Personal protective equipment (PPE) is an essential tool in every company to protect employees from potential risks and injuries.
Maintaining an adequate supply of PPE in the company is crucial to reduce the risk of workplace accidents, ensure compliance with safety regulations and create a safer working environment for everyone.
In this article, we’ll tell you everything you need to know about PPE vending machines, from types to benefits, and introduce you to our latest Modula storage solution, for storage and distribution of your PPE.
What is personal protective equipment (PPE)?
Personal Protective Equipment (PPE) refers to a series of items designed to protect workers from risks that could cause injury or illness while they perform their everyday tasks. PPE is designed to protect against physical, chemical, biological, electrical and mechanical hazards or any other source of potential injury; these devices include items such as helmets, gloves, eye protection, high-visibility clothing, safety footwear, earplugs or headphones, masks, respirators and protective clothing.
A wide range of PPE is available, with the most common items used for:
- Eye protection: safety glasses and goggles, face shields
- Hearing protection: earplugs, earmuffs
- Respiratory protection: respirators
- Hand protection: gloves
- Head protection: hard hats, air blast caps
- Foot protection: safety shoes, boots
- Body protection: overalls, aprons, vests
- Fall protection: safety harnesses, lanyards and lifelines
- Specialist PPE: thermal protective clothing, chemical suits.
Personal protective equipment is therefore essential to ensure worker safety, especially in the logistics and warehouse management sectors, where the risks of accidents are linked to different factors such as handling of loads, use of forklifts or other vehicles and movement of heavy goods or those that could cause injury. Adequate training on the use and maintenance of PPE is therefore essential to ensure its effectiveness and durability over time.
There are specific regulations that establish how PPE must be stored, according to specific criteria relating to the amount of PPE available, its unique assignment, handling of sizes, departments and, when possible, shared use. Therefore, investing in safety, by properly storing PPE and providing regular employee training, not only reduces the number of accidents at work, but also improves operator productivity, creating a safer and more sustainable working environment.
How does a personal protective equipment (PPE) vending machine work?
More and more companies in a range of industries are installing and using PPE vending machines at their premises; this technology is an efficient and cost-effective way to distribute safety devices in the workplace.
These machines typically operate according to the stages below:
- Identification: Employees use their badges to identify themselves and gain access to the vending machine.
- Selection: Once they have identified themselves, employees can choose from a range of PPE items stored in the machine. The machine interface, which can be a touchscreen or a button, enables users to select the item they need.
- Delivery: The vending machine dispenses the PPE item. The item is typically stored in a compartment and is dispensed once the selection has been made.
- Tracking and inventory management: The PPE vending machine actively tracks and manages stock by recording which users have picked up an item, when they have done so and which item the machine has dispensed. These data are important for managing inventory levels and understanding the most commonly used models.
- Refills and maintenance: Regular maintenance and replenishment of the machine is essential. Maintenance ensures that the machine is working properly and can dispense items promptly.
The implementation of PPE vending machines in logistics and warehouse environments not only facilitates the distribution of protective equipment, but also improves inventory management and security and therefore overall operational efficiency. These systems ensure that workers always have access to the PPE they need to perform their duties safely.
Modula Next, a valid substitute for PPE vending machines
Modula offers advanced automated storage solutions and warehouse management systems, ideal for maximising space efficiency and improving inventory management in various industries, including logistics and warehousing.
Our latest innovation, Modula Next, is an advanced solution compared to traditional industrial PPE vending machines.
Modula Next is designed for the automatic storage and picking of a wide range of items, offering a significantly higher storage capacity significantly than similar machinery. Its vertical design makes the most of the available unit height, giving you the option to store many items in a relatively small and centralised space.
In Modula Next, the only part that opens is the dedicated compartment – fitted with movable windows corresponding to the SKU sought, to guarantee unambiguous and tracked access. Each opening automatically updates the number of stocks and sizes available, ensuring accurate and secure inventory management. It is therefore easier for workers to quickly find and access the equipment they need.
