Automated warehouse management systems are designed to overcome some limitations of conventional systems by maximizing storage capacity in terms of efficiency, speed, space, precision and operating costs.
The main automatic warehouse management systems include:
Stacker crane automatic warehouse
In a stacker crane automatic warehouse, pallets are stored and handled by means of stacker cranes, and these operations are efficiently managed by means of the central WMS IT system.
The structure may be prefabricated or free-standing, can be very tall and is able to manage a large number of product codes.
The main benefits of stacker crane warehouses compared to conventional systems are:
- Picking process speed: the goods are brought to the operator, reducing order fulfillment times
- Space optimization: handling aisles are reduced to a minimum
- High selectivity and high density
- More control of products in store
- Low operating costs
This type of automated warehouse provides a clear improvement in terms of storage efficiency and operating costs, although the initial investment is high.
Vertical lift module automatic warehouse
Vertical buffer module, or Vertical Lift Module (VLM) automatic warehouses are leading-edge, compact automated storage structures which can be perfectly integrated with production processes and internal ERP systems.
Perhaps the most obvious benefit of a vertical automatic warehouse is the saving in floor space, which may be as high as 90%.
Compared to conventional models, management with a VLM also provides a sharp improvement in safety, speed and inventory precision, cutting times, costs and errors.
In other words, this is a real revolution in efficiency, the spread of which is perhaps only hampered by lack of awareness of the results and potentials of this particular automatic management model.
Those who are worried about having to stop or slow down production because they view automatic systems as complex and therefore think lengthy assembly times are required have no cause for concern.
The installation times for a vertical warehouse are very similar to those for conventional static solutions and the transition to automatic operation can also take place gradually.
The idea that automatic vertical warehouses cost a lot more than conventional solutions is another of the common misconceptions about automatic warehouses.
The investment is definitely not unaffordable and a rapid ROI is guaranteed.
In Italy, the option of “Hyper and Super Amortization” for tax purposes under the Industry 4.0 scheme makes the transition to automatic warehouse management even more financially attractive.
In other words, there are many reasons for investing in an automatic vertical warehouse.
Now let’s take a look at the differences between them and stacker crane warehouses.
Difference between stacker crane and vertical warehouses
The first difference between stacker crane and automatic vertical warehouses is that the latter do not need aisles for transporting goods, and all the space available is used for storage.
What’s more, any type of goods can be stored in a vertical warehouse, from heavy, bulky products to small parts, without the limitations imposed by pallets.
The automated system guarantees the optimization of spaces between trays, improving storage efficacy.
How to optimize picking operations?
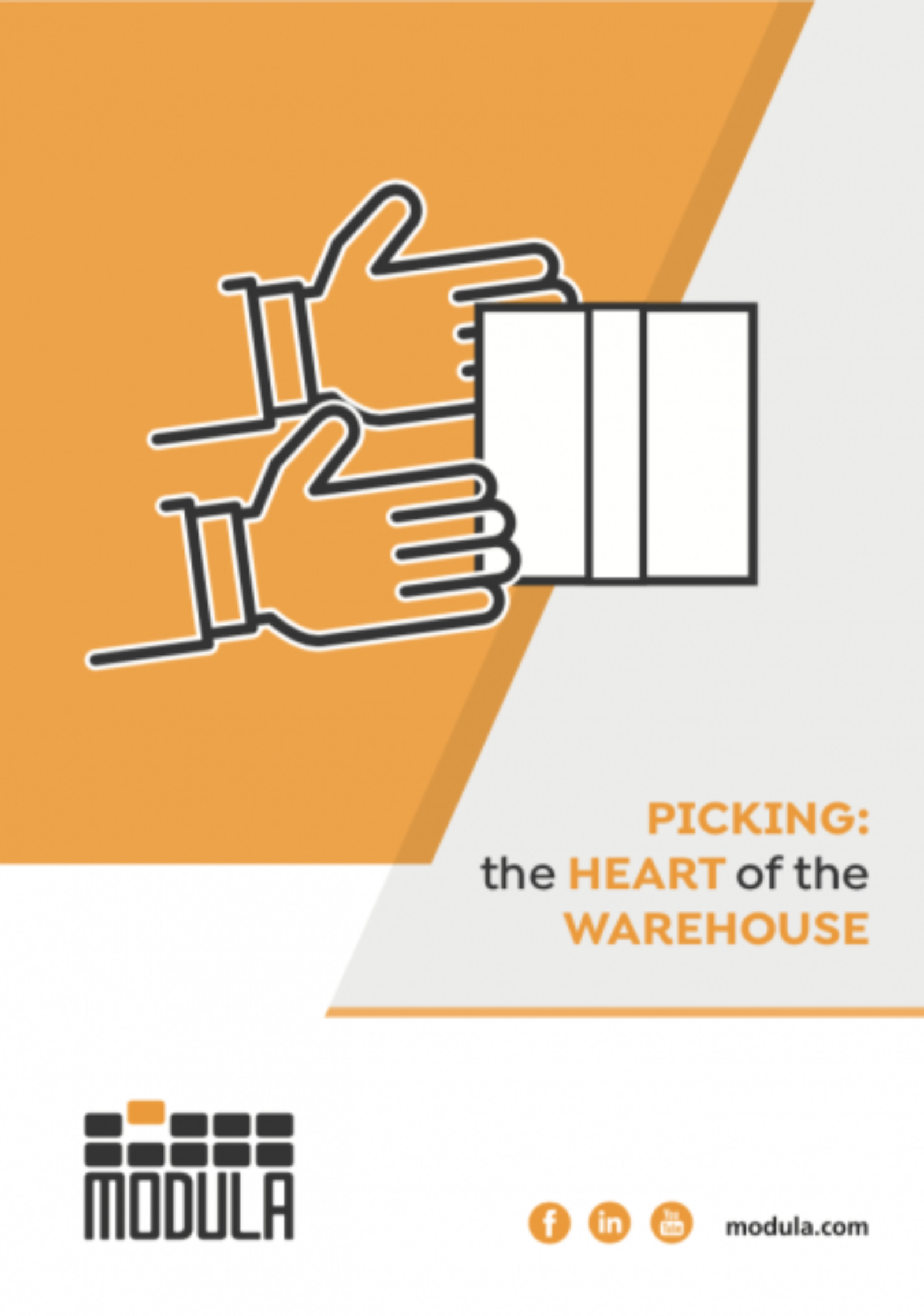