Modula technology solutions have long been synonymous with order, safety and automation for companies that adopt them in their production departments or in logistics. Easy to use and equipped with advanced security systems, our products are indispensable to speed up operations, reduce the number of errors, speed up operations and for extensive tracking and control of all operational stages.
Behind this technology and innovation is a research and development department made up of a team of over 40 people whose everyday work focuses on the search for new solutions, in terms of both the mechanical and software aspects. This know-how translates into automated vertical and horizontal warehouses, now also on display in a showroom open to visitors.
Showroom at new HQ in Fiorano Modenese
At our new headquarters in Fiorano Modenese – with a surface area of over 13,000 m2 – the showroom is one of the architectural and experiential focuses of the facility, giving people, visitors, clients and authorities the opportunity to visit, learn about and experience Modula solutions face to face.
For people working in the supply chain world, it is not always easy and immediate to understand a state-of-the-art tray-based vertical lift module; often confused with stacker cranes or carousels, Modula automated vertical warehouses are true giants in storage, cabinets that can hold up to hundreds of steel trays, used to store goods within their aluminium panels.
The Experience Centre thus appears as a vertical city, with a variety of warehouse models standing up like multi-storey buildings.
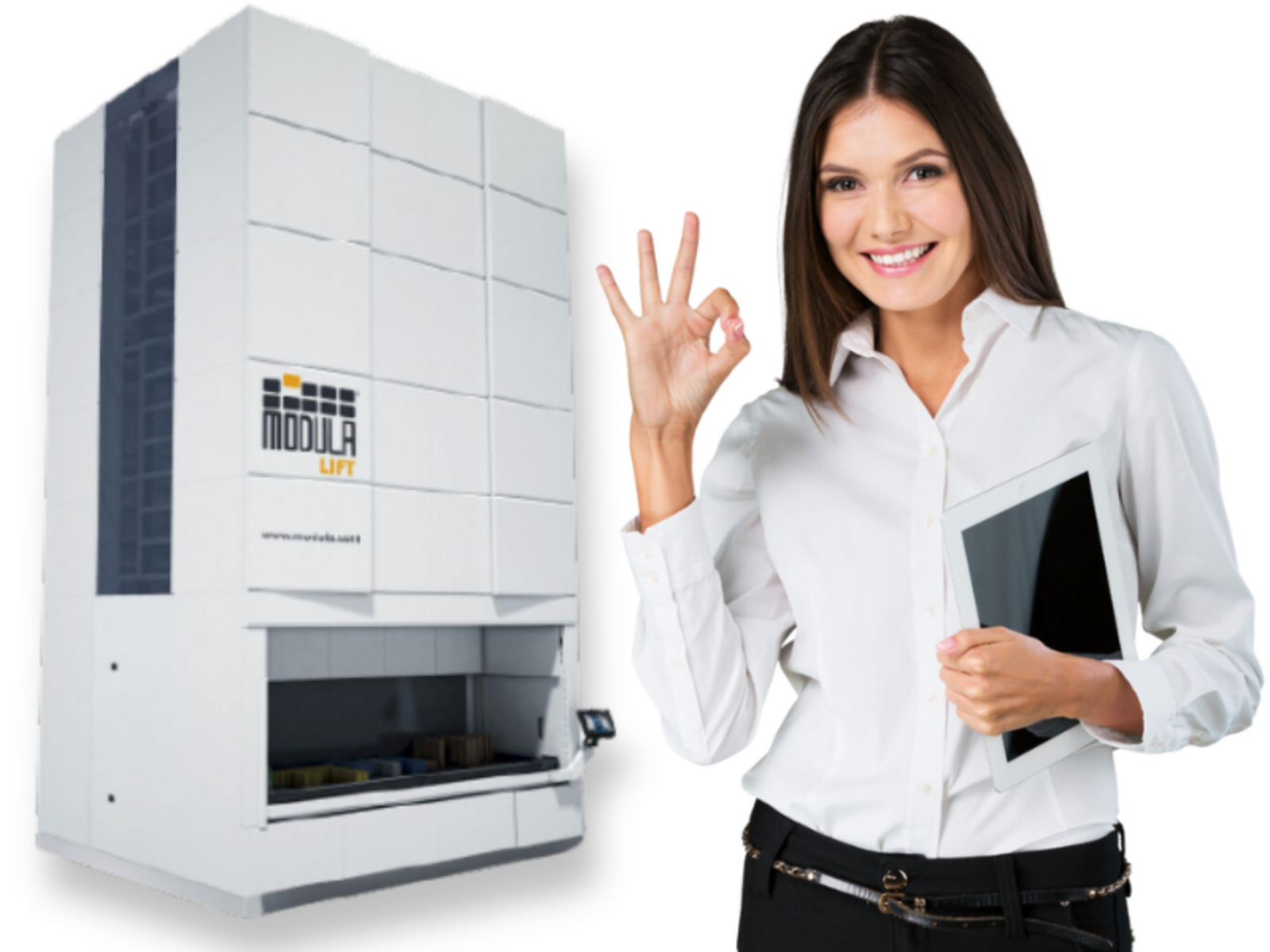
Already aware of Modula's mission and values?
