Order point management model
The order point management model consists of reordering constant quantities each time available stocks reach the order point.
This is based on the following assumptions:
- Supplier lead time is known and constant.
- Demand during lead time is a random variable with an approximately normal (Gaussian) distribution where the mean and mean squared deviation are known; this we can define as the average variation from the average value.
Management of available stocks and stock in hand is similar that used in the Wilson model, but the curve is moved up by a quantity equal to the safety stock, which is used to protect stocks against variations in demand during the replenishment lead time.
In this model, the stock manager finds themselves in the situation of having to set both the “Q” and “S0” parameters. There are various possibilities, but perhaps the most practical one is to set them separately (first one then the other). So therefore:
- you first need to set “Q” and in it replace “known demand” with “average demand during unit of time”;
- next set “S0“in order to ensure your clients a particular level of service.
Determining the order point (“S0“)
As we have already seen, the order point is the stock level at which a new order needs to be issued so that stocks do not run out.
A good method for calculating the order point consists initially of choosing the service level you want to provide your clients in terms of probability of coverage (coverage of demand from stocks in the warehouse). In practice, choosing to offer a service level of e.g. 99% means setting an order point so that the probability of being able to despatch client orders is exactly 99%.
At a particular desired service level, we can associate a particular safety coefficient (“K“). If we assume that the demand random variable during supplier lead time is a normal (Gaussian) random variable, then this “K” value can be determined by consulting special reference tables (a sort of logarithm table like you used at school).
Fixed interval stock management model (T, S)
The fixed interval stock management model consists of reordering a quantity (variable) at constant intervals (“T“) to bring available stocks back to a preset level, called the maximum stock level (“S“).
The underlying assumptions are the same as for the order point model:
- Supplier lead time is known and constant.
- Demand during lead time is a random variable with an approximately normal (Gaussian) distribution where the mean and mean squared deviation are known; this we can define as the average variation from the average value.
- Management of available stocks and stock in hand is similar that used in the Wilson model, but the curve is moved up by a quantity equal to “SS” (safety stock).
The safety stock can be calculated by:
SS = standard deviation of error * service factor
In this model, the stock manager finds themselves in the situation of having to set both the “T” and “S” parameters. There are various possibilities, but perhaps the most practical one is to set them separately (first one then the other). So therefore:
- you first need to set “T” using the formula (seen earlier in preceding snippets) for the optimum Wilson rotation interval and making sure to replace “known demand” with “average demand during unit of time”;
- next set “S” in order to ensure your clients a particular level of service.
Determining maximum stock level (“S“)
The maximum stock level is the amount of stock in hand at the moment an order is issued to a supplier, in order that current levels of demand can be met right through until a new order can be placed. In practice, the maximum stock level must ensure stocks can cover the period equal to the replenishment period (“T“) and supplier lead time.
In this case, too, in order to calculate your maximum stock level effectively, it is advisable first to choose the service level you want to provide your clients in terms of probability of coverage (coverage of demand from stocks in the warehouse).
Overall considerations about these models of stock management
Order point model or fixed interval model?
When choosing between these two systems, it is a good idea to keep the following considerations in mind.
- The fixed interval model gives you a real order scheduling capability for individual items with the possibility of grouping everything coming from the same supplier together on the same date. This therefore means fewer overall orders to issue and better organised procurement and goods inwards operations.
- In equivalent conditions, the fixed interval model leads to higher stock levels compared to the order point model, as checks are less frequent and demand can undergo bigger fluctuations over longer periods. This can be particularly disadvantageous when the replenishment time is greater than the supplier lead time.
- If continuous checks are being made and reordering at any time is permitted, a fixed interval system can be combined with an order point indicator and this can help to reduce safety stock levels.
Bear in mind that the models described here “work” on the basis of past demand that has been recorded (average demand and fluctuation rate).
In businesses where effective sales prediction systems can be implemented, these models can actually be slightly modified in order to increase performance in terms of reducing stock levels needed to provide the same service level to clients.
