In manufacturing firms, stock management and production planning should be closely linked. In fact, in some businesses, finished product stock levels are the input for production planning. In these cases, finished product stocks can be controlled using EOQ systems, attempting to minimise operating costs and bearing in mind financial, space, etc. constraints. In other cases production constraints, especially minimum production batches, are a major factor in stock management, and therefore finished product stock sizes are consequent on production planning. The production context and the technology available will determine which of these activities prevails over the other.
Let’s refresh our memories about what the various management areas do:
- Stock management makes sure that stocks of products and materials are at the correct levels. Article discussing stock management models in depth: How to manage stock effectively.
- In a manufacturing company, finished product stock management decides the size of finished product stocks, bearing in mind the main production constraints.
- Production planning draws up production plans or programmes, which means deciding what to produce, in what quantities and when, with different levels of detail and different time horizons.
What does drawing up production plans mean?
The fundamental purpose of production planning is to organise production activities so that they are consistent with the company’s business plans, which define the medium-term (3-5 year) economic and financial targets for the whole company.
More precisely, this means coordinating production, with its own operating logics and efficiency targets, with sales, which has the aim of responding to market trends and satisfying customers’ requirements. While on the one hand, producing at top efficiency (minimising production costs) requires production plans which are as stable as possible over time, on the other hand, the lack of coordination may have serious consequences: surplus stocks and/or a lack of product in stock when required, or low efficiency in the use of production resources (which means high costs and poor service).
Production plans
In general, company business plans set the medium-term (3-5 year) economic and financial targets for the whole company. Production plans or programme define what to produce, in what quantities and when, with different levels of detail and different time horizons.
In fact, there are 3 different types of plan:
- The (Aggregate) Production Plan (PP): it relates to a fairly long time horizon (1 year) and its aim is to plan highly aggregated quantitative parameters (number of pieces which can be produced, tons of finished product, etc., at the overall level or by product families). The purpose of the Production Plan is to reconcile the need for production capacity (arising from market demand) with actual availability (expressed in man- or machine-hours).
- The Master Production Schedule (MPS): this relates to a limited time horizon (3-4 months) and refers to individual finished products. Specifically, the purpose of the MPS is to decide the size of production batches.
- The Final Assembly Schedule (FAS): it relates to a very short time horizon (1 month) and refers to the assembly-configuration of the finished product. The typical function of the Final Assembly Schedule is to decide how orders are to be fulfilled.
The main characteristic of the entire production planning process is that it is cyclic, so that each period is the subject of a sequence of planning operations, in gradually increasing detail. We can therefore talk in terms of production planning and control phases: each phase starts with the planning of a period and ends with the control stage which starts planning of the next period.
Phase 1: writing of the Production Plan
We have underlined that production planning is cyclic: each period is the subject of a sequence of planning operations, in gradually increasing detail. The process thus proceeds by phases: each phase starts with the planning of a period and ends with the control stage which starts planning of the next period.
The following input data are used:
- Sales forecasts and/or customer orders.
- Production system characteristics and standard operating conditions: shifts, hours, minimum and multiple batches, available of labour net of absences and inefficiencies, etc.
- Current and optimal availability of finished and semi-finished products and materials (stock on hand + quantity ordered + quantity booked).
- Material consumption standards (using product bills of materials).
- Production resource standards (using processing cycles).
In practice, the Production Plan compares and reconciles the demand for and availability of materials and other production resources over a fairly longer period of time (generally a year).
The level of detail in values is generally month by month, using fairly aggregated parameters (families). It is generally revised once a month (or even less often) on a rolling basis (when one month closes another month is added).
With regard to production resources as such (people and machines), it is important to check that the capacity and availability are consistent both over the entire period examined (the year) and within the individual sub-periods (months).
If this is not the case, the following actions should be taken, depending on the problem identified:
- Permanent increase or reduction in internal production capacity.
- Use of outsourcing.
- Increase or reduction in production capacity in specific period, through the use of overtime, flex-time working, holidays, etc.
- Bringing forward production from periods with excess demand to periods with surplus capacity.
With regard to materials management, long-term agreements must be reached with suppliers to book their production capacity and negotiate supply prices and procedures.
At this point the first phase has been completed: the Production Plan is ready.
Phase 2: writing of the Master Production Schedule
The Master Production Schedule (MPS) relates to a limited time horizon (3-4 months) and refers to individual finished products and the relative quantities. It is the production planning tool which establishes the sizes of the production lots, bearing in mind the production capacity constraints which apply in each period.
In other words, the MPS should answer the following questions: what will be produced? When will it be produced? What quantities will be put into production?
Since the MPS derives from the long-term production plan (with a greater level of detail), its time horizon should be shorter or equal to that of the PP, and must be greater than or equal to the production lead time of the planned products. Generally, this plan is revised weekly or monthly.
The MPS input data are:
- Product orders and sales forecasts.
- Product stock levels.
- Safety stocks for the various products.
- Production times of the various products.
- Production Plan with production capacity constraints.
Since, as already stated, the MPS derives from the Production Plan, it must comply with the constraints already established with regard to the maximum resources available (quantity of components or quantity of hours).
Therefore, when writing the MPS, it will be necessary to assess the production capacity required (capacity plan) with regard to both the labour hours available and the availability of machinery to be used. If the capacity available is insufficient to meet the planned need, this must be balanced, either by increasing the resources (overtime hours, if possible), or by bringing forward/postponing production.
Basically, the procedure for writing an MPS is generally the following:
- Setting of the relative time horizon.
