Modula automatic vertical warehouses are innovative solutions for automatic storage, specifically designed to contain any type of product: e.g. from small electronic components, up to much heavier, bulkier items.
This makes them the perfect solution for improving the internal management of the warehouse in any environment and industrial sector, even those that would seem most unlikely – like the Food & Beverage sector.
Modula vertical storage systems were created to organize, protect, and guarantee the cleanliness of stored goods and above all, to track every single item in stock. In addition, these systems also safeguard worker’s health and safety by operating based on the goods to person concept: personnel can operate the storage system from an ergonomic workstation without wasting time picking or placing items along aisles, shelves, and mezzanines or use ladders or the like with the consequent risks.
How to use the Modula vertical warehouses for bottling: from wineries to large logistics centres
Depending on the type of beverage, bottling can be done in a variety of ways and using various techniques. You can also have a variety of critical storage factors determined by the specific needs of the bottling location. Modula warehouses can be used, first of all, to service the bottling line, carrying out storage as their main activity. Storage of Spare Parts is an ideal example of this type of solution.
Indeed, whether they are used in the production processes of the bottling machines specifically, or whether they are implemented in the bottling process itself, the Modula vertical warehouses help you solve all your goods storage issues. Indeed, the Modula were chosen by various companies in the Beverage sector:
- wineries or food companies for the storage of different types of labels, caps, accessories and boxes for packaging. Thanks to the WMS software and the Copilot console, the needed label lot is sent to the bay and the inventory is automatically updated. The famous chocolate company Venchi as well as wineries like Ferrari, Colli del Soligo, Cantine Mezzacorona and Contri have at least one Modula storage system dedicated to labels. The same process has been adopted by several vinegar and olive oil producers, including Acetificio Ortalli, Acetaia Leonardi, Bunge and many others;
- companies in the design, construction and installation of integrated machines and systems for bottling, to increase the traceability of products in the warehouse, to reduce the number of employees, and to store the tools and spare parts for the machines;
- large hubs for bottling and distribution to reduce the time to look for and transport the parts used, and especially to reduce the operators’ physical exertions.
The major operators in the Food & Beverage sector have chosen Modula vertical storage systems
Vonpar Refrescos, a Coca Cola bottler in South America, stores the bulky bottle mold components in its Modula storage systems, using trays with widths over 4 meters.
Sidel, on the other hand, has a couple of Modula systems to serve its production line of packaging machines and beverage filling lines where the spare parts for the machines or finished components such as pistons and robotic arms are stored.
Barilla, in its Parma plant, uses external bay storage systems to store bulky pasta cutting dies; this bay model enables the automatic handling of the material since the pieces exceed 200 Kg.
Grissin Bon made a similar choice for the storage of spare parts intended for the maintenance of its production plants, as did Centro Carni in Padua and Morato Pane.
Thanks to Modula’s ability to operate at freezing temperatures, Inalca (Cremonini Group) purchased 3 of them, one of which operates inside a cold room.
Other well-known brands in the sector worldwide such as Krones, Sidel, ACMI, SACMI, and ELETTRIC 80 have chosen to adopt Modula storage systems both to serve production lines and store components and spare parts for maintenance: the goal in each case was to reduce the time necessary to locate and handle the parts needed, optimize the use of ground space, and decrease the physical stress on personnel.
Many companies have also adopted the Modula automatic storage systems for the storage of their finished or semi-finished products precisely to significantly reduce picking errors and decrease order preparation time. Spendrups, one of Sweden’s largest breweries stores low turnover products as well as the inventories of finished products such as cartons of beer or wine in Modula storage systems.
Another example is a Taiwanese food company, JIN DING, which eliminated picking errors and sped up order preparation operations thanks to a Modula solution.
Very often this result is achieved with the integration of visual aids such as Laser Pointers or subsystems like the Put To Light or Picking Cart. At this point we no longer speak of a single automation mechanism but of automation subsystems working cooperatively.
Food & Beverage: advantages of the Modula automatic vertical warehouses
Increase the quantity of items at the warehouse, while lowering storage space
With the Modula warehouses, you can exploit the space available in height, up to 16 metres, saving 90% of floor space.
You can customise the warehouse depending on your needs: for example, by determining the number of trays or how they are divided internally, so that you can store the maximum number of items possible within them. Instead, the load heights are managed automatically, meaning, the warehouse automatically positions the trays so there is minimum distance between one tray and another. You can always add or remove trays any time you want. In 16 m2, you can store 80 cubic metres of goods, for a total of 90,000 kg.
This means, you can use the Modula vertical warehouses to store thousands of labels along with the heavy materials used for production.
