Your warehouse performs a fundamental role within your business. It cannot simply be interpreted as a physical entity. It is an important part of the production chain and must therefore be managed using strategic company activities.
Over the years, warehouses have changed. Today, warehouses can even be expanded beyond your own company for various reasons including outsourcing, but also due to changes in supply and production policies.
This is why you need to completely redesign your warehouse in order to maximise its performance and eliminate waste in terms of money such as a lack of space, and in terms of time lost looking for items inside an extremely large and poorly organised space such as in your warehouse.
But how do I redesign my warehouse, maximise performance and avoid blowing my budget? What steps do I need to take?
First of all, you can start continuous improvement activities aimed at eliminating small everyday problems (direct deliveries from suppliers, redesigned packaging to save space, improve forecasting methods). Next, management must act and undertake more substantial operations, invest in concrete ways to redesign the warehouse and employ expert consultants from the logistics sector.
The various steps you need to take in order to design a VLM are detailed as follows:
1. Gantt Chart and estimate of investment needed for a VLM
Estimating the investment required means conducting careful analyses in order to show that the project meets the set objectives. It is very important to carry out estimates of the duration of the project and schedule in operational objectives, and also consider that the project may not be achievable within the established timescales.
We recommend getting help from experts with long experience in the field. In this way, it is easier to carry out analogue estimates based on past operations, or on estimates which concentrate on the parameters derived from a sample of work already carried out.
But can redesigning my entire warehouse be profitable? How long will it take?
Building a new warehouse or adopting new technologies has a cost which must be quantified and split into timeframes often with the aid of a Gantt Chart.
This Cartesian diagram represents activities and indicates when a particular activity should start and end. On the X-axis you have the time period from the start to the end of the project, and on the Y-axis you have the things that must be done to bring the project to completion. By entering all your estimated activities, you can have a full overview of the project. At a glance you can see which to give priority to, which are overdue, which ones to carry out concurrently in order to save time and which ones depend on others.
This chart is used to keep control over the timing of a whole range of activities. This can be linked to other detailed information: who is to carry out the task, whether this should be full or part time, how much of the task has been completed and how much remains to be done.
2. Audit and Feasibility Study
It’s important to start by analysing strengths and weaknesses and defining actions suited to the purpose you want to fulfill and your overall objective. Start by monitoring your warehouse’s performance in order to identify and eliminate critical issues: this is how the audit is carried out.
Here you need to concentrate on performance indicators covering processes, tools, technologies and the costs involved, and not least the human resources involved.
By basing your actions on a feasibility study, you can resolve problems and improve operating results. By analysing data, you can identify alternative ways of organising your warehouse, storing goods and logistics in general, compare them and choose the one that has the best cost/benefit ratio.
Alternative solutions will have to consider various aspects such as the site master plan, warehouse layout, operating and logistics criteria, human resources and costs involved and timescales. On the basis of all the collected information, company management will be able to choose the best possible alternative with which to proceed.
For all the details, please read the article about how to compile an Audit and Feasibility Study.
3. Slotting: product positioning
In order to achieve the lowest possible warehouse management cost and least possible movement, products must be positioned correctly in the picking area. By mapping and analysing warehouse activity logs, you will be able to understand where to place products inside your VLM and which products to keep close.
A Slotting analysis allows you to understand where to position products and how to classify them within your warehouse in order to save time and optimise resources.
For all the details, please read the article about Slotting Optimisation.
4. Project Detail
At the moment you decide that it is worth making the investment and want to proceed, you need to conduct a detailed analysis of the project. This means assessing the merits of the functional, technical, operational and systemic issues which were flagged by the feasibility study.
By studying and analysing project data, you can determine a final layout with drawings, plans, cross sections and components.
Your logistics project must include issues with buildings (e.g. with VLMs you can consider implementing them outside, known as External Covering, perhaps also assessing anti-seismic solutions) and facilities (e.g. sprinkler systems, heating, cooling, lighting and compressed air).
Operating procedures can then be defined and a detailed Gantt chart compiled.
5. Dynamic Simulation
Dynamic simulation seeks to predict how a system or facility behaves in various alternative scenarios. Based on a map of your company’s logistics processes and comparing them against various scenarios, you can identify risks and bottlenecks and monitor your system’s performance.
This starts with collecting data and validating the conceptual model in order to share all the studied scenarios, hypothetical cases and assumptions made between the entire design team. You then proceed by defining all the scenarios you want to test and the level of confidence expected for the comparison of output results.
Numerical indicators are then converted into project solutions and results illustrated in order to help the client make decisions.
For all the details, please read the article about Dynamic Simulation for minimising risks in logistics.
6. Construction Project
A dynamic analysis is valuable for when you want to then proceed to the construction project. Once the project has been defined and the suppliers chosen, you then proceed with a critical examination of the construction plans and review the various documents relating to automation.
Based on the company’s Gantt chart, you proceed to update it based on decisions taken and on the construction project which will undoubtedly adversely affect the project’s flow and deadlines.