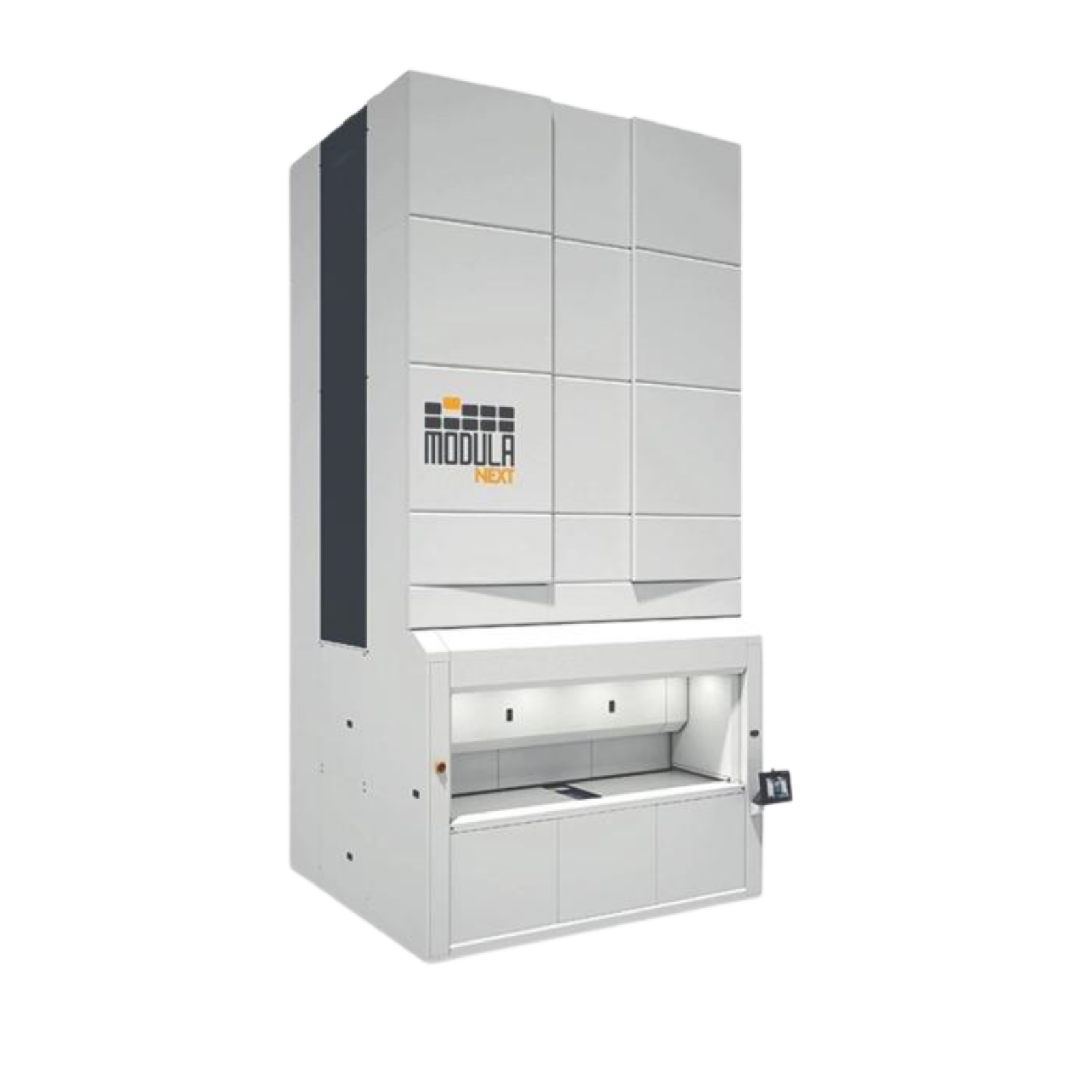
Find out how Modula Next can help to handle your PPE
Advantages of using Modula Next as a PPE vending machine
The centralised Modula Next system saves time and keeps PPE in an organised and efficient way, reducing clutter and the risk of lost stock, optimising workflow and increasing overall productivity.
One of the main advantages of using Modula Next is its extraordinary ability to optimise the available space, allowing a wide variety of PPE to be stored in a small area. On top of this, precision in picking of materials, ensured by the system’s advanced technology, which minimises the possibility of human error and guarantees that each operation is carried out accurately and error-free.
When used as a vending machine, Modula Next ensures that PPE is protected from dust, moisture and direct sunlight, keeping it in optimal condition for use regardless of the type of activity for which it is used. Plus, thanks to Modula WMS, the system records each pick, ensuring efficient inventory management – made possible by real-time monitoring of PPE stocks, with precise data on the levels and models used.
