking accuracy. Each bin arriving in the bay can hold up to 35 kg of material, ready for efficient retrieval.
This speed and precision are made possible by the core of the handling system, which consists of:
- A central elevator that moves vertically along the structure, carrying the bins from their storage positions to the operator bay.
- A telescopic fork that executes the picking process with extreme accuracy, reaching both the front and rear columns.
Another key advantage of the Modula Flexibox is its ability to handle up to 9 bins per picking cycle. Depending on the chosen model, the system can process 3 to 9 bins simultaneously, ensuring maximum flexibility to meet various operational needs. With the capacity to complete 180 picking actions per hour, the system enables far more order lines to be processed than in traditional warehouses, as numerous items can be retrieved from each bin. This approach streamlines the workflow and drastically reduces fulfilment times, enhancing overall warehouse efficiency.
This capability is particularly beneficial for batch picking, refining the picking process, and exponentially boosting productivity in warehouses and distribution centres. In particular, it reduces:
- The number of movements required for each operation.
- The waiting time between one picking and the next one.
- The risk of errors, thanks to the ability to organise multiple picking actions within a single operation.
Compact and intelligent design
The Modula Flexibox features an intelligent vertical layout, enabling the storage of hundreds of bins (600×400 mm) within a minimal footprint. Thanks to this configuration, warehouse space usage is reduced by up to 90%, with storage heights reaching up to 20 metres. Moreover, its compact and modular design ensures seamless adaptability to warehouses of any size. The Modula Flexibox can be installed in just a few days with a minimal investment, and, once operational, consumes less energy than a hair dryer, delivering efficiency in terms of both space and energy consumption.
The entire Flexibox storage system has been meticulously designed with a strong focus on minimising operating and maintenance costs. In fact, its strong yet simplified mechanics result in:
- Fewer technical interventions with respect to other automated storage systems.
- Reduced wear and tear on components, thanks to the use of high-quality, durable materials.
- Maximum reliability over time, significantly decreasing downtime.
There’s even an extensive customer care network available worldwide, staffed by a specialised and highly-trained team of continuously updated professionals.
Adaptability and scalability for unlimited growth
As previously mentioned, one of the Modula Flexibox system’s greatest strengths is its ability to adapt to the evolving needs of businesses. In fact, it is possible to start out with a single unit, which can be installed quickly, and later expand the system to meet any new requirements.
For both small warehouses and large logistics centres, the Flexibox system’s modular design allows additional units to be integrated without disrupting the existing infrastructure.
This scalability makes it a long-term strategic investment, ideally suited to support business expansion. Whether your company is a small logistics business or a large distribution centre, if it’s growing, the system can be seamlessly adapted to its new dynamics, without compromising on performance or requiring costly space reconfigurations.
Optimising picking with smart order preparation
The Modula Flexibox provides exceptional flexibility through customisable bay configurations and picking cycles, tailored to meet the specific workload volumes and operational needs. Its structure and advanced features also enable smart orders preparation, allowing boxes to be “pre-sorted” within the trays, even when the system is not in use.
The WMS processes the upcoming orders and pre-selects the required bins, arranging them systematically on the trays. These trays are then presented to the operators as soon as they are ready for picking.
This process allows orders to be prepared in advance, ensuring that all items are readily available for fast and accurate retrieval when needed.
Automation and interconnection with advanced technologies
Thanks to its ease of integration, the Modula Flexibox is also able to seamlessly connect with handling and automation systems, including:
- Autonomous mobile robots: The system integrates with conveyors and autonomous mobile robots to carry bins between different warehouse areas with no need for human intervention. This reduces waiting times, enhances operational speed, and is particularly beneficial in environments with restricted operator access.
- Robots: With compatibility for collaborative robots and automated picking systems, the Flexibox operates efficiently in highly automated environments, enabling anthropomorphic picking directly from the bin present in the bay.
- Put to Light Systems: Integration with put to light solutions provides visual guidance to operators during picking operations, reducing errors and increasing order preparation speed. Fixed or mobile stations, such as picking carts, can be used — sometimes in combination with a pocket monitor and wearable glove to facilitate live picking confirmation.
