Improve the quality of services, be more competitive in the marketplace, reduce operating costs, increase efficiency and productivity. There are so many goals a company has to aspire to in order to maintain a profitable business, but perhaps not everyone is clear about how achieving any of these goals requires a complete warehouse reorganisation. This step is now practically mandatory and one which cannot be underestimated, especially by small- and medium-sized companies which do not have the tools or the technology for optimum warehouse management.
According to some studies, the costs linked to warehouse management have a significant effect on company turnover and can adversely affect its financial viability. This is why a warehouse reorganisation project can prove fundamental to stopping waste and improving productivity.
Optimising warehouse logistics: critical points to address
Amongst the various issues to be addressed are: product availability – this must always take a warehouse’s stock rotation factor into account in order to best optimise available space; true management of logistics flows – this can waste resources and increase maintenance costs; goods monitoring – goods locations can often be difficult to map and this requires operators to waste a lot of time looking for them.
Issues which can also adversely affect logistics management are: a lack of standardised procedures which can simplify the work of warehouse staff, and resources able to manage inventory in real time which, if not kept properly up-to-date, can adversely affect the normal operation of a warehouse.
Not only that, but an inability to maintain a high quality service risks leaving you with dissatisfied customers, discontinued stock may have to be disposed of in order to make room for other incoming materials, and analysing statistical data is fundamental to keeping control over the performance of your warehouse processes. There are so many issues to address.
You have to pay particular attention to those products which are fundamental to the profitability of your business. As we know from the Pareto principle, 20% of products produce 80% of profits. Identifying these products and the solutions needed to manage them best is fundamental to ensuring your customers receive high levels of service and to protecting your profits.
Fundamental elements of warehouse organisation
Generally speaking, the costs involved in a complete warehouse reorganisation tend to frighten many businesses, but by making a few smart choices and focussing on the most advanced technological solutions, you can manage your warehouse logistics in the most profitable way possible and get a return on your investment.
Of course, each company is different and needs specific strategies in order to optimise warehouse logistics, but there are some basic organisational elements which work in all sectors and should not be overlooked.
If the goal is more efficient and safer warehouse management, following these 8 steps is fundamental.
- Get a Picking List – a real list containing all the information you need to manage operations involved in picking goods off the racks (and refilling them), monitoring incoming/outgoing flows, having the clearest possible idea of stock levels and facilitating the movement of operators and their vehicles, saving precious time.
- Define precise storage criteria in order to optimise the storage of raw materials, semi-finished products and finished products, keep stock levels to a minimum and achieve a cleaner and better-organised warehouse. Whether they are more or less lightweight metal racking units, gravity-fed dynamic warehouses or automatic storage systems such as the carousel, mini-load or tray-based vertical lift module, it is a good idea to identify which ones are most suited to your business.
- Provide a system which can track the goods stored in your warehouse and monitor incoming and outgoing products via standardised procedures which use advanced technology such as RFID. This technology ensures products are tracked using Wi-Fi radio frequency transmission.
- Carefully schedule all warehouse activities so that flows are synchronised, stocks are properly managed and bottlenecks avoided. These issues are always a problem for companies as they risk interfering with the normal operation of the warehouse, slowing it down or, in the most serious cases, actually bringing it to a complete standstill.
- Handle orders with a high level of precision and keep stock levels up-to-date in real time: this is the only way to simplify inventories and keep the risk of errors to a minimum. To keep track of all activities being carried out inside your warehouse, you can make use of a simple Excel spreadsheet in which you record all order, stock and returns information. Alternatively, you can invest in a good warehouse management software package. This will surely be more expensive, but it will of course make this activity much easier.
- Set company targets to be reached so you can have a clear idea from the start of what standards you wish to maintain in terms of quality and throughput from your service, and also so you can adapt your warehouse logistics to achieve them. This will mean you avoid disappointing your customers and ensure you meet their requirements fully.
- Use standardised solutions which help you reduce your costs and improve the quality of your services and safety, making the work of your operators easier too.
- Keep your warehouse under control by using precise data reporting and defining key performance indicators (KPI) which are essential for understanding whether the warehouse is close to achieving your predetermined targets or not.
Solutions for improving warehouse logistics
In some cases, reorganising a warehouse can turn out to be quite complex, but all you need to do is put your trust in technology and adopt various standardised solutions which guarantee its regular operation and ensure more efficient management.
One of the most common procedures used to speed up the registration of incoming products, simplify order and stock management and keep inventory up-to-date is RFID (Radio Frequency Identification). This technology can identify goods automatically using radio frequency electromagnetic fields, or RFID tags, which are simple and intuitive to use. RFID tags, powered either by the reader device or a battery, are physically placed on the goods themselves and these are then constantly monitored and identified via their radio signal.
