Safety in the warehouse is a fundamental element for effective workplace management and is synonymous with quality of production and of your workplace environment. A safe warehouse means fewer accidents, fewer problems, fewer delays during operations and fewer incidents.
In fact, although these last factors primarily have negative repercussions for your staff, they can also affect the financial health of your business. Frequent accidents mean a reduction in efficiency, replacement of staff, possible extra recruitment, insurance policies and government inspections.
The starting point for eliminating all critical factors which conspire to make a warehouse less safe, and therefore less efficient, is to identify what the actual problems are. The most common “symptoms” which indicate problems with warehouse management in terms of safety are generally as follows:
- Damaged goods
- Disorganised warehouse
- Complaints by operators about onerous tasks or heavy loads
- Frequent accidents
- If you become aware that one of the above problems is occurring constantly, then the time has come to think about the safety of your warehouse.
- When we talk about safety, it’s important to distinguish between the two different types:
- Safety of personnel working in the warehouse: everything that relates to the people working in the warehouse and the various activities they perform when moving goods around, but also the weight limits imposed by manual handling regulations, obstacles and distances between objects depending on whether handling is being carried out manually or using mechanical vehicles.
- Security of goods: everything that relates to the goods being stored. Everything in the warehouse has a value, so theft and damage will negatively impact the business’ bottom line. For this reason, it’s important to pay attention to how goods are being stored in order to avoid this type of issue.
Let’s take a look in more detail.
Safety of personnel
Protecting operators
Looking after the people who work in the warehouse is an absolutely fundamental issue. In this case, the concept of safety can be split into two methods: adoption of accident prevention measures or the ability to intervene effectively when an accident occurs. We all know that prevention is better than cure, and it’s always better to pay attention to and invest money in the former. If operational risks are high or if you are getting complaints from your staff relating to safety then you need to take another look at how you are managing your warehouse.
How? First of all, you must monitor completely all operations. Don’t leave any out just because they may not be performed very often. They may still pose a significant danger for anyone who performs them and they must obviously be redesigned or eliminated.
Now analyse each individual activity and everything that relates to it. This is so you can understand if the working environment is safe enough for the people working there. Are the goods located on traditional shelving units and therefore are people often required to use stairs or carry heavy loads by hand? How safe is the equipment being used? Is the space between shelving units wide enough to allow people climbing stairs to retrieve the goods safely? What is the likelihood that a load could be dropped by an operator? Are you complying with legal limits? These questions will help you to understand any weak points in your warehouse which can act as the starting point for implementing new safety measures.
If, for example, loads are mainly being moved manually, the risk of incidents or accidents is increased compared to movements made using automatic systems or mechanical equipment. As manual handling requires operators to push, lift or drag even very heavy loads, this carries a much higher risk of objects being overturned and puts the health of operators in jeopardy.
The size of loads also has an influence on the quality of work in the warehouse. If the goods to be moved are large and cumbersome, operators are required to make movements or twisting motions which are dangerous to their safety. For this reason, and in the interests of improving safety in your warehouse, you must design your packaging correctly so that it reduces the effort required by your staff to a minimum, or else you need to rethink how their work is organised.
Keep the warehouse clean and tidy
One simple but fundamental rule which will help you maintain a higher level of safety for your operators is really just about keeping the place clean. Especially where oily substances are used inside the warehouse or where the floor of your working area often gets wet, the risk of accidents occurring is rather high.
It’s a good rule in these cases to warn others of the “danger” as soon as possible and proceed as quickly as possible to remove the spillage. Clean the floor to avoid falls which may be dangerous for operators and at the same time create an obstacle for vehicles used inside the warehouse.
Pay attention particularly to transit areas: avoid any type of obstacle which might cause an accident such as packaging, detritus and stationary vehicles. Operators can get distracted, become tired or simply can’t physically see the danger. However, it’s important that every person working inside the warehouse remains alert to these issues to encourage a workplace which is safer for everybody. Being in a hurry to complete the day’s deliveries can sometimes cause omissions or distractions which can have undesirable consequences in terms of safety.
Organise safety courses for all operators and update staff constantly about regulations
Always give a high degree of importance to training new staff before they start work. This goes especially for those workers who use transport and handling equipment.
Make use of the advice of safety experts so you know what types of courses your operators should be sent on and also find out if your warehouse is effectively compliant and safe.
Pay particular attention where new people are employed and/or when new machinery is being adopted. In both cases, before starting production, you must ensure that you have properly explained all safety regulations that relate to your warehouse to your new employees and, in the latter case, ensure that all methods for using the new machines are clear to everyone.
If any equipment requires specific certification for its use, you must make sure that all those persons who will be using the equipment are in possession of this certification and that it is still valid.
Security of goods
Have you ever found goods have been damaged in the warehouse? Or have you noticed that some products have magically disappeared?
These are definitely symptoms of a failure in the way the warehouse’s security is managed. It could be that your employees are not very careful when moving goods about, that the goods arrive already damaged but nobody says anything, or that orders coming in are not complete (you are receiving lower quantities than you ordered), or that someone does not have a clear conscience.
Resolving this type of problem is simpler than you might think: just keep track of all operations involving the goods. For each order coming in, know with certainty what the quantity is and its relative specifications (model, colour, etc.) but also who was responsible for loading it onto the shelves or moving it around.
One of the simplest ways of doing this is to get yourself some Warehouse Management Software to manage and record day-to-day operations. We recommend that you allocate specific tasks and responsibilities to each person or to groups of people so you can more easily get to the heart of the problem. If a particular product type is regularly proving to be faulty, you could turn to the person responsible for its production and request an explanation. You can then understand if it is a problem with how the warehouse is managed or if the problem is down to a careless supplier.
