Despite unstable economic times, the e-commerce sector has been experiencing constant growth in Italy, Europe and in the Americas; it is estimated that this market will approach figures of $11 trillion in the USA alone by 2025.
However, few understand the dynamics behind the scenes of this enormous industry: most users of e-commerce services rarely even consider logistics in a warehouse and how it maintains efficiency and performance.
Behind every delivery, every package and every order are the operators who have to handle constant increases in stock levels, deliver speedily and without making mistakes, all with no increase in the workforce or the footprint of their warehouses.
Is there an ideal way to optimise these actions? Unfortunately not, no solution can solve everything with a click of the fingers. Actually, a warehouse survives on processed that are all intertwined with each other; to improve management and therefore increase numbers of shipments, or speed them up, a company needs to focus on the processes with the most impact, i.e. their strategy.
One strategic process is warehouse slotting, a method to organise warehouse space that can contribute to improving efficiency and productivity in all sectors and all companies, especially if they are equipped with automation systems such as automated vertical warehouses.
What is warehouse slotting and how is it useful
One of the processes with the greatest impact on operational management in the field of storage is the slotting of the warehouse. This logistics sequence optimises space, distance between items and the selection of materials and options in order to improve picking performance.
Efficient space management is essential in a warehouse and, as a rule, this is based on the correct placement of stock-keeping units (SKUs), each of which must be in its optimal slot to facilitate the work of the warehouse staff.
In turn, each slot is either fixed or random, depending on company requirements.
Fixed slotting is an inventory splitting method, used for products always kept in the same location. Random slotting tends to be used for products that are assigned to the first available picking zone.
Typically, fixed slotting is reserved for fast-moving or high-turnover items, whereas random slotting is used for items with a lower turnover.
Warehouse slotting: why?
Decisions on how to organise a warehouse frequently focus on the lowest possible running costs, by optimising picking locations. It results in better positioning of products in the picking area, fewer movements and less time wasted. It results in mapping and analysing logs and warehouse activities in order to understand which products to keep close and in which part of the warehouse.
There is always a golden zone in every warehouse, characterised by stock locations housing the most commonly moved items, i.e. those with the highest turnover. If this golden zone is compact in size, picking operations are immediately optimised.
The person optimising slotting normally bases their actions on position analyses and the ABC classification system used in logistics units. A good slotting analysis offers great savings in terms of warehouse management, as travel and picking times can be modified to improve picking times and efficiency will undoubtedly improve. The crucial point is in seeking to reduce as far as possible the total cost of picking and refilling your warehouse.
Three key best practices in slotting
Once these dynamics are known, let’s have a look at how an efficient slotting process can be created.
1. Organise inventory by SKU throughput
From sudden demand for beach balls and party supplies in summer, to the unmissable sales and discounts on Black Friday, seasonality can have a major impact on “SKU throughput” (the frequency of picking each item in a given period).
To respond to spikes in demand, a stock distribution strategy needs to be devised and created, to improve stock layout and maintain warehouse efficiency throughout the year.
Tips for inventory organisation to meet seasonal demand:
- Determine which products are or will be affected by seasonal demand
- Identify when spikes will occur
- Identify fast-moving items and place them near the shipping area for easy picking
- Aggregate frequently picked SKUs in the same storage area
2. Organise slot inventory by zone or equipment
Whether storing perishable goods in refrigerated areas (when it is necessary to adopt solutions such as Modula Climate Control) or storing high-value items in high-security compartments, identifying the correct zone for each item is critical to ensuring efficient inventory management and workplace safety.
How to divide inventory slotting by zones:
- Define picking zones in the warehouse
- Identify theright storage area for individual SKUs – for example, store perishable items in environmentally controlled areas and store flammable liquids in the flammables zone.
In addition to dividing the storage of items/SKUs by zones, inventory slotting can be optimised by grouping products based on the picking equipment used.
How to optimize stock distribution based on the picking tools and equipment used in the warehouse:
- Store heavy items in lanes close to each other
- Store small parts in another picking area, away from heavy stock
- If a forklift or scissor platform is used to pick stock, ensure that the aisles are wide enough for the equipment to pass.
3. Arrange stock based on product affinity analysis
Product affinity analysis is the process of analysing consumer behaviour to evaluate and identify which products are commonly purchased together.
