In the age of e-commerce, logistics can no longer just be efficient: they must guarantee throughput, precision and reliability to meet customers’ growing expectations. These days speed and accuracy are more than added value. They’re essential requirements.
An inefficient logistics system marred by delays, picking errors and inventory management problems has a compromising impact on the customer experience. Consumers are less and less willing to tolerate long waits or wrong deliveries, making it imperative to adopt advanced technologies to optimise the supply chain. Automation, digitisation and innovative strategies are and will be the key to ensuring competitiveness and service quality.
Order Fulfilment: how to improve order management for efficient logistics
In order to fully understand the dynamics – and the consequences of certain situations – it’s necessary to be aware of the entire process of order management and fulfilment.
Order fulfilment is the process that includes all activities necessary to receive, process and dispatch an order to the final customer. It’s a fundamental component of logistics and can have an impact on many aspects, including customer satisfaction.
This sequence of operations and activities can be outlined as follows:
Receipt of the order
- The order is received via one of the available channels (e-commerce website, ERP system, marketplace, etc.).
- The system checks the availability of the product in the warehouse.
- If the product is available, the order is processed.
Picking
- This is one of the most critical steps during which the items ordered are picked.
Efficiency in this phase is crucial, which is why it’s important to have:
- Picking methods such as batch picking, multi-order picking or single-order picking.
Advanced solutions such as vertical automatic warehouses and optimised picking solutions guarantee accuracy and speed.
Packaging and shipping
- The picked items are packed for shipment.
- The order is then handed over to the courier and a tracking number and shipping method are assigned.
- Shipment tracking provides up-to-date, real-time information.
After-sales and Reverse Logistics
- Management of returns and replacements to ensure a high level of customer satisfaction.
It’s clear that the whole process from the first to the last step needs to be as linear as possible. Not surprisingly, the picking phase plays a crucial role, determining the proper development of all subsequent phases.
Order fulfilment models
Depending on the size of the company and the type of product to be picked and managed, different fulfilment methods can be adopted, specific KPIs can be monitored to assess performance, and optimal picking solutions chosen to improve internal logistics.
The main Order Fulfilment models are as follows:
- In-house Fulfilment: internal management of the entire logistics process.
- Third-Party Logistics (3PL): outsourcing of logistics to specialised providers.
- Dropshipping: direct shipment from suppliers to end customers, without direct warehouse management.
KPIs to measure the effectiveness of Order Fulfilment
In order to optimise the order management and fulfilment process, it’s essential to monitor performance through targeted KPIs (Key Performance Indicators). Some of the most important include:
- Order Accuracy Rate: The percentage of orders processed without errors is essential to maintain high customer satisfaction and reduce returns.
- Order Cycle Time: The total time required to complete an order, from purchase to delivery. A short cycle indicates efficient fulfilment.
- On-Time Delivery: The percentage of orders delivered by the scheduled date. A key indicator for assessing the service’s reliability.
- Rate of Returns: The return rate gives an indication of any quality problems, inaccurate product descriptions or picking errors.
Fast, efficient picking: how Multi-order and Batch Picking optimise logistics
As mentioned above, the use of automated picking systems accelerates the picking and transfer of items, improving process continuity and reducing the risk of bottlenecks. These technologies, combined with innovative picking strategies and methods, help companies handle peaks in demand, ensuring fast and efficient order fulfilment.
Let’s take a closer look at two innovative and high-performance picking methods.
With multi-order picking the operator picks items for several orders at the same time.
Main characteristics:
- Each order has its own container or space during picking.
- The operator walks along the picking route and picks the items of each order one after the other.
- This solution is usually appropriate for small to medium order volumes, or items with little overlap (few items in common between orders).
Compared to traditional picking, the reduction of the distance travelled is a very positive development because it provides greater control over each order with less risk of misallocation of items, as well as being easier to implement. On the other hand, with many similar orders it might take longer to process them if they are handled separately.
Practical example:
The operator picks the items for three orders at the same time, carrying three different boxes (one for each order). At each stop in the warehouse they assign the correct item to the respective container.
Batch picking is the simultaneous collection of items from several separate orders in a single operation, without worrying about separating them immediately into individual orders.
Main characteristics:
- The operator picks items only once for all orders that require them, reducing the number of stops in the warehouse.
- After picking, the items are sorted and divided to complete individual orders (usually in a subsequent sorting phase).
- This solution is suitable for warehouses with a large number of orders that share identical items.
To further optimise batch picking and order fulfilment there’s an ideal technological solution, an innovative automatic warehouse designed and built for efficient box handling. This system not only drastically reduces picking times, but also increases order accuracy, ensuring unprecedented operational efficiency.
This method makes it possible to reduce picking times – especially for orders with many items in common – while also improving operator productivity and efficiency. This process is further refined if the operator is aided by highly automated systems or support technologies (e.g. autonomous mobile robots). On the other hand, this step necessitates an additional sorting step, leading to an increased risk of error if the process is not well organised.
Practical example:
The operator receives instructions to pick 30 pieces of a certain item because it’s needed for 10 different orders. Once picked, these pieces will then be sorted and assigned to their respective orders.
The main differences between multi-order and batch picking
Multi-order Picking | Batch Picking |
Items are picked for multiple orders but separately. | Items common to several orders are picked in a single operation. |
There is no need for a subsequent sorting phase. | The items must be sorted at the end. |
Suitable for orders with few items in common. | Ideal for orders with many identical items. |
Easier to manage manually. | More efficient with large volumes or automation. |
These methods are particularly effective for warehouses with high product turnover and high daily order volumes, such as:
- e-commerce: where the most popular products are picked in batches and then sorted into individual orders.
