MRP (Material Requirement Planning) is a system for planning material requirements suitable for managing components needed to produce finished products. This technique is now widely used to plan production and procurement orders, taking into account market demand, bill of materials and production lead times.
If we imagine a stock manager who is using traditional models to manage “their materials” (Wilson and variants), we can imagine one of their main problems is how to estimate demand for these materials accurately. In fact, traditional models generally assume that future demand will be similar to past demand (mean historical demand).
This is all very well as long as demand is “regular”, but what happens when this is not the case?
What happens if demand is concentrated into certain periods (when the finished product is placed into production) but then drops off entirely? The error is a basic one: demand for these materials cannot be predicted but must be calculated on the basis of demand for the finished product. Production must be scheduled according to the quantity of finished products to be produced, and from this quantity you can arrive at the actual requirements for materials that go into them.
The MRP system has 3 inputs:
Master Production Schedule (MPS)
The production schedule (MPS) contains the quantity of each item to be produced within a particular time period. The time period referred to in the production schedule is generally short. In order to define the quantity to produce, you need to consider predicted demand for a given product, orders in hand already received and all constraints linked to the production system. You also need to try to define the quantities you can produce on a reasonably regular basis.
Bill of Materials
The Bill of Materials is the document which defines the structure of a product, i.e. types and quantities of components (raw materials, components, intermediate products, sub-assemblies, auxiliary materials) that make up a finished product. A product’s bill of materials has several levels (the finished product is generally “level zero”, its components “level 1”, its components’ components “level 2”, etc.). The bill of materials helps you progress from production schedules for finished products to those for their components. The operation through which an assembled product is transformed into a list of its components is called “explosion”.
Current stock level
The current stock level is the constantly updated record of what materials and components are currently lying in stock in the warehouse.
But how does an MRP system work? Calculations, all these calculations!
We can summarise how an MRP system works by defining the calculations needed to be performed. These are assembled here into 5 steps:
Calculating gross requirements
Gross first-level component requirements are calculated using orders to be issued (or launched) for finished products that they contain. This calculation is cascaded down through to the end of the bill of materials: from the first-level component orders to be issued we obtain the gross requirements for second-level components, and so on.
Calculating net requirements
You now need to calculate net requirements for each finished product, component, assembly and sub-assembly, taking into account how many of each of these you already have in stock. The net requirement is therefore obtained by subtracting stock in hand at the end of the previous period from the gross requirement. Gross and net requirements must be accurately linked to a point in time: the date on which the finished products have to be available comes from the production plan, whilst the dates for components must be calculated backwards taking into account production or procurement lead times.
Calculating incoming orders
Outgoing orders are the quantities to be ordered (or produced) for each finished product, component, assembly and sub-assembly. These quantities match those in the incoming orders but are expected during the lead time period.
Calculating outgoing orders
Outgoing orders are the quantities to be ordered (or produced) for each finished product, component, assembly and sub-assembly. These quantities match those in the incoming orders but are expected during the lead time period.
Calculating stock in hand at period end
The last step is to determine stock in hand at period end. This is obtained by adding incoming orders to stock available at period start and subtracting net requirements in the current period. This calculation must obviously be repeated for each product.
Advantages and limitations of the MRP system
The MRP system is preferable to order point and fixed interval systems when managing materials intended for production, especially if the final product is complex (with a multi-level bill of materials).
For these products, we can note the following advantages compared to traditional systems:
- Lower stock levels.
- Accurate predictions are not required (and not necessarily based on historical data) as it is forward-looking and is therefore better at managing even those items with highly variable demand.
- This is a real scheduling tool as it is able to highlight late orders and flag whether these are going to affect the production plan schedule.
As for any limitations, however, we must say that as the main goal of an MRP system is to reduce the cost of holding stocks of materials to a minimum, this is only possible if there are no particular obstacles. Problems with the MRP system are mainly linked to the difficulties businesses have collecting the necessary information and keeping it constantly up-to-date.
This would make you think that it might be preferable to use traditional methods to manage stocks of low-value components or those used in high volumes (e.g. no need to calculate requirements for “screws” accurately and constantly monitor them) or those with a particularly long and therefore most probably variable lead time.
In reality, if you decide to adopt an automatic vertical warehouse with WMS, all of these problems are completely bypassed.
With a WMS system connected to an automatic vertical warehouse, all coded components placed into the warehouse are tracked, so you will always have control over stock levels and can issue reorders based on these.
When scheduling production, which might be weekly, monthly, annually or another defined period, you usually consult your company ERP system in order to start picking operations. The ERP system will only give you the exact state of stock levels if every picking, refilling and usage operation has been correctly mapped and tracked.