Examples of kit or bundled items that can be sold together are ink cartridges and printers, wrapping paper and Christmas decorations, dried pasta and canned tomatoes, mobile phones and their cases.
Knowing which products are usually purchased together helps to optimise the division of stock in the warehouse, incentivises promotions and involves customers in cross-selling or upselling of relevant products.
To split inventory using product affinity analysis:
- Study consumer behaviour and purchasing patterns
- Store items in a bundle, with those that can potentially be sold together, next to each other.
In such cases, operators have to complete multi-order work, resulting in batch picking. Organising the entire warehouse according to items that could be included in multi-order picking greatly reduces picking time, because operators do not have to travel far and wide through the warehouse.
Modula vertical warehouses are the best solution in these cases, because the operator can remain at the same workstation to carry out batch picking, i.e. picking items of the same type at the same time, then sorting them into the various orders.
How can automation optimise warehouse organisation?
From reducing travel time to increasing workplace safety, warehouse splitting – combined with the introduction of automated equipment – is key to optimising inventory management for four reasons.
1 – Reduction in travel time
The routine of a warehouse operator includes searching for products within the warehouse so they can pick them; as such, stock location is essential to reduce the time required to pick products ready for shipment.
Warehouse slotting proves useful in situations like these: goods sold in a short time can be stored near the shipping area, resulting in faster picking and refilling.
A Modula automated warehouse is a clear example of an efficiency saving: travel time is virtually eliminated by having a concentrated golden zone in the warehouse. Reordering costs are then also easy to predict when you already have all picking, refilling and consumption of materials under control.
2 – Improvements in safety
As in any other workplace, accidents can unfortunately occur in a warehouse. Whether an operator might carelessly trip over a product left on the floor or be hit by an item falling off a shelf, a warehouse can be a breeding ground for injuries if goods are not stored properly.
Primarily, Modula automated warehouses store all products in trays and therefore prevent the risk of sudden falls from shelves. They also mean lighter goods can be stored at a higher level with heavier items lower down, which ensures a balanced and safer storage area.
3 – Improvements in goods handling
The estimated value of all global returns made in Europe in 2020 was €490 billion, as shown in a recent study by Twenga, comparing percentages of orders and returns in European countries. The research also highlighted the differences in digital buyers’ approaches to returning goods.
The highest numbers of returns were recorded in Germany (53%), followed by the Netherlands (52%), France (45%), Italy (43%), Spain (43%), the UK (40%), Belgium (38%) and Poland (32%).
With vertical warehouses, returns due to picking errors reduced exponentially; all it takes to reduce return rates and therefore improve customer satisfaction is to store the items in the right position (e.g. refrigerated containers for perishable foods).
Proper space division can improve the goods handling process. In an organised warehouse, the staff mainly work on picking, which adds value. They are not required to walk up and down the aisles searching for products, as automated vertical warehouses know the precise location of the items. As a result, they are more focused and make fewer picking mistakes; inventory management processes are also quicker, easier and more efficient.
4 – Maximisation of storage
Warehouse space in Italy can cost between €50 and €60 per square metre: in Milan, €55 per m2 per year; in Rome, €56 per m2 per year; in Florence, an average of €50 per m2 per year.
London, Paris and the cities of northern Europe are much more expensive, whereas costs can be lower in Poland, other countries in eastern Europe and Spain.
By designing and building efficient warehouse splitting, companies can save valuable space and focus operations in a smaller area closer to where they are needed. Of course, this contributes to reductions in total running costs, or can prevent needing to move to a larger warehouse
The net capacity of an automated vertical warehouse in the case of, for example, increasing slot volumes is very high, and detailed mapping of trays and their splitting into compartments using dividers and partitions results in levels of space optimisation that would be unthinkable with racking, shelving, mezzanines or traditional warehouse types.
You can think in terms of a golden zone and slotting even within the details of the warehouse itself: let’s imagine that we have the most frequently picked items (or those with the highest turnover) in the middle of a tray in an automated warehouse (also known as a vertical lift module). This means that they are in the closest part of the tray to the operator, which is therefore the easiest part to access. The distance an operator’s arm can reach and the tray depth are now variables to add into the equation used when positioning products.
The use of bins, containers or metal dividers to create multiple and highly detailed compartments can make picking operations even more efficient. These systems are normally used as part of WMS, but can also be used as modules alongside WMS as part of automated processes or manual preparation.