It is important to emphasise how the modular design of Modula Next offers easy configuration, customised according to inventory and location needs, with adjustable compartments for different items and sizes to make it suitable for various sectors. In contrast, PPE vending machines have limited scalability, as they are typically designed for a specific range of PPE items and cannot always easily be adapted to variations in stock type or size.
Want to know more?
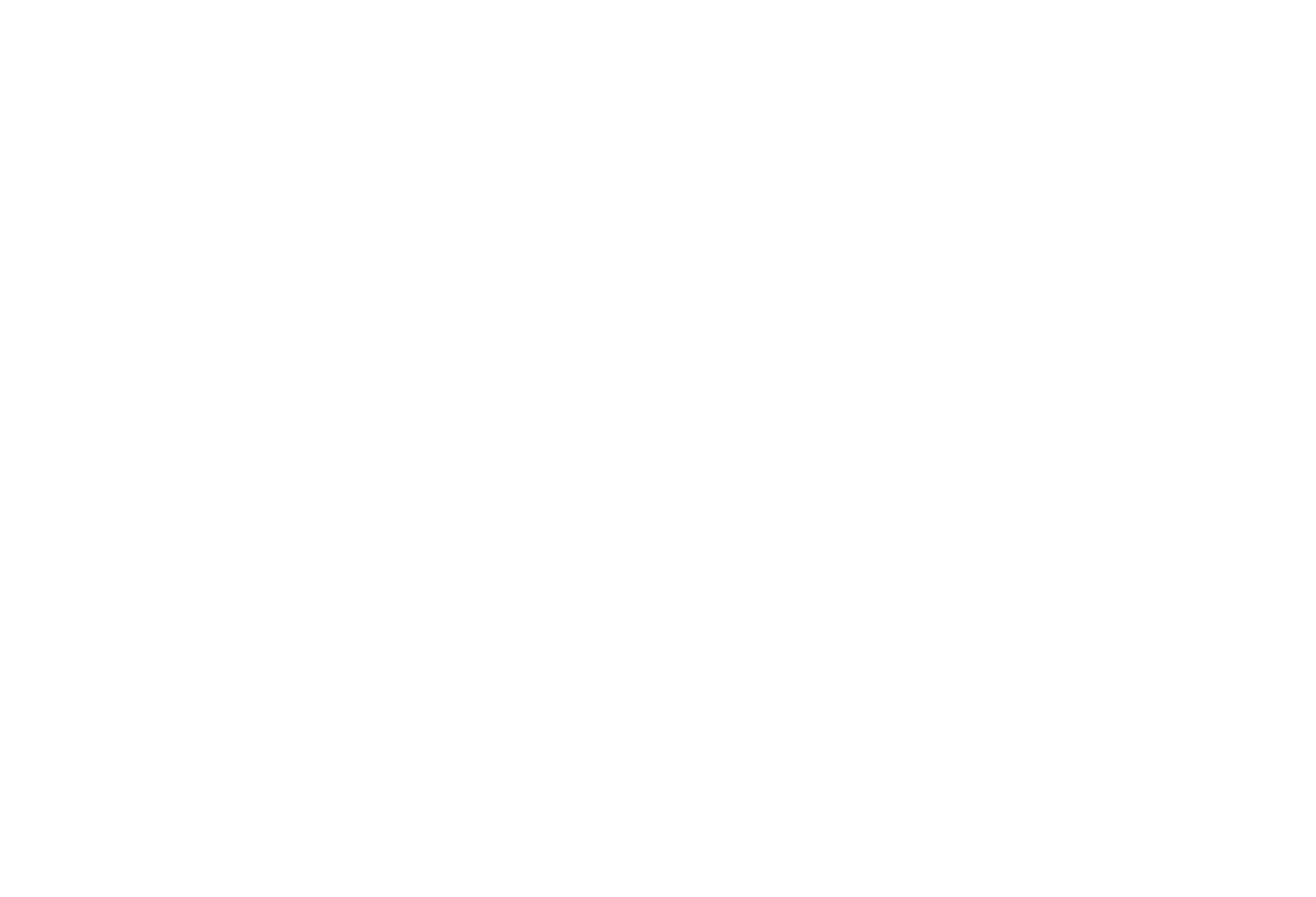