Alternatively, you could opt for another type of automatic warehouse management, called a Vertical Lift Module. These systems are proving to be the ideal solution for businesses who need to optimise logistics processes, make the work of operators easier and provide a safer working environment for them, simultaneously increasing the quality of services and productivity.
Thanks to their ability to store goods vertically and thus save a significant amount of floor space, tray-based vertical warehouses, known as VLM (Vertical Lift Module), actually allow you to monitor all incoming/outgoing flows constantly, keep control over storage processes, manage stocks more efficiently and ship orders more quickly. These systems are really easy to install and can be fully integrated into all production processes. Moreover, there are even really small and compact versions starting from 4 metres in height and 1.6 metres in depth.
The advantages of a Modula automatic vertical storage system
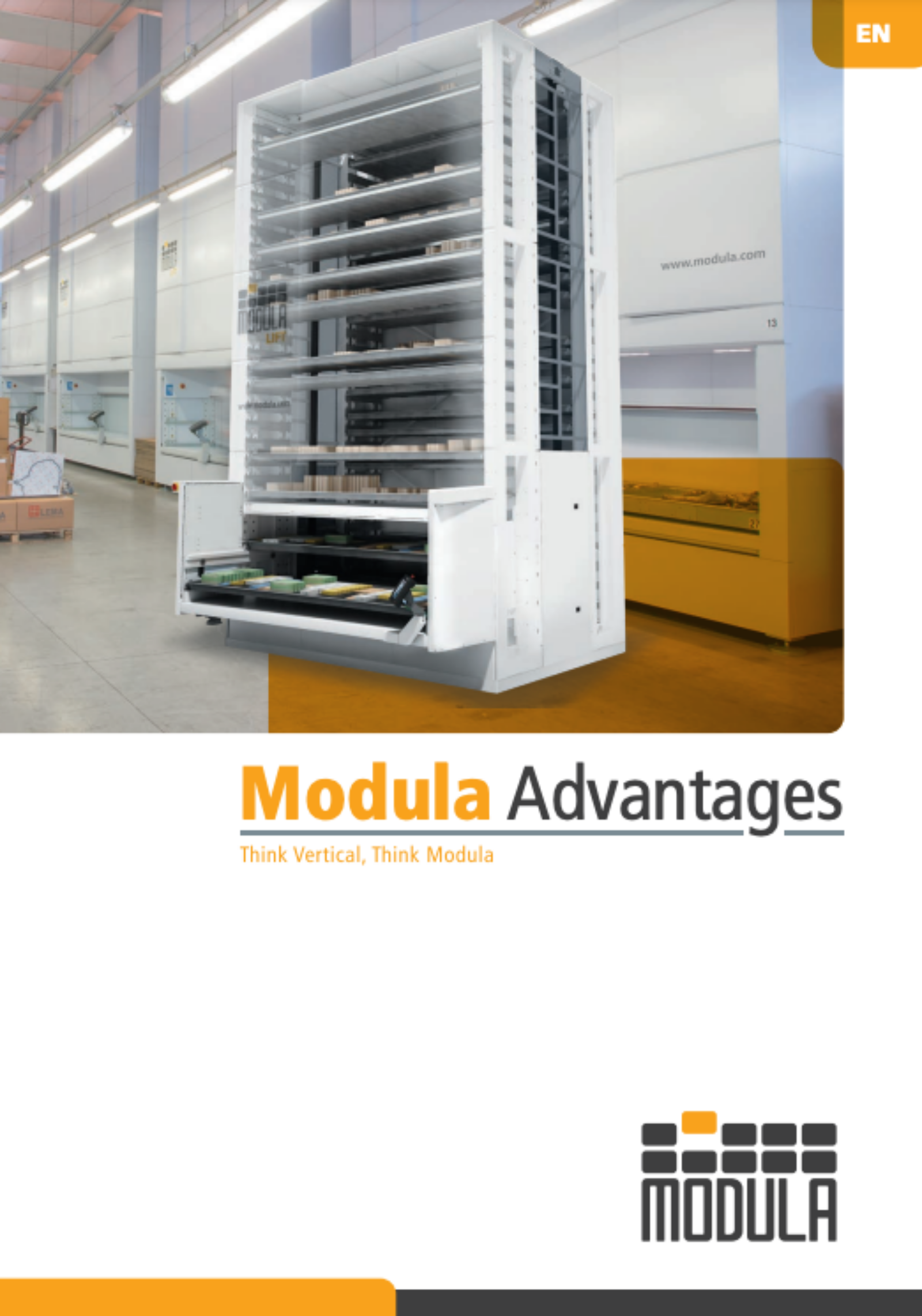