Lots of problems? One single solution which improves security in your warehouse
In the last few years, new types of solutions have been arriving on the market which simplify warehouse management and bring improvements in every area: from improvements to throughput in picking operations to security for the entire storage area.
These are automatic vertical warehouses, dedicated product storage systems which are made up of ultra-robust metal trays propelled automatically by an internal elevator and which are able to hold weights of up to 90,000 kg.
Using a simple digital interface, you can control all the goods in your warehouse and with one click you can bring them directly to the delivery level which can be either internal or external, single or double. As you will have noticed, this avoids all dangerous operations normally carried out by people, such as carrying heavy loads, retrieving them from very tall shelves or gangways and mezzanines, and which are generally the main source of accidents. With automatic vertical warehouses, the operator only has to move the goods from the delivery/loading level which is completely ergonomic, protects the operator’s personal safety and prevents issues related to this type of task.
Another very important aspect is that not everyone has access to the automatic vertical warehouse, only those who have been authorised. In this way, you will know exactly who performed certain loading and unloading actions: who accessed which tray, at what time and in which machine. This will allow you not only to keep watch, in real time, over everything that happens in the warehouse but therefore also better manage orders. Moreover, you will be protected from theft of and damage to your goods.
This type of warehouse is recommended for any type of product, from small items up to heavy weights and even expensive goods and allows you to store goods with different sizes and weights thanks to the use of Dynamic Tray Height Storage: in other words, the machine organises the trays according to the various heights of the goods stored in them in order to best manage the space available and not waste even a millimetre of it.
Once your goods are organised into the closed trays, they can no longer become damaged and always stay clean. For this reason, all the above problems simply disappear!
Want to know if you need an automatic vertical warehouse? Take the test and with a few simple questions you’ll find out if this solution is right for you!
Ideas for warehouse reorganization
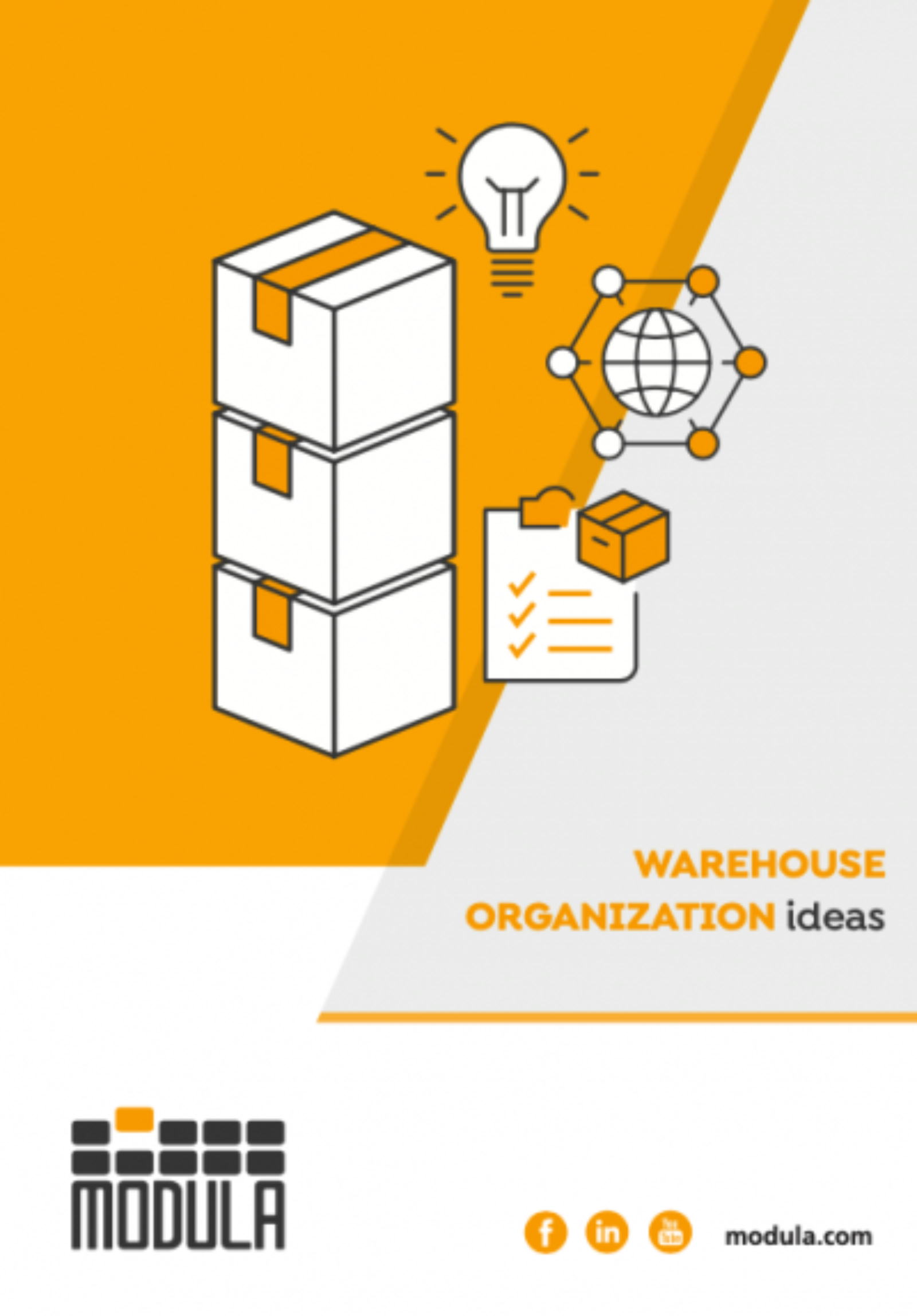