The organisation of a company’s warehouse is often the subject of discussion when talking about new investment. Whether it’s intended for the storage of raw materials, semi-finished or finished products, the warehouse greatly influences the total costs that a company can sustain and becomes an important lever in its competitivity. Although every business is an ecosystem in itself, some warehouse logistics issues are common to all companies: reduced delivery lead times, increased custom deliveries, poor ability to predict developments in the economic situation, shortages, and high cost of floor space. These are issues encountered by many companies, trading in sectors that are often very different.
Automation is the best solution for making the warehouse more efficient and bringing benefits to the entire production process. Depending on the type of investment you want to make, there are usually two options to choose from:
- Complete warehouse automation: this requires a thorough feasibility study, specialists to design the entire plant, and a very large budget.
- Using automatic solutions. In contrast with the previous solution, these can be incorporated into your processes without requiring a complete revolution in your logistics system. Amongst these are automatic vertical tray warehouses. If used to implement the right aspects of warehouse management (such as, for example, order flow, stocks and storage management), they can bring benefits in terms of efficiency and effectiveness at very limited cost.
There really is a lot of talk lately about automatic vertical warehouses. Flexible, modular and ergonomic design allows you to store and pick goods of different sizes quickly and easily. Let’s look at 6 benefits of using automatic vertical tray warehouses.
1. Save floor space
An automatic vertical tray warehouse allows storage of goods by utilising the height of your production plant and saving up to 90% of the floor space. Imagine if you didn’t have to store goods on standard shelves that take up all your space and make it difficult to store and pick goods. Instead you could deposit them all in a robust, vertical structure with a central elevator that moves the trays containing the goods, auto-adjusts its own unit height, and brings the goods right to the picking and loading bay. The floor footprint of all your goods is reduced to a minimum.
2. Save time
An automatic vertical tray warehouse guarantees maximum throughput of both storage and picking of goods as everything is just a click away. Using the Copilot Console, the time spent searching for your goods is reduced to a minimum. Just type in the product code and it is brought to the picking bay within seconds following the principle of “Goods to Man.” The operator is no longer obliged to move around the warehouse either during the search phase or doing the actual picking. Vertical warehouses fitted with two delivery bays are best at optimising your time management as they eliminate operator inactivity between one operation and the next almost completely: once picking from one tray is completed, the operator does not need to return to their post in order to proceed with the next operation. Within only a few seconds, a second tray is made immediately available in the second bay. With external bays, the changeover between the two trays is practically simultaneous. Depending on the configuration, these warehouses can even guarantee 140 cycles per hour, ensuring a time saving that has a direct and positive effect across your entire production.
3. Safety for operators and security for goods
All your goods are completely secure. Every operation is tracked and can be viewed by anyone to ensure maximum security against theft and damage. Access to individual trays can also be locked down and limited to certain user profiles. These warehouses also ensure operator safety. They will never again be forced to bend over, climb to dangerous heights, lift weights over long periods, or use stairs or mezzanines. All your goods are within easy reach right here in the delivery bay. If your warehouse is fitted with the external version of the delivery bay, it can also easily be combined with overhead hoists, mechanical or zero-weight cranes for lifting heavy items.
4. Reduction of errors
Have you ever had your goods sent back because the order was wrong? Probably yes, as it happens to most. Thanks to the automatic vertical warehouse you will avoid this risk. Using the software, you can track all incoming and outgoing goods, and by installing some accessories such as LED bars and laser pointers, you can reduce picking and loading errors so each order is prepared as perfectly as possible.
5. Real-time inventory
Inventory has never been so easy. At any time, you can compare your warehouse’s expected stock numbers against the physical stock numbers, check the stock and properly manage reorders with an efficiency improvement which will affect your entire production. All this thanks to the use of warehouse-linked WMS which indicates the quantity, type, and location of your stock at any time. This will limit problems to the point of complete elimination of the types of errors inherent to manual stock inventory management.
6. Take advantage of Ultra and Super Depreciation
By purchasing automatic vertical tray warehouses, you can claim Ultra Depreciation at 250% for the hardware and Super Depreciation at 140% for the software. The news is that you can now claim rebates even for the software, as long as it is associated with hardware related to Industria 4.0 projects, such as vertical warehouses. These are fully covered by equipment rules linked to business digitisation projects and for which you can claim depreciation at 250% as announced in the Italian State Budget 2017.
