The term picking refers to the activities involved in retrieving items from your warehouse and in particular transforming a storage unit into a despatch unit.
Picking is a cornerstone of the logistic management of your warehouse and can affect both your company’s efficiency and customer service. It is pivotal to your competitivity and should not be undervalued.
It also represents a cost in terms of the significant resources it requires. This can occupy up to 50% or more of your human resources and also has related costs for safety and ergonomics. For this you will then need to optimise all of your picking operations and other related activities such as packaging and preparation for despatch.
Types of picking
First of all, it’s useful to specify that the various types of picking can be grouped into two main macro categories:
- manual picking
- automatic picking
These methods differ in the types of actions your operators are required to perform. In the first method, the trays or individual articles are transported and deposited by warehouse staff, and they must therefore comply with weight limits stipulated in the manual handling regulations.
In the automatic method however, physical picking operations are carried out by the machine and the operator has only to retrieve the articles which have been moved around mechanically.
Picking criteria
To categorise picking methods, a second criterion can also be used:
“man to goods”
“goods to man”
Whilst the first criterion involves picking operations where the operator is expected to move about, covering sometimes large distances within the warehouse and wasting significant amounts of time doing so, the second is more innovative and modern. It allows you to optimise your logistics management and combine it with warehouse automation techniques.
Optimise picking using automatic vertical warehouses
Amongst the most recent solutions for optimising your warehouse’s logistics management are automatic vertical warehouses with movable trays. They allow you to combine automation with “goods to man” picking systems.
Besides the advantages in terms of space, as they allow you to store products using the full height of your warehouse, automatic vertical warehouses allow you to reduce picking times as the operator is not required to cover large distances inside your warehouse and this speeds up picking operations immensely.
The structure of these warehouses is organised vertically, made up of internal trays whose number can vary according to your needs, and arranged in two columns. Between these is a motorised elevator which transports the trays from their “resting” position down to the delivery level. This is the area of the warehouse accessible to operators who are carrying out picking activities or loading goods into the trays.
Let’s look at why automatic vertical tray warehouses allow you to improve picking:
Picking throughput
With automatic tray warehouses, the time it takes to pick an item is reduced drastically. This is because the various goods are immediately accessible and made available in one single picking area. The operator does not have to move around the warehouse to pick them, instead it’s the tray which arrives in the delivery level following the principle of “goods to man”.
You can store goods of very different sizes and weights in your warehouse, and using the Dynamic Tray Height Storage system, the warehouse is able to manage the clearance between trays completely autonomously. This saves as much space as possible and allows you keep everything in one central location. When goods were stored on classic shelving units, these had to be managed manually and availability was affected by their limitations in terms of weight. This was vastly inferior to these new technologies.
The picking bay can be located at different heights, on several levels or even on opposite sides and can be equipped with overhead hoists and mechanical or zero-weight cranes for lifting heavy items.
Zero mistakes
Optimising picking times also means eliminating mistakes made by operators during picking of goods and preparation of orders. Using the Vertical Lift Module (VLM) you can do this because picking activities are guided by the program linked to the warehouse. In other words, using the graphical interface located on the side of the delivery level, you select the item to be picked. When the tray reaches the delivery level, a graphical representation of it appears on the screen showing specific instructions on which compartment you need to access to pick that item. All of this is automatically recorded in the database. You can add accessories to your warehouse to further simplify these operations, such as an LED bar and a laser pointer.
The LED bar can be used to indicate the quantity, code and description of the items to be picked and their location. On the other hand, the laser pointer uses a two-coordinate X and Y system to indicate the precise compartment from which to pick the item using a pointer and an intersection along a holographic line.
Double bay - Let's take a look
Choose vertical tray warehouses with a double loading and unloading bay. With this you have the option of two delivery levels for picking, one above the other.
From the same access point you can pick from one tray on the first level whilst the second tray is being transported automatically to the access point. The second tray is then immediately ready for picking as soon as you are finished with the first one. In this way, the operator does not have to wait.
A warehouse of this type, with a double delivery level, allows you to optimise picking and reduce waiting times between picks to zero.