- IoT Technology and AI: The Modula Flexibox collects and transmits real-time operational data through Modula Web Analytics and OPC-UA telemetry. Moreover, with the support of artificial intelligence, this warehouse system enables businesses to optimise their processes through advanced data analysis.
To streamline the picking process and enhance efficiency, the Modula Flexibox supports Colour Guided Picking, where operators are guided by colour cues displayed on the screen during each picking operation. This functionality is enabled through the Pocket Monitor application, which provides clear and detailed visual guidance. During picking, the monitor displays the colour associated with the trolley in use and the item to be retrieved, indicating its precise position within the tray. The system automatically updates the WMS, thus reducing errors and improving operational speed. The Pocket Monitor, mounted on a mini PC or PC Stick and positioned directly on the trolley, also works in conjunction with a glove-like wearable barcode reader, allowing operators to confirm item locations hands-free. This intuitive and highly integrated system optimises picking and adapts to various logistical needs, enhancing both productivity and operational accuracy.
How to integrate the Flexibox with other Modula solutions
One of the Modula Flexibox system’s key strengths is its ability to integrate seamlessly into existing logistics infrastructures without disrupting warehouse organisation or rendering other storage systems obsolete.
The optimal scenario occurs when this solution is integrated into a Modula ecosystem: The Flexibox does not replace the other Modula solutions, but rather complements and enhances them, creating a more efficient and adaptable workflow.
A real-world example?
In an ideal workflow, goods stored on pallets can be processed at the input stage using the Modula Pallet. Once a large package or product has been depalletised, it can be stored within a tray in the Modula Lift warehouse, which is designed to handle bulkier materials with medium to low turnover.
For smaller, high-turnover items requiring rapid picking, the Flexibox is the perfect solution. In fact, this system is specifically designed to manage small and medium-sized items that require frequent handling, such as e-commerce and retail products.
The choice between a Modula Lift and a Flexibox system depends on various factors, including weight, size, and product turnover. The most suitable technology for the storage and picking requirements is determined based on these parameters.
That which we have just examined is only one of many possible configurations. But the integration possibilities with other Modula solutions aren’t limited to the Lift model alone. In fact, the Flexibox operates within the same ecosystem — and with the same software licences — as the Modula Slim, Pallet, Next, Climate Control, and Clean Room, offering unparalleled flexibility in stock management and picking.
An integrated digital ecosystem
All Modula solutions are connected via WMS software, creating a digital ecosystem in which every machine and system communicates seamlessly and can be coordinated and monitored. Every operation within the warehouse is managed and tracked by the software, ensuring a smooth workflow and precise accurate management.
Multiple machines can be made to operate within the same environment, optimising resources with no need to have separate licences for each individual system. This centralised approach enhances overall efficiency, reduces costs, and simplifies stock management.
Modula Flexibox | Modula Lift | Modula Pallet | |
Loading Units | 600×400 mm bins | Trays of various sizes (width and depth) | EuroPallets 1200×800 mm, pallets, boxes |
Material type | Small medium/high turnover items | Low and medium turnover materials of all types and sizes | Low and medium turnover material on pallets |
Picking Speed | up to 180 bins/hour | approx. 80 trays/hour | approx. 25 pallets/hour |
Optimised space | High | High | High |
WMS integration | Total | Total | Total |
AMR compatibility | Yes | Yes | Yes |
Why the Modula Flexibox system is the right choice for your warehouse
The Modula Flexibox system marks a significant advancement in automated logistics, delivering an optimal balance of speed, precision, and flexibility, while ensuring seamless compatibility with a wide range of technologies.
Its ability to integrate with other systems (particularly Modula solutions) without redundancy, and instead enhancing the relative storage and picking operations, makes the Flexibox an ideal choice for companies operating in various industries. With its versatile applications, the Flexibox is perfectly suited to a wide range of operational needs, boosting efficiency and driving business growth in every sector.