Automation and slot optimisation strategy
Warehouse organisation requires the constant gathering of information on consumer behaviour, data analysis and changes to inventory layout when required.
Using a Modula solution, together with logical slot optimisation, is an excellent choice to ensure appropriate development of warehouse dynamics, resulting in benefits from the perspective of both productivity and safety.
The user can monitor stock levels in real time, speed up order resolution times for both picking and replenishment, and avoid the accidental release of incorrect, obsolete, expired or pending products.
The advantages of a Modula automatic vertical storage system
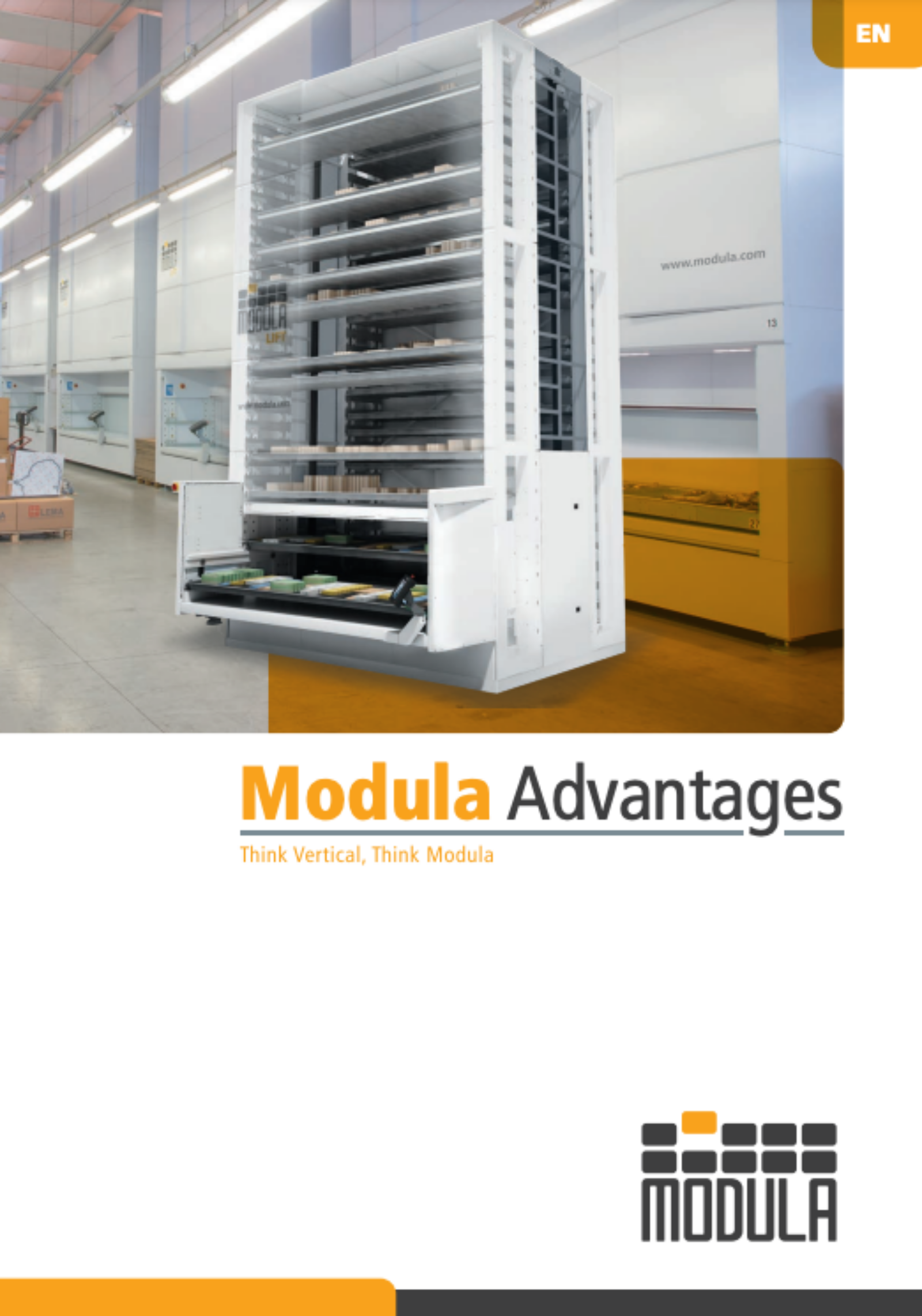