- Writing of a first draft of the MPS on the basis of the forecasts and any orders already received.
- Performance of a capacity analysis, via simulations of feasibility of the proposed production schedule.
- Revision of the MPS, if necessary further to the previous point, or modification of the capacity available, until a feasible schedule is produced.
Phase 3: writing of the Final Assembly Schedule
The Final Assembly Schedule (FAS) relates to a very short time horizon (from 1 to 4 weeks) and refers to the assembly/configuration of the finished products. In other words, this Schedule defines what is to be produced and in what order at the level of the working shift and individual processing centre (it therefore refers to individual items, product variants, packs, etc.), bearing in mind the actual availability of materials and man- or machine-hours.
The FAS for a given period must be prepared in accordance with the plans already set out in the MPS. In fact, the overall quantity which can be obtained for a given assembly (article) must not exceed that specified for the common components in the MPS. However, the mix may also vary at the product variant level provided the safety stocks for the specific components of each individual article are available.
The FAS is the production planning tool which:
- Checks availability of materials and components in accordance with the plans prepared.
- Guarantees compliance with the set finished product delivery dates.
- Maintains the warehouse material stock levels at the lowest possible levels.
- Regulates production, purchasing and order issue activities.
The activities previously planned at the MPS level (purchase of raw materials and components, internal processes which produce semi-finished products, etc.) are always scheduled on the basis of the forecasts. If purchasing and/or product design take place in response to orders, there are no forecasts and all activities are planned directly at the FAS level. Therefore, in this case, the FAS may embrace longer time horizons and be revised less often (similar to the MPS).
40 Warehouse KPIs to monitor and measure performance
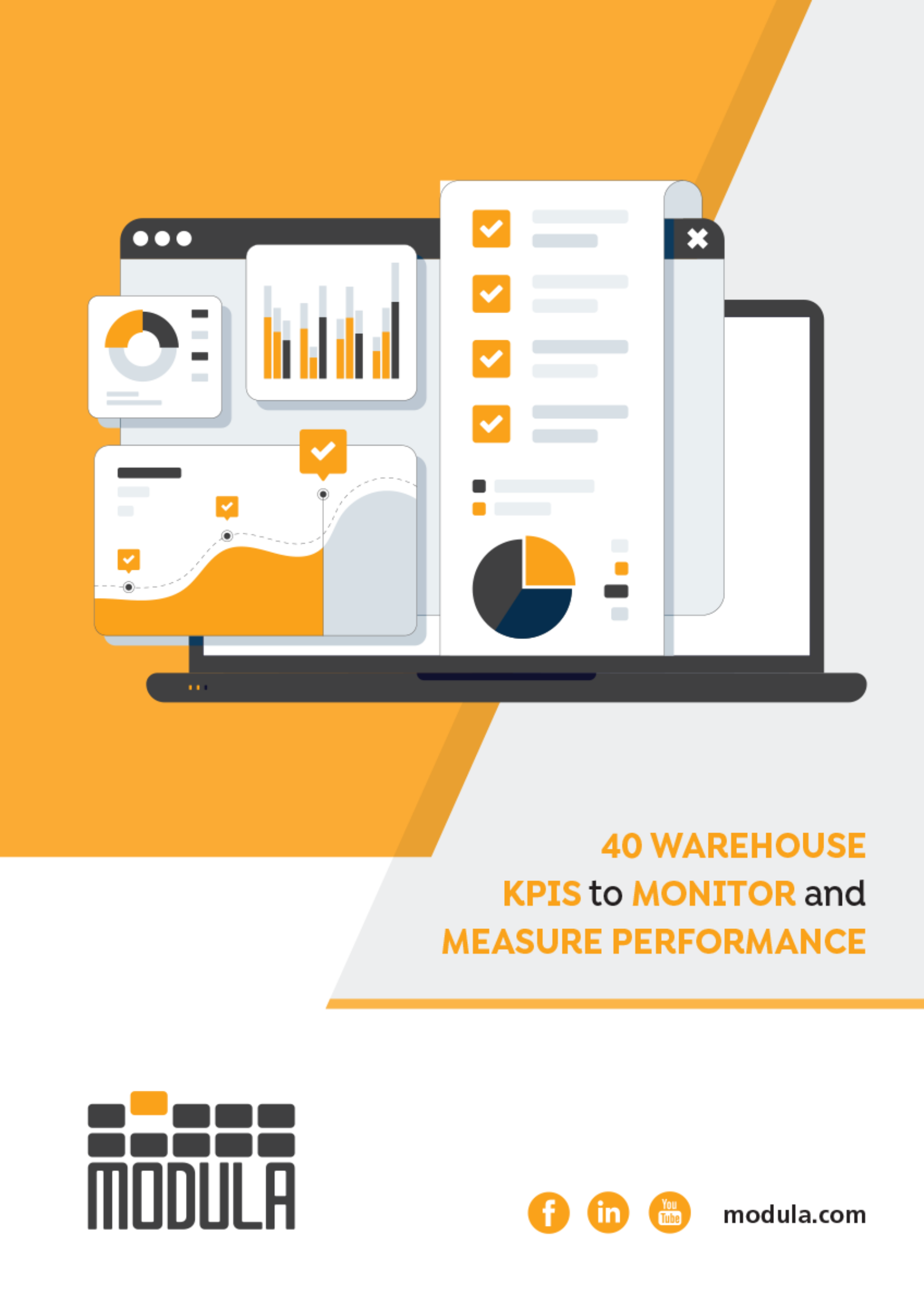