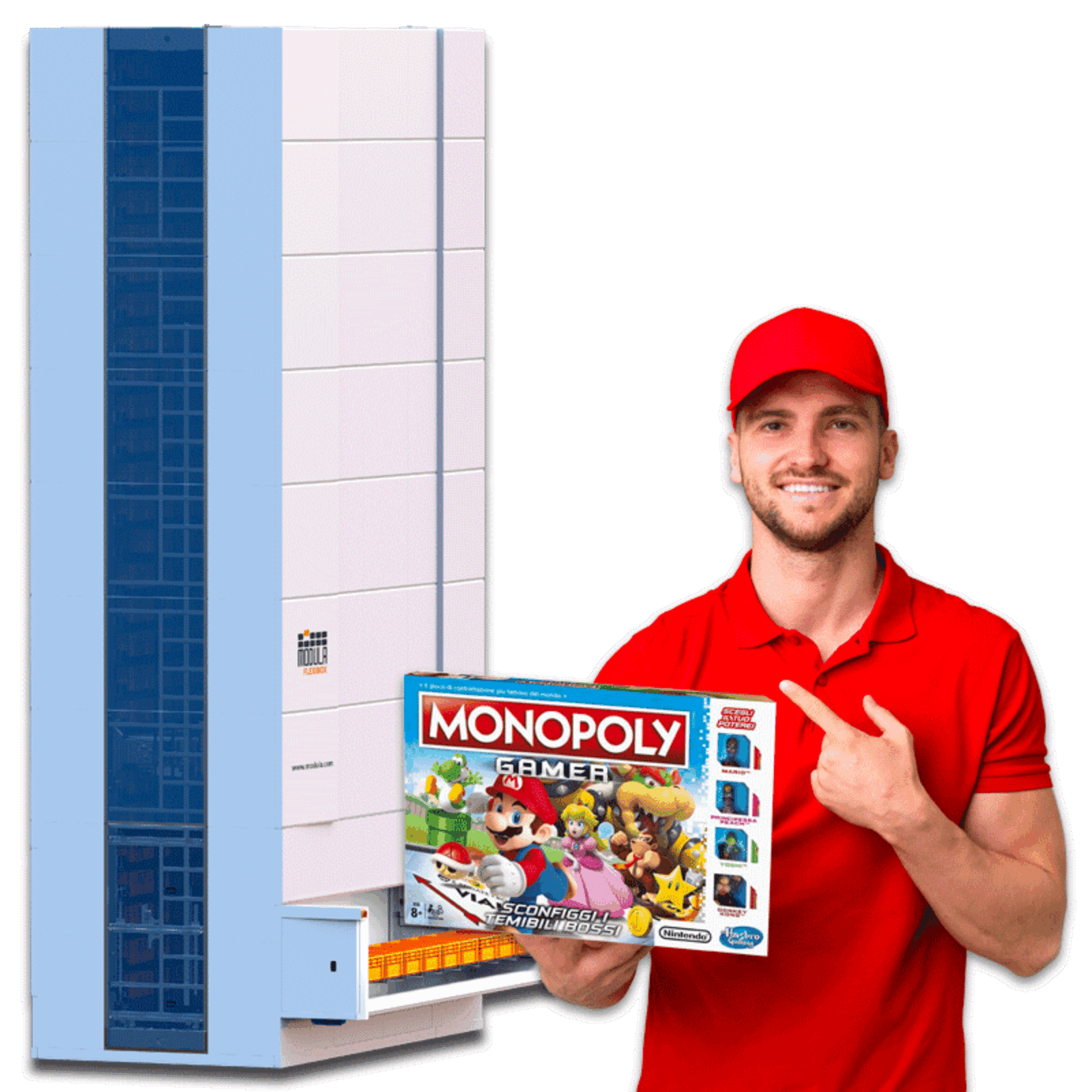
Transform your warehouse with the Flexibox
Discover all the benefits of smart logistics. Contact us for a personalised consultation, and optimise your warehouse with the latest Modula solution.