Find out what drives and moves the process of innovation and implementation of Modula solutions.
Experience Modula modularity, options and accessories face to face
The very name “Modula” refers to modularity, one of the most important features of its automated solutions. A wide range of customised configurations can be adopted for Modula warehouses.
The systems on display at the Experience Centre include two pairs of Modula Lifts, 10 metres high with differing tray widths, grouped into twos of opposite bays. The tray payloads also vary, ranging from 200 to 1000 kg each.
Various options are installed in the systems on display, to show visitors some of its many possible uses:
– Laser pointer for improved product identification during picking
– LED bar and alphanumeric LED bar
– Trolley, to extract the entire tray and move it around premises, made possible by an ergonomic and safe solution on wheels
– Barcode reader
– EKS system and magnetic badges for access control
– System to protect electrical equipment from shocks and discharge the current to earth, to protect goods and operators.
FUN FACT:
Vertical warehouses are sometimes known as ‘paternosters’. Do you know why?
The old models, with no central elevator, worked like a chain that rotated to move all the trays, exactly like a chain of rosary beads (‘pater noster’) to be wound vertically through the hands. This technology involved waiting for the entire tray rotation cycle for the operator to pick from the one they needed. Conversely, current Modula warehouses have a central elevator that moves on the vertical axis and takes the trays into the ‘front’ or ‘rear’ towers where they are stored, moving like a shuttle and shifting only one tray at a time.
Innovative picking solutions: Modula Lift external and internal bays
The four Modula Lift systems at Fiorano are also equipped with both an external and internal bay: the difference between the two lies in more ergonomic picking from the external bay, whereas the internal one is more compact and saves space. According to configurations, Modula Lifts can work at single or dual delivery levels; in the section of the showroom focusing on picking solutions, both options can be viewed and tried out.
Among the four Lift systems there, a picking station has been set up, to handle various orders using put-to-light systems, as well as a picking cart to prepare the SKUs, then move them around the facility. This technological ecosystem of vertical warehouses and picking solutions helps operators with order preparation, especially in more complex cases of batch picking or multiple orders.
Get to know the Modula WMS system and the differences with Modula OS
All this can only be possible with the WMS system, vertical lift module management software to connect all the technologies and provide 360° control of the warehouse, stocks and movements of goods, from entry to shipment. Modula WMS software is integrated into all the solutions at the Experience Centre, providing visitors with a practical demonstration of all its potential. For example, in the picking station area, the WMS monitor offers the option to check the item master data, quantities and stocks.
WMS can easily be confused with OS. Actually, they are two different kinds of software: WMS is the warehouse’s brain and manages all aspects of the supply chain, including integration with other technologies and various company ERPs, whereas the Modula OS system is the software used in human-machine interfaces (HMIs). This software is the user-friendly graphical interface on Copilot, the 10.4” tablet included in the machine, with which operators give commands to and interact with the warehouse.
In the VLM units on display at Fiorano, the sliding Copilot consoles can also be seen in action, with the option to move the console along the full length of the tray. As such, operators can take the Copilot with them, to keep it conveniently to hand anywhere in the tray.
Special, innovative solutions on display at the Experience Centre
Visitors to the Experience Centre can find out more about all the special solutions Modula has created, including:
– Modula Clean Room: a machine designed for use in clean rooms where cleaning rules are dictated by stringent ISO standards, especially useful in the pharmaceuticals, chemicals and electronics industries.
– Modula DD: a Lift warehouse with maximum payload and tray width, with a depth of 1,257 mm.
– Modula Climate Control: a temperature-controlled automated vertical lift module designed to store materials that are sensitive to variations in temperature and humidity or in refrigerated storage.
– Modula with integrated Robot: a Modula Lift with dual opposing bays, with an integrated ABB Cobot for direct picking from items in trays.
The showroom includes several Modula Slim systems with varying tray widths, used to store small items and mechanical parts. A Slim is ideal for companies with limited depths available and those who require a smaller investment. It also features a Modula HC with 3 pods that can handle hundreds of plastic crates, useful when the ceiling is too low for tall warehouses.
Another innovation presented at the Experience Centre is the Modula equipped with the new special MIR bay, designed for interaction with autonomous mobile robots (AMRs). This solution enables AMRs to pick up and deposit plastic crates directly into the Modula trays, completely eliminating the need for human intervention. An advanced system that represents a major step forward towards complete automation of warehouse management, improving efficiency and reducing operating times.