As you can see, together with other cataloguing and storage operations, picking plays a strategic role in the management of your warehouse.
How to optimize picking operations?
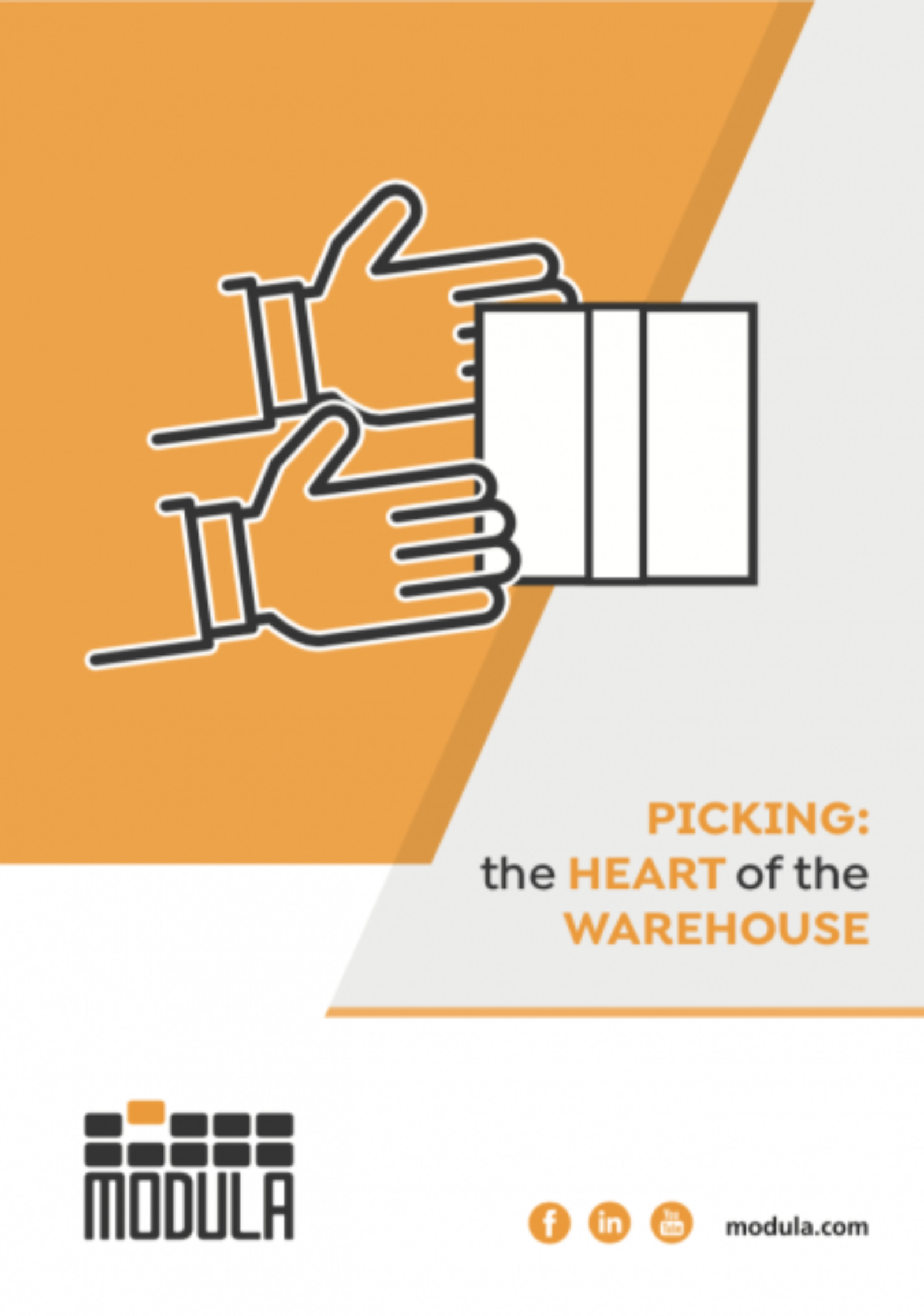