When materials are placed into an automatic warehouse equipped with a Warehouse Management System, you can easily understand how each picking or refilling operation is recorded and stored and automatically sent through to the ERP system via data interchange protocols.
For anyone carrying out production scheduling, it will be almost impossible to make a mistake in reordering or send anything into production with missing components as all stock levels are actually updated in real time.
Once the ERP has been consulted, it launches picking operations for the necessary quantities and these are converted into picking orders in the warehouse. Once picking is complete, WMS automatically informs ERP of the updated quantity, making a just-in-time inventory a practical reality.
The risk of error practically disappears and there is no more need for physical and/or manual inventories. The MRP warehouse management technique is therefore ideally suited to a production process which uses the latest lean manufacturing principles.
40 Warehouse KPIs to monitor and measure performance
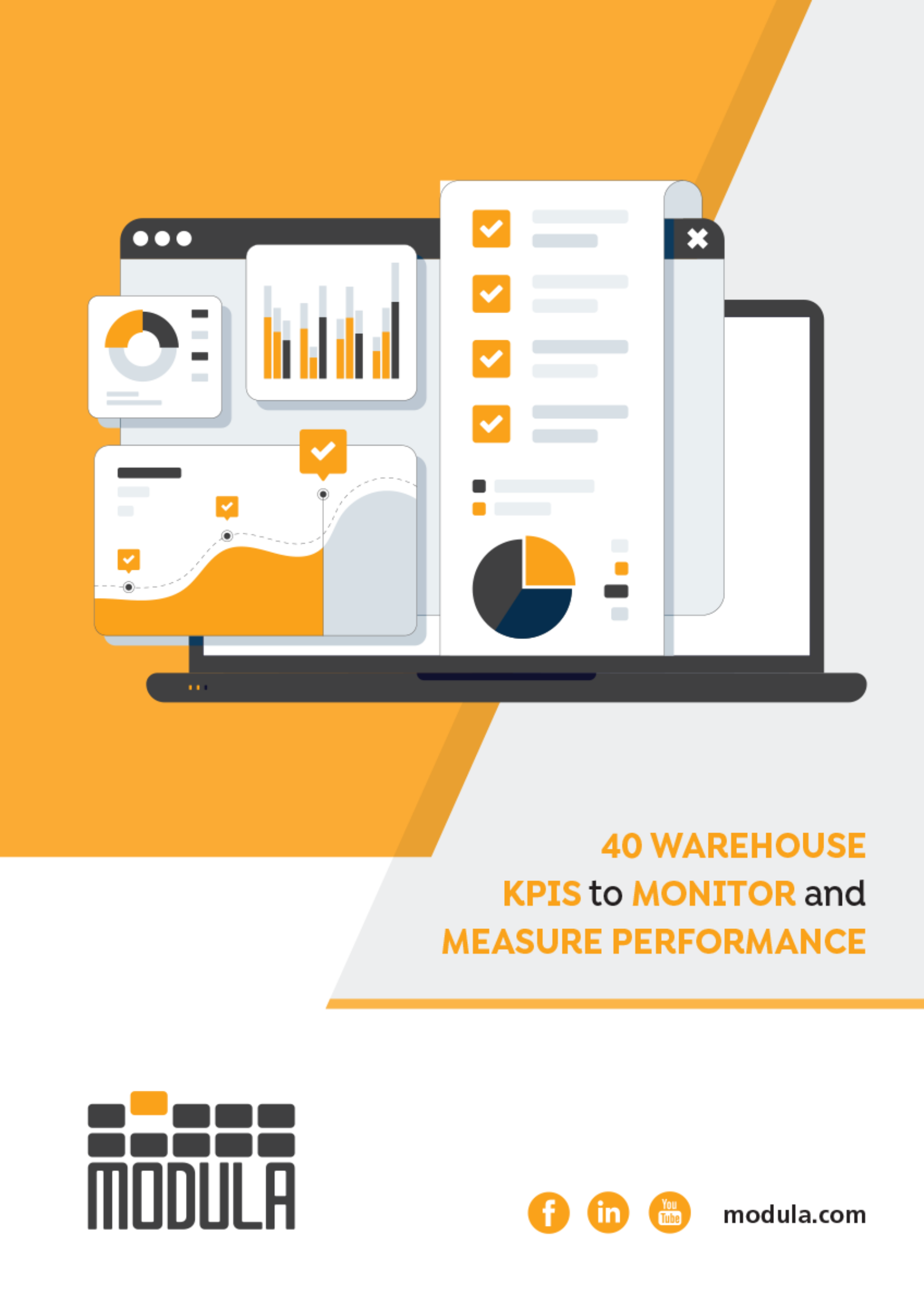