Experience Centre as the fulcrum of Modula’s present and future
Finally, in the prototype area of the facility, visitors can see the results of the research and design in the Modula world. One of the most curious innovations recently produced is definitely the Modula Next, a lift warehouse that works like a vending machine, offering operators only one compartment at a time, to present them with the product they need.
This innovative system reduces picking errors, especially between similar products, made possible by unique, tracked access using movable roller shutters. A further demonstration of the Modula approach: thinking about the future in a technological and digital way, while maintaining the focus on people and the component of the human experience.
The Modula Experience Centre in Fiorano Modenese is therefore an example of how advanced technology and innovative solutions can improve the efficiency of the supply chain, offering a tangible and practical vision of the potential of automated vertical warehouses and picking solutions.
But that’s not it for our new products. Behind the scenes, Modula is developing two revolutionary systems: one dedicated to e-commerce, designed to optimise handling of online orders; the other to store very bulky or heavy materials. Stay tuned to find out how these new solutions will further transform the future of logistics.
Want to know more?
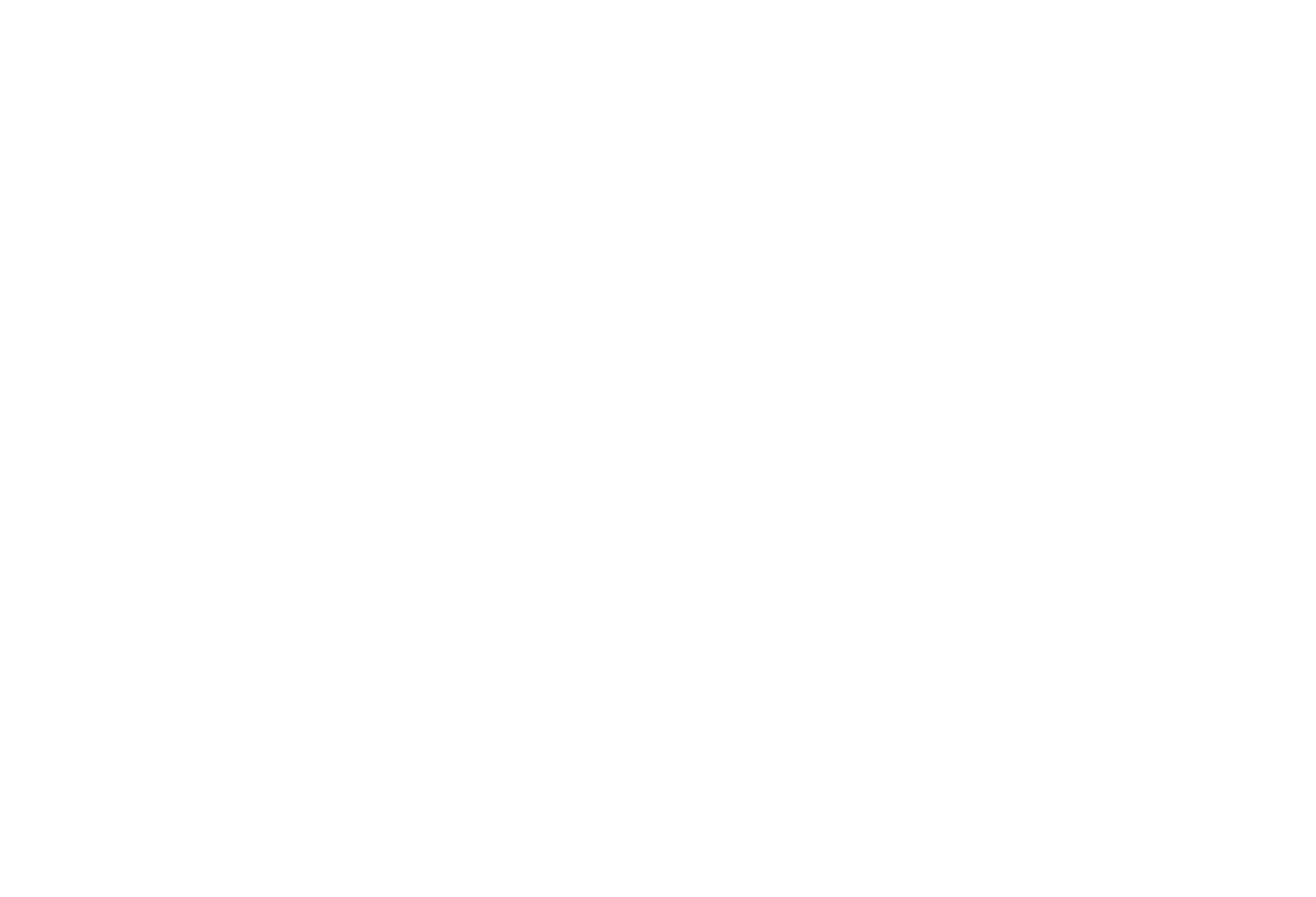