You then move to acceptance through FAT (Factory Acceptance Test) with documentation prepared by all suppliers. This involves inspecting the equipment and components before delivery or final inspection.
By guaranteeing the high quality of the components, you also ensure their integrity in the factory. Conventional functional testing or simulation ensures that the system or the equipment meets the specifications and contractual obligations. This involves checking documentation such as manuals and any sort of instructions, designs, drawings, structural and instrumentation diagrams.
This is also true for VLMs which, for example, come with an instruction manual, a maintenance manual, a declaration of conformity and other documents such as a warranty or TÜV certification.
These documents are essential for periodic inspections either during construction or afterwards.
It is very important to have a Project Leader who will monitor all of the project’s implementation phases. Monitoring the work of suppliers and supervising commissioning is essential right through until the Site Acceptance Test, when the system is tested for compliance with the test plans and technical specifications and to demonstrate that the system is correctly installed and interfaces correctly with other systems and peripherals within its working environment.
In the case of a VLM, this phase concludes with installation and testing of WMS software and any interfacing with your company’s ERP system.
This phase concludes with the hand-over document.
Ideas for warehouse reorganization
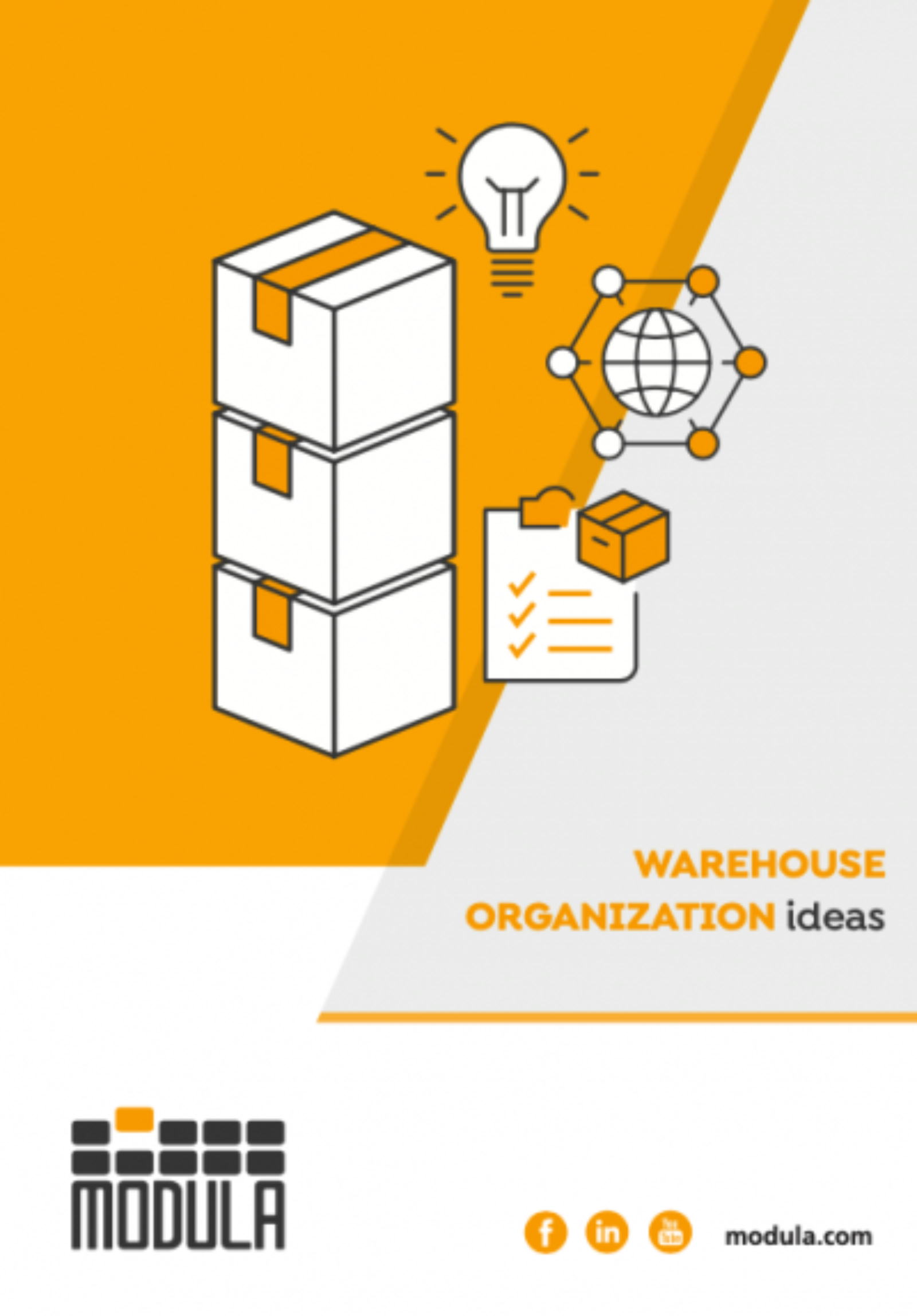