- Pharmaceutical distribution: pharmacies and hospitals receive supplies by batch picking, selecting multiple drugs in a single picking round.
- Garment logistics: orders containing similar items (e.g. the same model in different sizes) are picked at the same time to increase fulfilment throughput.
Furthermore, by employing advanced software such as a WMS in this process, the best picking and distribution strategies can be processed and updated automatically. For example, the Modula WMS analyses orders in real time and suggests the most efficient picking routes.
A real-world example? In online supermarket warehouses, orders with consumer products are grouped and handled automatically, reducing logistical steps and improving delivery times.
Advanced solutions to optimise picking and order management
Automation is key to increasing efficiency and flexibility, lowering operating costs and improving accuracy. In addition to vertical automated warehouses, the adoption of cobots and advanced picking solutions optimises the flow of operations and increases productivity
- Pick-to-Light: lights show operators which items to pick and in what quantity.
- Picking Cart: intelligent carts equipped with scanners and displays that guide the operator in multiple picking.
- AMR: autonomous robots transport the picked products to the sorting areas, reducing human travel.
- Miniload: automatic warehouse for light loads, with column structure and stacker crane moving along narrow aisles. It retrieves and transports loading units directly to the picking and shipping areas, ensuring productivity and safety thanks to the fully automatic picking system.
Therefore, investing in automated solutions not only optimises logistics, but also contributes to improved customer satisfaction through faster and more accurate deliveries.
Smarter and more responsive order management gives companies a competitive advantage and a greater ability to adapt to changes in demand, being able to count on a more agile and precise operation: an indispensable element for customer loyalty and gaining a lasting strategic advantage.
How to optimize picking operations?
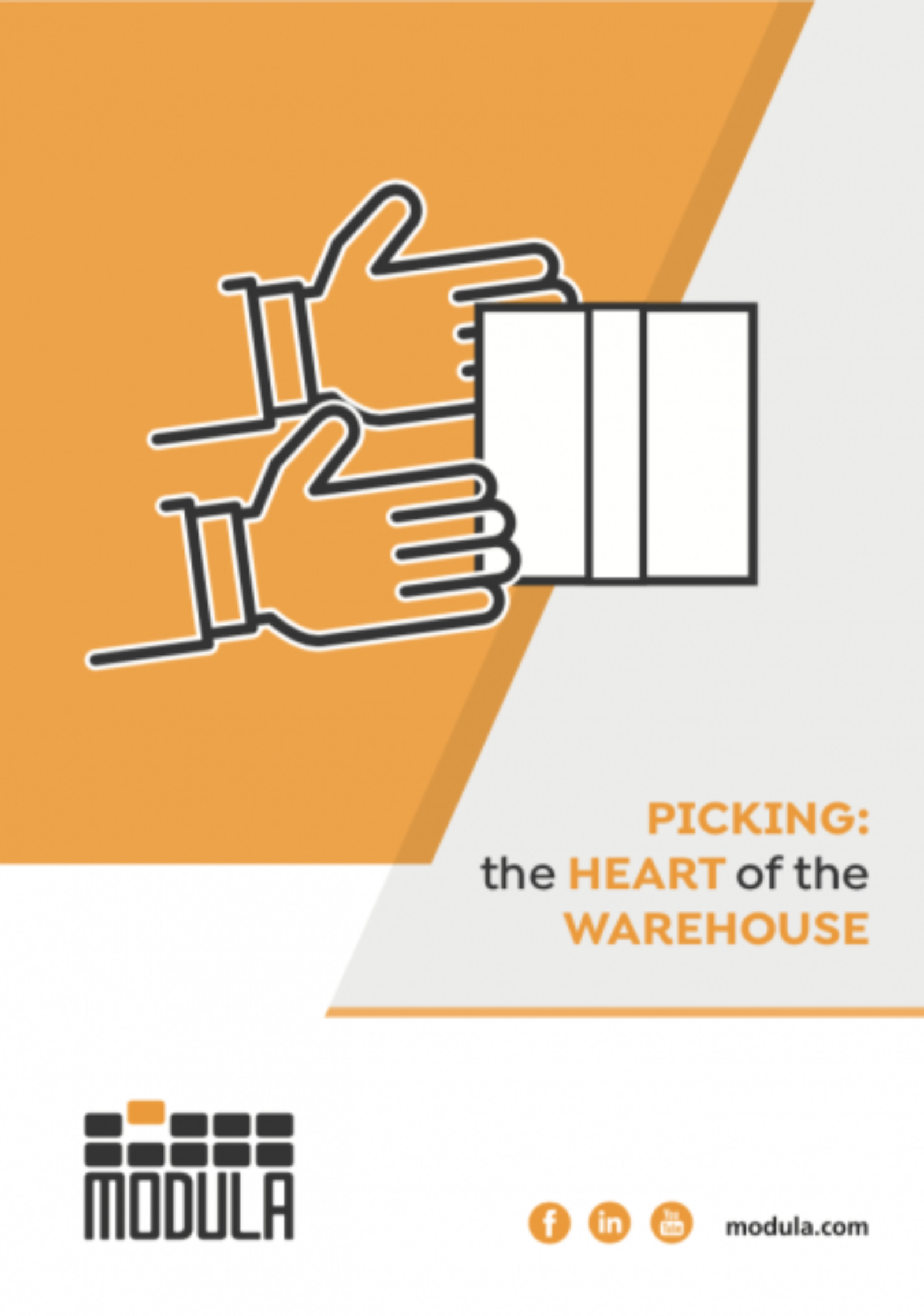