How to optimize picking operations?
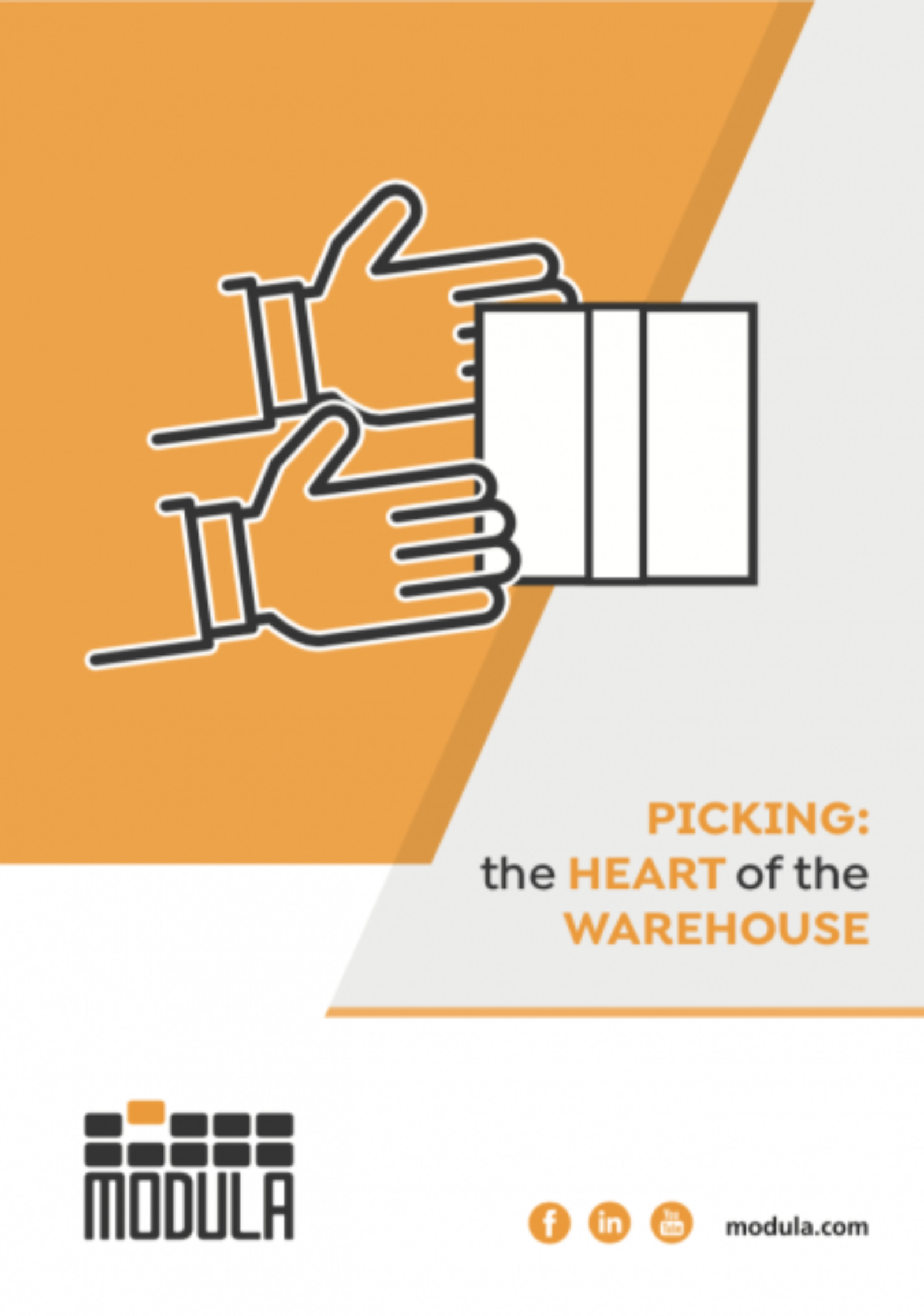