Bottling lines will never sit idle, thanks to Modula warehouses
Once started, bottling lines are difficult to stop, which is why it’s essential to have all the goods available and easy to find. With our automatic warehouses, this is quite simple, thanks to the Modula WMS, the software that allows you to manage your warehouse in real time via a simple PC interface. You can use the console to track the items stored within the warehouse, and send them to the delivery bay in just a few clicks.
Even the operators’ input-output search speed increases, with an increase in the overall efficiency of the whole warehouse and production centre. Line changeover times can be dramatically reduced, as operators no longer have to spend time searching for the correct parts for the next planned production operation.
The Modula warehouses can work both completely independently as stand alone, without interface with the company management, as well as very easily connected to your company system.
These are just two of the many advantages using the Modula automatic vertical warehouses. If you want to learn more, contact us!
Want to know more?
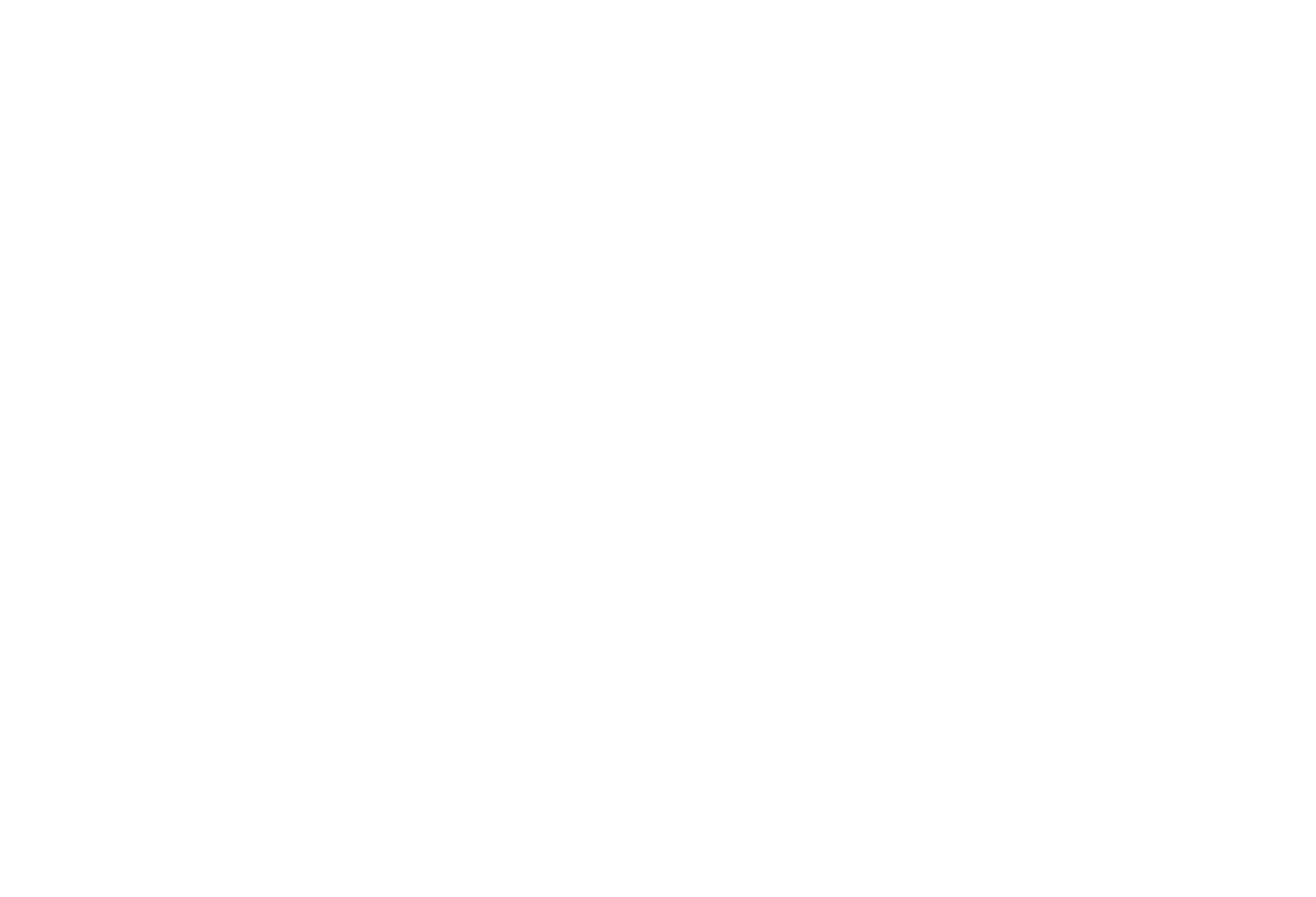