40 Warehouse KPIs to monitor and measure performance
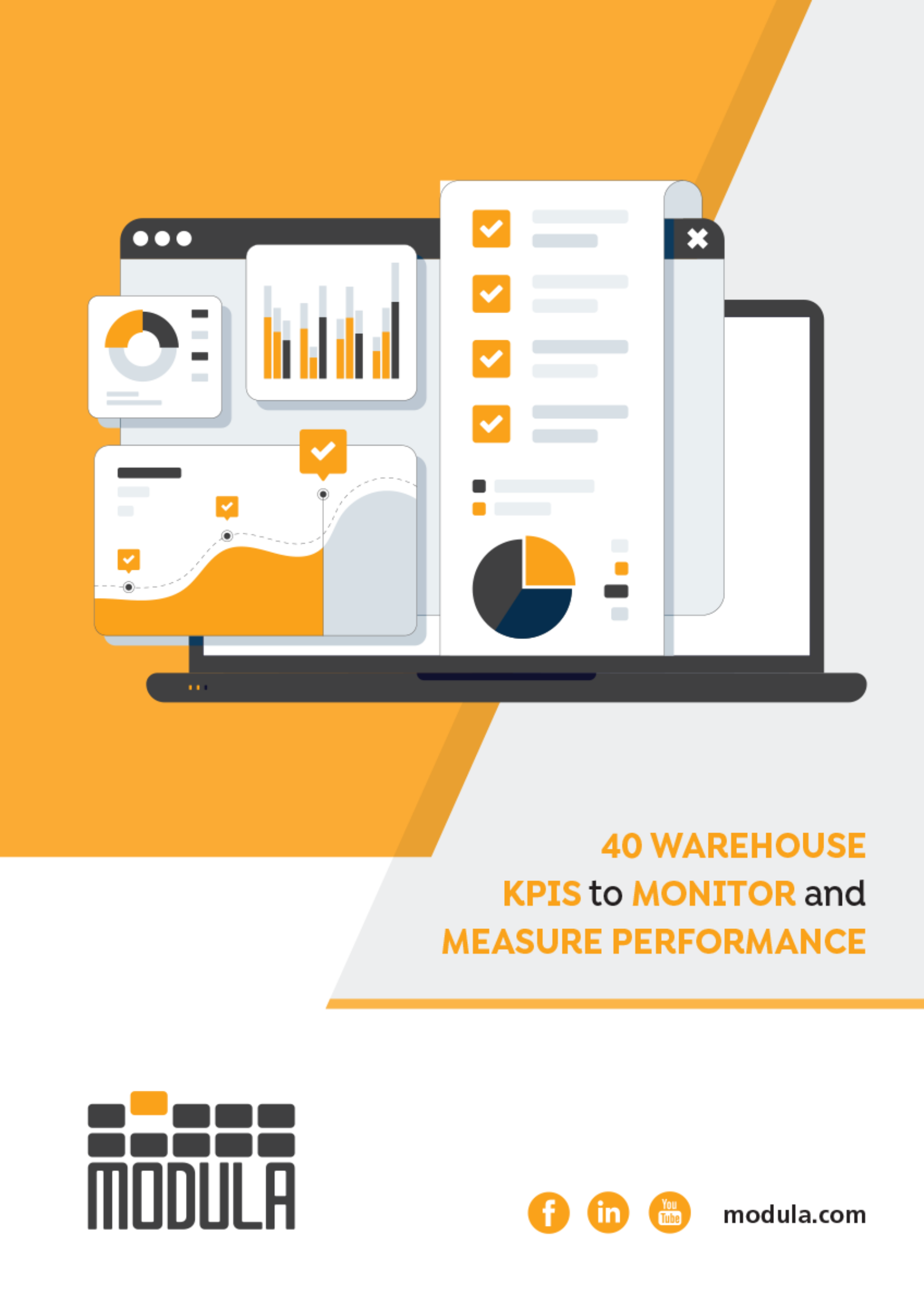